Технология электродуговой наплавки и обработки металла в процессе его нанесения на плоские поверхности
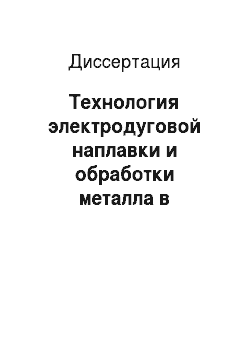
Аналогом технических решений в работе, могут служить результаты исследований, выполненные А. И. Бойко, В. А. Наливкина и Ю. Н. Казакова, суть которых сводится к совмещению наплавки с процессами фрезерования, шли7 фования, литьём, вытеснения металла и наложения вибраций. Однако эти способы полностью не решают проблему повышения эффективности наплавки плоских деталей, доля которых особенно велика… Читать ещё >
Содержание
- 1. АНАЛИЗ, СИСТЕМАТИЗАЦИЯ И РАЗРАБОТКА ОБЩИХ ПРИНЦИПОВ ФОРМООБРАЗОВАНИЯ ПЛОСКИХ ПОВЕРХНОСТЕЙ
- 1. 1. Плазменно-дуговой разряд для технологических целей
- 1. 1. 1. Существующие схемы совмещенных методов нанесения и обработки металла
- 1. 1. 2. Характеристика, виды и составные части электрических дуг
- 1. 1. 3. Формирование геометрических параметров при дуговых и плазменных процессах
- 1. 2. Анализ методов механической обработки наплавленного металла
- 1. 2. 1. Технологические возможности современных способов механической обработки
- 1. 2. 2. Основные явления при контактном взаимодействии
- 1. 1. Плазменно-дуговой разряд для технологических целей
- 2. 1. Выводы литературного обзора и постановка задач исследования
- 2. 2. Диалектика и системный подход к разработке технологии плазменно-дуговой наплавки плоских поверхностей
- 3. 1. Контактное взаимодействие режущего инструмента с наплавленным металлом
- 3. 1. 1. Особенности контактного взаимодействия инструмента с наплавленным металлом
- 3. 1. 2. Расчет усилия и времени образования контакта при терморезании
- 3. 2. Тепловая обстановка в технологической зоне
- 3. 2. 1. Расчет температурного режима процесса наплавки для выбора условий резания
- 3. 2. 2. Источники нагрева
- 3. 2. 3. Тепловой баланс
- 3. 2. 4. Выбор места размещения инструмента
- 3. 3. Влияние остаточных деформаций и напряжений на формирование припуска
- 3. 3. 1. Классификация
- 3. 3. 2. Механизм образования и развития остаточных напряжений и деформаций
- 3. 3. 3. Теоретическое обоснование снижения деформаций и остаточных напряжений путем снятия наплавленного слоя
- 3. 4. Особенности механизма стружкообразования при обработке металла в зоне высоких температур
- 3. 4. 1. Состояние наплавленного металла в технологической зоне стружкообразования
- 3. 4. 2. Разработка схемы резания металла в ходе его нанесения
- 3. 5. Кинетический анализ схемы терморезания наплавленного слоя путем возвратио-качательного движения резца
- 4. 1. Обоснование целесообразности применения ЛЭМД в качестве привода режущего инструмента
- 4. 1. 1. Анализ приводов и устройств для механической обработки
- 4. 1. 2. Расчет основных элементов ЛЭМД
- 4. 1. 3. Окончательные требования к приводу режущего инструмента и его конструкция
- 4. 2. Инструмент для терморезания наплавленного металла в процессе его нанесения
- 4. 2. 1. Методика исследования стойкости режущего инструмента
- 4. 2. 2. Анализ условий резания и работоспособности режущего инструмента
- 4. 2. 3. Выбор материала режущего инструмента при терморезании
- 4. 2. 4. Работоспособность и характер изнашивания инструмента
- 5. 1. Исследование шероховатости и неровностей наплавленной и обработанной поверхности
- 5. 1. 1. Методика исследования
- 5. 1. 2. Результаты исследования качества формообразования
- 5. 2. Исследование остаточных напряжений и деформаций
- 5. 2. 1. Методика исследования остаточных напряжений
- 5. 2. 2. Результаты исследования остаточных напряжений и деформаций
Технология электродуговой наплавки и обработки металла в процессе его нанесения на плоские поверхности (реферат, курсовая, диплом, контрольная)
Актуальность проблемы. Недопустимо низкое качество деталей и хронически нарастающий дефицит запчастей, создают большую напряжённость в ремонтном производстве, масштабы которого становятся соизмеримыми с первичным изготовлением.
Поэтому особую значимость обретает проблема совершенствования существующих технологий, что особенно актуально в условиях экологических потрясений и социально-экономической запущенности. Но уже на стадии заготовительного производства из-за повышенных припусков, высоких остаточных напряжений и деформаций закладываются условия неконкурентноспособности продукции.
В этом смысле детали составной конструкции сулят большую экономию материальных и денежных ресурсов. Их изготовление все чаще сопровождается освоением технологии наплавки с использованием плазменных и дуговых разрядов (ПДР).
Такой подход, когда на недорогую заготовку или изношенную деталь, выполняющую функцию заготовки, наносят рабочий элемент с заданными свойствами, создаёт реальные предпосылки для наиболее полной реализации всех преимуществ, присущих каждому из материалов, входящих в состав детали.
Желаемая цель наплавки — получить изделие в виде законченных форм, размеров, дизайна и заданных функциональных свойств. Но специфика и спонтанный характер кристаллизации наплавленного металла вызывают дефекты формообразования, химическую и структурную неоднородности металла, трещины, высокие значения твёрдости, деформации и неровности поверхности, что затрудняет механическую обработку и сводит к нулю все достоинства наплавки. Особенно эти вопросы характерны для плоских и длинномерных деталей ограниченной толщины, которые составляют значительную долю в номенклатуре восстанавливаемых деталей машин и инструментов.
В последние годы проявляется тенденция к применению совмещённых методов наплавки. Из их критического анализа существующих технологий следует: 6.
•традиционные методы наплавки не имеют резервов повышения качества формообразования и производительности процесса наплавки плоских поверхностей, особенно длинномерных деталей с тонкой стенкой и изготовленных из высоколегированных материалов;
•регламентация температурно-временных параметров наплавки не позволяет в широких пределах маневрировать режимами нанесения и гибко управлять процессами деформаций наплавленных деталей. Особенно к этим параметрам чувствительны высоколегированные длинномерные детали с относительно тонкой стенкой. •.
•в связи с трудностью механической обработки наплавленного металла с высокой твёрдостью на практике исходят не из качества наплавки, а из условия лучшей из её лучшей обрабатываемости;
•потенциальные возможности наплавки не используются в полной мере, особенно для плоских поверхностей. Часто возникает множество противоречивых толкований и суждений по поводу применения совмещённых методов наплавки.
Отмеченные обстоятельства вызваны отсутствием данных о явных преимуществах существующих процессов терморезания.
На решение вопросов качественного формообразования наплавки плоских поверхностей и направлена данная диссертация.
Работы А. И. Бойко, Б. М. Березовского, П. В. Гладкого, А. Г. Григорьянца, H.H. Дорожкина, В. А. Деева, В. А. Ефимова, Е. Л. Емельянова, И. В. Кудрявцева, В. Г. Вердникова, Т. К. Копенёва, В. В. Кудинова, B.C. Клубникина, В. Н. Лясникова, В. В. Меликова, Н. М. Новожилова, В. А. Наливкина, Б. Е. Патона, В. Н. Подураева, В. П. Пономарёва, H.H. Рыкалина, А. Н. Резникова, Э. В. Рыжова, A.B. Сидорова, А. Г. Суслова, Е. М. Трента, И. И. Фрумина, М. А. Шатерина, Б. Ф. Якушина, П. И. Ящерицина и др. позволили создать эмпирический базис, направленный на поиск положительных эффектов от применения процесса терморезания.
Аналогом технических решений в работе, могут служить результаты исследований, выполненные А. И. Бойко, В. А. Наливкина и Ю. Н. Казакова, суть которых сводится к совмещению наплавки с процессами фрезерования, шли7 фования, литьём, вытеснения металла и наложения вибраций. Однако эти способы полностью не решают проблему повышения эффективности наплавки плоских деталей, доля которых особенно велика для дорожно-строительной техники, ж/д транспорта, металлургического оборудования и т. п.
Цель: повысить эффективность технологии изготовления, восстановления и упрочнения изделий с плоскими поверхностями за счёт тепла, генерируемого электродуговыми разрядами, при совмещении процесса нанесения металла с его лезвийной обработкой.
Для достижения этой цели решаются следующие задачи:
• систематизация .и структурирование эмпирического базиса по наплавке и обработке металла лезвийным инструментом и на этой основе разработка теоретических предпосылок по совершенствованию процессов формообразования при электродуговой наплавке плоских поверхностей;
• обоснование положительных эффектов термосилового резания металла с единых общих теоретических позиций контактного взаимодействия, тепловой обстановки и термодеформационных процессов в технологической зоне;
• разработка общих принципов, моделей, функциональных схем активного управления формообразованием при наплавке плоских поверхностей и исследование механизма, закономерностей и параметров качества поверхностного наплавленного и обработанного слоя;
• определение наиболее рациональных схем, технологических режимов и возможностей при электродуговой наплавке плоских поверхностей со снятием стружки в едином технологическом цикле и оценка технико-экономической целесообразности её применения.
Научная новизна.
1. Выявлены технологические возможности и рациональные условия использования тепла, генерируемого сварочной дугой для обработки металла в процессе его нанесения на плоские поверхности.
2. Установлена возможность снижения уровня деформаций в ходе наплавочного процесса за счет снятия металла лезвийным инструментом в зоне аустенитного превращения. 8.
3. Согласованы технологические режимы наплавки с режимами резания и определено рациональное место врезания режущего инструмента.
4. Обоснованы технологические параметры нанесения металла и снятия стружки по критериям шероховатости, поверхностного слоя и стойкости режущего инструмента.
На защиту выносятся:
• теоретические обобщения, содержательные логические структуры, классификаторы, позволяющие получить расчётную модель, адекватно отражающую условия контактного взаимодействия лезвийного инструмента с наплавляемым металлом- 1.
• новые схемы и режимы формообразования металла, позволяющие вести его обработку в процессе нанесения на плоские поверхности и снизить величину остаточных напряжений и деформаций;
• новые устройства, наплавочное оборудование, оснастка и их приводы на базе линейного электромагнитного двигателя (ЛЭМД), позволяющие вести процесс обработки при наличии флюсовой корки и получать слои с заданной шероховатостыо при высокой стойкости режущего инструмента.
Техническими средствами, используемыми в исследованиях, были мерительные, контрольные приборы и инструменты, твердомеры (ТП-2, ТК-2, ПМТ-5), оптические и, инструментальные микроскопы (МИМ -7, МИМ — 8, УЙМ—23), дефектоскопы (М-127, ДМП-2), потенциометр (ПП-63), электроинтегратор ЭГДА-9/60, разрывная машина МР-50, маятниковые копры (МК-30, МК-0,5), машины трения (СМЦ-2), профилограф «Талисурф» и М-201.
Наплавка проводилась на универсальной экспериментальной установке, оснащённой многоэлектродной головкой, дозирующими и резцедержательны-ми устройствами для вытеснения и резания металла с приводом от линейного электромагнитного двигателя (ЛЭМД), механизмом сканирования присадочных и электродных проволок.
В качестве источников питания использовались выпрямители ВС-600, ВДУ 1200, преобразователь ПСО-500.
ОБЩИЕ ВЫВОДЫ.
1. В результате анализа научно-технической информации в области наплавочных процессов установлено, что применение существующих методов терморезания становится проблематичным из-за наличия флюса и флюсовой корки на поверхностях деталей, отжима инструмента, высоких значений деформаций и стесненных условий наплавки.
2. На основе построенных моделей теплового состояния наплавленного металла и его контактного взаимодействия с режущим инструментом обоснована возможность применения технологического тепла сварочной дуги для повышения эффективности механической обработки плоских наплавленных поверхностей в едином технологическом цикле.
3. На основе термодинамики кристаллизации наплавляемого металла и кинетики процесса стружкообразования предложена новая схема снятия металла путем возвратно-качательного движения инструмента в интервале температур аустенитного превращения.
4. Установлены закономерности формирования рельефа наплавленной и обработанной поверхности в зависимости от режимов наплавки и частоты движения инструмента (не менее 1. .3 Гц).
5. Рассмотрен механизм и установлены закономерности формирования остаточных напряжений и деформаций при совмещенном методе наплавки. Расчетным путем определена и экспериментально подтверждена принципиальная возможность снижения уровня деформаций в процессе наплавки за счет снятия припуска при температуре (0,3 -ь 0,4) от температуры плавления.
6. Обоснована приоритетная роль импульсного характера резания и целесообразность применения в качестве привода режущего инструмента линейного электромагнитного двигателя, что позволило вести процесс резания с большим припуском (в 1,5.2,0 мм), при размещении резца на расстоянии 2535 мм от сварочной ванны.
7. Разработаны технологические рекомендации по выбору основных факторов режима нанесения и обработки металла (ток наплавки, температура в зоне.
148 резания, частота возвратно-качательного движения), при которых достигается минимальный уровень шероховатости (15.40 мкм) и максимальная стойкость режущего инструмента (75.100 мин). 8. При внедрении результатов работы расчет технико-экономической эффективности показал, что затраты при совмещении процессов наплавки и лезвийной обработки снизились в 2,3 раза по сравнению с раздельным методом восстановления.
Список литературы
- Авдеев М.В. О распределении температуры в сварочной ванне. — «Сварочное производство», 1974. № 11.
- Акулов А.И., Бельчук Г. А., Демянцевич В. П. Технология и оборудование сварки плавлением. М.: Машиностроение. 1977. 432 с.
- Армарего И.Д., Браун Р. Х. Обработка металла резанием / Пер. с англ. В. А. Пастухова. М.: Машиностроение, 1977 — 325 с.
- Арсентьев П.П., Коледов JI.A. Металлические расплавы и их свойства. М.: Металлургия. 1976. 376 с.
- Бабичев А.П. Вибрационная обработка деталей. М.: Машиностроение. 1974.134 с.
- Беляковский В.П., Семофалов Ю. И. Применение плазменно-механической обработки при восстановлении деталей металлургического оборудования // Тез. Докл. XI конф. Инструментальщиков Урала. Перьм, 1982 .С. 16.
- Березовский Б.М. Математическое моделирование формирования горизонтальных швов на наклонной плоскости. //Автомат. Сварка. 1988, — № 1С. 26−31.
- Березовский В.М. Смачивание и растекание сварочной ванны на поверхности металла // Автоматическая сварка № 10. 1983. С. 81−84
- Биргер И.А. Остаточные напряжения. М.: Машгиз, 1963. — 187 с.
- Бобров В. Ф., Иерусалимский Д. Е. Резание металлов самовращающимися резцами. М.: Машиностроение. 1972 112 с.
- Богоявленский К.Н., Рис В.В. Экономичные методы формообразования деталей. Л, Лениздат, 1984. — 144 с.
- Бойко Н.И. Повышение эффективности механической обработки наплавленного металла за счет тепла, генерируемого сварочной дугой. Диссертация. док. техн. наук. Самара: Куйбышевский политехи, ин-т. 1991. — 540 с.150
- Бойко Н.И. Термомеханическое упрочнение наплавленного металла. Ростов на — Дону: РИИЖТ. 1986. — 185с
- Бойко Н.И. Фрезерование широкослойной наплавки цилиндрических деталей. Ростов на — Дону: РИИЖТ. 1987. — 74с.
- Болдырев A.M., Дорофеев Э. Б., Петров A.C. Способ электродуговой сварки A.C. 584 996 от 17.04.76.
- Буки A.A., Шилов A.A. Математическая модель проплавления основного металла при электродутовой сварке // Сварочное производство. 1975. Ижевск: ИМИ. С. 23−37.
- Вердников В.Г., Копенев Т. К. Производительность многоэлектродной наплавки при восстановлении изношенных деталей строительных машин. /Сварочное производство. 1972. N 4.
- Веселовский О.Н. Низкоскоростные линейные электродвигатели. Дис. д.т.н. Новосибирск. 1979 366 с.
- Виноградов В.Н., Сорокин Г. М., Албагачиев А. Ю. Изнашивание при ударе. М.: Машиностроение. 1982. — 192 с.
- Возможность применения электроконтактного нагрева для получения соединений в твёрдой фазе. //Сварочное производство 1986 № 6 с 7 8.
- Галин Г. А. Контактные задачи теории упругости и вязкоупругости. М.: Наука. 1980 303 с.
- Гаркунов Д.П. Триботехника. М.: Машиностроение. 1985 434с.
- Гельман A.C. Основы сварки давлением М.: Машиностроение. 1970, — 312 с.
- Головизнин В.М., Самарская Е. А., Чуданов В. В. Дифференциальные уравнения .1987. Т.23. № 7. С. 1143.
- Горячева И.Г., Добычин H.H. Контактные задачи в трибологии. М.: Машиностроение. 1988,-256 с.
- Грохольский Н.Ф. Восстановление деталей машин и механизмов сваркой и наплавкой. М.: Машгиз. 1962. — 275 с.151
- Дегтерёв С.П., Смирнов B.B. Повышение Эффективности процессов дуговой сварки и наплавки с поперечными колебаниями электрода.Л.:ЛДНТП. 1987.20 с.
- Дёмкин Н.Б. Контактирование шероховатых поверхностей.М.:Наука. 1970. 228 с.
- Дёмкин Н.Б., Рыжов Э.В Качество поверхности контакта деталей машин. М.: Машиностроение. 1981 244 с.
- Демянцевич В.П., Зависимость провара от режима сварки под флюсом / Сварочное производство, № 7,1974
- Демянцевич В.П., Мапохин В. И. Особенности движения жидкого металла в сварочной ванне при сварке неплавящимся электродом // Сварочное производство. 1972. № 10. С. 1−3.
- Дехтярь Л.И., Игнатьков Д. А., Андрейчук В. К. Выносливость валов с покрытиями. Кишинёв: Житница, 1983. — 176 с.
- Дорожкин H.H., Петюшев H.H. Дуговая газопорошковая наплавка. Минск. Беларусь. 1989. 94 с.
- Доценко Н.И. Восстановление автомобильных деталей сваркой и наплавкой. М.: Транспорт. 1972. — 197 с. 13
- Дрозд М.С., Маталин М. М., Сидякин Ю. И. Инженерные расчёты упруго-пластической контактной деформации. М.: Машиностроение. 1986. 224с.
- Дьяченко П.Е. Исследование зависимости микрогеометрии поверхности от условий механической обработки. М.: изд. АН СССР. 1949. — 128 с.
- Еланский Г. Н. Строение и свойства металлических расплавов. М.: Металлургия. 1991. 160 с.
- Емельянов Н.П. Многоэлектродная электродуговая и электрошлаковая наплавка под флюсом. //Труды ВНИИЖТа. Вып.239.М.: Трансжелдориздат. 1962.-С. 4−12.
- Ерохин A.A. Основы сварки плавлением. М.: Машиностроение. 1973. 448 с.
- Зорев Н. Н. Вопросы механики процессов резания металлов. М.: Машгиз, 1956 368 с.
- Иванов В.И. Повышение эффективности обработки износостойких сталей с использованием технологического тепла наплавки. Автореф. Дис. канд. техн. наук. Запорожье, 1969. — 21 с.
- Иващенко Г. А. Выбор материала режущей части при обработке наплавленного слоя 11 Ремонт машин и технология металлов: Сб. тр. МИИСП. 1975. -Т. XII, вып. 4, ч. 1.-С. 82−84.
- Иващенко Г. А., Пилипеенко Н. С. Зависимость между скоростью резания и стойкостью резца при точении наплавленного металла.// Технология восстановления деталей сельскохозяйственной техники: Сб. тр. МИИСП. -1977. ТХ1У. Вып. 8.-С. 48−51.
- Исаев А.И. Процесс образования поверхностного слоя при обработке металлов резанием. М.: Машгиз. 1950. — 358 с.
- Казимиров A.A., Недосека А. Я., Лобанов А. И., Радченко И. С. Расчет температурных полей в пластинах при электросварке плавлением. Справочник. Киев: Наукова думка. 1968. — 830 с.
- Калашников А. И Восстановление и упрочнение деталей машин автоматической наплавкой в среде защитных газов. Саратов: СГУ, 1978. — 176 с.
- Каракозов Э.С. Соединение металлов в твёрдой фазе. М.: Металлургия. 1976. 263 с.
- Карлсоу Г., Егер Д. Теплопроводность твердых тел. М.'Машиностроение. -1973.-560 с.
- Китаев A.M., Китаев Я. А. Справочная книга сварщика. М.: Машиностроение, 1985. 1985. — 256 с.
- Клауч Д.Н., Кириллов О. М., Редин А. П. Перспективы применения металлорежущего инструмента с износостойкими покрытиями. Технология, организация производства и управления (ЦНИИТЭИ тяжмаш),№ 17.1988. -40с.
- Клименко В.М., Шаповал В. И. Вибрационная обработка металлов давлением. Киев: Техника. 1977. 128 с.
- Клименко С.А. Технологическое обеспечение качества и эксплуатационных свойств наплавленных деталей точением. / Дис. к.т.н. Киев. 1988. -270 с.153
- Койре В.Е. Обработка деталей, наплавленных сормайтом с подогревом срезаемого слоя, //Весник машиностроения. 1960. № 10. — С.72−74.
- Комаров В.А. Некоторые вопросы формирования шероховатости в зависимости от технологических факторов обработки лезвийным инструментом: Автореф. Дис. канд. техн. наук. М. 1978. — 16 с.
- Комбалов B.C. Влияние шероховатости твёрдых тел на трение и износ. М.: Наука 1974.- 112 с.
- Коновалов Е.Г., Сидоренко В. А., Соусь A.B. Прогрессивные схемы ротационного резания металлов. Минск: Наука и техника. 1972 272 с.
- Конструкторско-технологическое обеспечение качества деталей машин / В. П. Пономарёв, A.C. Батов, A.B. Захаров и др. М.: Машиностроение. 1984- 184 с.
- Копенев Т.К. Исследование параметров режима многоэлектродной наплавкой применительно к восстановлению изношенных деталей строительных машин. Автореф. дис. канд. техн. наук. М.: МАДИ. 1971. 156 с.
- Коперсак Н.И., Сливинский A.M., Духно В. М., Каховский Ю. Н. Температурный режим сварочной заины. -" .Автоматическая сварка", 1973, № 7.
- Коротких М.Т., Шатерин М. А., Лаевский Г. Б. Плазменно-механическое фрезерование труднообрабатываемых материалов. Л.: ЛДНТП, 1988.- 24 с.
- Костецкий Б. И., Носовский И .Г., Бершадский Л. И. Надежность и долговечность машин. К.: Техшка. 1975. — 408 с.
- Кочергин К.А. Сварка давлением. Л., Машиностроение. 1972.-216 с.
- Крагельский И.В., Добычин М. Н., Комбалов B.C. Основы расчетов на трение и износ. М.: Машиностроение. 1977.-528 с.
- Крокстон К. Физика жидкого состояния/ Пер. с англ. М.: Мир. 1973, — 400 с.
- Кувшинский В.В., Шабашов С. И. Чистовое скоростное толчение стали. // скоростная обработка металлов. Сб. тр. И.: Свердловск, 1950. — С. 96 -101.
- Кудинов В.В. Плазменные покрытия. М.: Машиностроение. 1977 184 с.
- Кумабэ Д. Вибрационное резание//пер. С яп. С. Л. Масленникова /под ред. И. И. Портнова, В. В. Белова. М.: Машиностроение. 1985. — 424 с.154
- Кунин B.C. Опыт внедрения плазменно-механической обработки. Д.: ЛДНТП. 1982. 28 с.
- Леви Э., Панцер М. Электромеханическое преобразование энергии. М.: Мир. 1969−556 с.
- Лесков Г. И. Электрическая сварочная дуга. -М.: Машиностроение. 1970.-335с.
- Литовченко С.С. Исполнительные устройства, изменяющие силовые поля // Техника средств связи: Серия ТПС. М.: Связь 1985 -вып. 7. С. 98 -109
- Лоладзе Т.Н. Прочность и износостойкость режущего инструмента. М.: Машиностроение. 1982. 320 с.
- Лыков A.B. Теория теплопроводности. М.: Высшая школа, 1967. — 600 с.
- Львицын A.B. Разработка и исследование электромагнитных двигателей для прессового оборудования. Дис. к.т.н. М. МЭИ. 1982−267с.
- Львицын A.B., Мошкин A.B., Угаров Г. Г. Режим работы линейных электромагнитных двигателей //Вопросы теории и проектирования электрических машин. Саратов: СГУ. 1985 вып. 5.
- Львович А.Ю. Электромеханические системы. Л.: ЛГУ. 1989 296 с.
- Любов Б.Я., Соболь Э. И. Процессы теплопереноса при фазовых превращениях под действием интенсивных потоков энергии// Инж.-физ. журн. 1983. Т.45.№ 4. С. 670.
- Люболенский С.П. Технологические остаточные напряжения и управление ими при механической обработке резанием с целью повышения износостойкости высокоточных деталей: Автореф. дис. канд. техн. наук. М.: -1983 — 14 с.
- Любчик М.А. Оптимальное проектирование силовых электромагнитных механизмов. М.: Энергия. 1974 392 с.
- Макаров А.Д. Оптимизация процессов резания. М.: Машиностроение. 1976−278 с.
- Маталин A.A. Микротвердость и износоустойчивость поверхности. // Качество обработанных поверхностей. Докл. второй Ленинград, конф. 1953 г. -М.: Машгиз. 1954. С. 58−72.155
- Медиков В.В. Многоэлектродная наплавка. М.: Машиностроение. 1988. -144 с.
- Миркос Р.П. Применение безотходных и малоотходных технологий в машиностроении // Обзор Новосибирский межотраслевой цент НТП. Новосибирск. 1986. 26 с.
- Михеев М.А., Михеева И. М. Основы теплопередачи. М.:3нание., 1977. -346 с
- Могилев В.К., Лев О.И. Справочник литейщика. М.: Машиностроение, 1988.-271 с.
- Найдич Ю.В. Контактные явления в металлических расплавах. К.: Наук. Думка, 1972, — 196 с.
- Наливкин В.А. Исследование и применение механизированной и автоматической наплавки для централизованного восстановления деталей машин. -Саратов: Приволж. кн. изд-во, 1969, — 124 с.
- Наплавка. Опыт и эффективность применения. // Сб. научн. ст. /Под ред. П. В. Гладкого Киев: ИЭС им. Е. О. Патона АН УССР. 1985. — 108 с.
- Наплавка при изготовлении деталей машин и оборудования. //Сб. научн. ст. / Под ред. П. В. Гладкого Киев: ИЭС им. Е. О. Патона АН УССР. 1986. -122 с.
- Новожилов В.И., Бояркин A.M. Применение резцов из эльбора и гексанита при обработки восстановленных деталей. // Алмазы и сверхтвердые материалы. Сб. № 10 1979. — С. 4 — 5.
- Оборудование и материалы для наплавки: Сб. научн. Тр. // АН УССР. ИЭС им. Е. О. Патона: под ред. В. П. Гладкого и др. Киев: 1990. — 124 с.
- Олейник И. В. Кычин В.П., Луговской А. Л. Поверхностное динамическое упрочнение деталей машин. К.: Техника. 1984. — 151 с.
- Оптимальное управление точностью обработки деталей в условиях АСУ. / В. И. Кантор, О. Н. Анисифиров, Г. Н. Алексеева и др. М.: Машиностроение, 1981.-256 с.
- Пархимович Э.М. Сварка и наплавка в ультразвуковом поле. Мн.: Наука и техника. 1988. -207 с. 4.9.156
- Пацкевич И.Р. Исследование и применение вибродуговой наплавки. М.: Машиностроение, 1964.-232 с.
- Пацкевич И.Р., Деев Г. Ф. Поверхностные явления в сварочных процессах.- М.: Металлургия, 1974 .- 121 с.
- Подураев В.Н. Обработка резанием с вибрациями. М.: Машиностроение. 1970 — 350с.
- Попов Г. Я., Савчук В. В., Контактная задача теории упругости при наличии круговой области контакта с учётом поверхностной структуры контакти-руемых тел. Изд. АН СССР, МТТ, 1971, № З.С. 80−87.
- Попов Е. А. Основы теории пластического деформирования. М.: Машиностроение. 1968. — 283 с.
- Прогрессивные методы обработки резанием Сб. материала семинара / под ред. И. И. Олейникова и М. А. Шатерина. Л.: ЛДНТП. 1981. 94 с. 10.
- Размышляев А.Д. Исследование скорости движения жидкого металла в сварочной ванне при дуговой наплавке под флюсом. //Сварочное производство. 1979. № 9. С. 3−5.
- Рвачёв В.Л., Проценко B.C. Контактные задачи теории упругости для неклассических областей. Киев: Наукова думка. 1977 — 236 с.
- Резников А.Н. Исследование теплофизики процесса резания с плазменным подогревом обрабатываемого материала: Автореф. к.т.н. Тбилиси. 1983. 23 с.
- Резников А.Н. Теплофизика процесса механической обработки материалов.- М.: Машиностроение. 1981. 280 с.
- Резников А.Н., Резников Л. А. Тепловые процессы в технологических системах М.: Машиностроение. 1990. 288 с.
- Рудзит Я.А. Микрогеометрия и контактное взаимодействие поверхностей. Рига: Зинатне, 1975 216 с.
- Рыбакова Л.М., Куксенова Л. И. Структура и износостойкость металла. -М.: Машиностроение. 1982. 212 с.
- Рыжов Э.В., Суслов А. Г., Фёдоров В. П. Технологическое обеспечение эксплуатационных свойств деталей машин М.: Машиностроение. 1979. — 176 с. 11.1. Рыкалин H.H. Расчеты тепловых процессов при сварке. -М.: Машиностроение. 1951.-295 с.
- Рыкалин H.H., Кулагин И. Д., Николаев A.B. Тепловые характеристики взаимодействия плазменной струи с нагреваемым телом Автоматическая сварка, 1963,№ 6, с 3.
- Ряшенцев Н.П. и др. Аппроксимация статических тяговых характеристик силовых электромагнитов постоянного тока. Электрические машины ударного действия. Новосибирск: Наука. 1969 С 135−140.
- Ряшенцев Н. П. Ковалёв Ю.З. Динамика электромагнитных импульсных систем. М.: Наука. 1974 188 с.
- Ряшенцев Н.П., Угаров Г. Г., Львицын A.B. Электромагнитные прессы. -Новосибирск.: наука, Сиб. Отделение, 1989. 216с
- Ряшенцев Н.П., Угаров Г. Г., Стецко A.A. Расчёт силы тяги насыщенного электромагнита //Вопросы теории и проектирования электрических машин. Саратов: СГУ. 1978 С. 75−80.
- Сафронов. Формирование высоких триботехнических свойств изделий наплавкой. Кишинёв: Картя Молдовеняскэ. 1989 г. 286 с.
- Сергацкий Г. И., Дубовецкий C.B. Системы разомкнутого управления формирования шва при дуговой сварке (обзор) // Автоматическая сварка. 1986. № 6. С.37−48.
- Сипайлов Г. А., Лоос A.B. Математическое моделирование электрических машин. М.: Высшая школа. 1980 176 с.
- Смелягин А.И. Теория, синтез и исследование механизмов и машин с электромагнитным приводом. Дис. д.т.н. Новосибирск 1987−365 с.
- Сорокин Г. М. Виды износа при ударном контактировании поверхностей. / /Машиностроение". 1974. № 3. С. 89−94.
- Старков В.К., Кузин В. В. Режущий инструмент из нитридо-кремниевой керамики. М., 1988. -с. 60.
- Суслов А.Г. Технологическое обеспечение параметров состояния поверхностного слоя деталей. М.: Машиностроение. 1987.- 208 с.
- Суханов В.Е., Грушевский A.B., Суровцев А. П. Расчёт усилия и времени образования контакта при диффузионном соединении металлов //Сварочное производство. 1989. № 3. С. 37−40
- Сущенко А.П., Сущенко С. А. Многоэлектродная наплавка цилиндрических деталей малого диаметра. / Сварочное производство. 1968. N 7.
- Таран В.Д. Сварка магистральных трубопроводов и конструкций. М.: Недра. 1970−374с.
- Татаркин Е. Ю. Фёдорова Н.П., Ситников A.A. Определение межоперационных размеров при изготовлении деталей с покрытиями//Сварочное производство, 1991. № 1. С. 5−6.
- Теоретические и технологические основы наплавки. Наплавка деталей оборудования металлургии и энергетики. Сб. научн. ст. /Под ред. И.И. Фру-мина. Киев: ИЭС им. Е. О. Патона АН УССР. 1980. — 156 с.
- Теория расчёта и конструирования деформирующего и формообразующего инструмента./ Сб. Научн. Трудов. Куйбышев: КПтИ 1979. 171 с.
- Теплофизические свойства стали / О. И. Островский, В. А. Григорян, В. Н. Станюкович, С. Ю Денисов // Сталь. 1988, № 3, С. 37−39.
- Трент Е.М. Резание металлов. / Пер. с англ. Г. И. Айзенштока. М.: Машиностроение. 1981. 3 5. С. 16. 1980 — 263 с.
- Тыткин Ю.М., Кузмин Г. С. Анализ движения металла в хвостовой части ванны при сварке на форсированных режимах. «Сварочное производство» 1976, № 9.
- Убеллоде А.Р. Расплавленное состояние вещества / Пер. с англ. М.: Металлургия. 1982 .- 376
- Угаров Г. Г. Импульсные линейные электромагнитные двигатели с повышенными силовыми и энергетическими показателями. Диссертация. д. т.н. Новосибирск. 1992 491 с.
- Углов A.A., Смуров И. Ю. Гуськов А.Г. О рсчёте плавления металла концентрированными потоками энергии // Физика и химия обработки материалов. 1985. № 3. С.З.
- Урицкий М.Л., Кравченко С. С. Плазменно-механическая обработка -материалов //Машиностроение159
- Федонин В.Н., Кожевников В. Ю. Электромагнитные прессы (теория и расчёт).-Саратов: Изд-во Саратовского ун-та. 1990.-80 с
- Фильчаков П.Ф., Панчишин В. И. Интеграторы ЭГДА. Моделирование потенциальных полей на элеиропроводной бумаге. Киев: АН УССР. 1961. -170 с.
- Френкель Я.И. Кинетическая теория жидкостей. Изв. АН СССР. 1945
- Фридман Я.Б. Механические свойства металлов .- М.: Машиностроение. 1974.-Т.1 -472 с.
- Фрумин И.И. Основы технологии механизированной наплавки. М.: Проф-техиздат. 1961. — 303 с.
- Харламов Ю.А. Методика расчёта толщины покрытия // Сварочное производство, 1987. № 9. С. 9−11.
- Хасуй А., Миричаки О. Наплавка и напыление. М.: Машиностроение. 1985.-240 с.
- Хасуй Техника напыления. М.: Машиностроение. 1975.- 287 с.
- Холопов Ю. В. Ультразвуковая сварка. Л.: Машиностроение. 1972, — 152 с.
- Чалабаев Х.Ч., Меликов В. В. Широкослойная наплавка. Ташкент: Узбекистан. 1984. 142 с.
- Чалмерс Е. Теория затвердевания. М.: Металлургиздат. 1968.
- Чепеленко В.И. Исследование остаточных напряжений и деформаций деталей автомобилей и других машин, восстановленных автоматической наплавкой под флюсом./ Авт. дис. к. т. н. Саратов: СПИ 1971 26с.
- Чистяков В.В. Методы подобия и размерностей в литейной гидравлике . -М.: Машиностроение. 1990 224 с.
- Шаврин О.И. Технология и оборудование термомеханической обработки деталей машин. М.: Машиностроение. 1983. -176 с.
- Шаповалова Г. С. Состояние поверхностного слоя и эксплуатационные свойства опорных поверхностей валов из износостойких чугунов при обработке с нагревом. Автореф. Дис. к.т.н. М. 1981.-24 с.
- Шатерин М.А., Попилов А. Л., Медко B.C. Эффективность нагрева заготовки при плазменно-механической обработке. / Сварочное производство. 1982, № 5, с. 29−30.
- Шульц В.В. Форма естественного износа деталей машин и инструмента. -Л.: Машиностроение. 1990. 208 с.
- Шутинский С.Х. Электромагнитные приводы исполнительных механизмов. М.: Энергоиздат, 1984.
- Электрошлаковая сварка и наплавка / Под общ. ред. Б. Е. Патона. М.: Машиностроение. 1980. 511 с.
- Эффективность наплавочных работ. /Под общ. ред. Гладкого П. В. Киев. Наук. Думка. 107 с.
- Юзвенко Ю.А. Порошковые проволоки для наплавки // Автоматическая сварка. 1972. N5.-С. 67 -70.
- Ямпольский Ю.Г. О проектировании оптимальных линейных импульсных электродинамических двигателей возвратно-поступательного движения. Электротехника. № 2. 1990 С. 51−55.
- Ярошевич В.К. Прогрессивные способы упрочнения быстроизнашивающихся поверхностей деталей машин: ЭИ. Серия «Металлообработка» -Минск: БелНИИНТИ, 1978. 12 с.
- Bramerts Р.Н. Die Entstehung der Oberlachenrauheit Beim Feindrehen. // Ind. -Aur. -№ 2 .-1961.-P. 25−32.
- Derby В., Wollach E. .R. Theoretical model for diffusion bonding// Metal Science. 1982. V. 16. N 1. P. 49 56.
- Gannong G., Paton N. E. Attainment of full interfacial contact during diffusion bonding// Metallurgical Transactions/ 1975. V. A6. N6. P. 1969−1979
- Mc. Glone I. C., Weld bead geometiyprediction a review / Metal Construction and British Welding Journal. 1982 N 7 P. 378−384.
- Документ, подтверждающий внедрение разработок организацией (предприятием), у которых отсутствует отчетность по форме Р- 10 ЦСУ1. Утверждаю"
- Генеральный директор ЗАО ЭПФ «ТрансМагистраль Саратов"1. Бежкинев С.И.1. АКТо внедрении результатов научно-исследовательской (опытно-конструкторской) работы
- Разработка сотрудников Саратовского государственного технического верситета доцента кафедры МВПО к.т.н. Казакова Ю. Н. и аспиранта нина A.A.
- Именно технология и технологическое оснащение наплавки плоских деталей. Выполненной в соответствии с договором подрядом «разработка и исследование тологии упрочнения ножей отвалов методом совмещенной наплавки с анической обработкой» от 20.01.98.
- Переданные ТОО «Нике» в лице Гомаюнова В. А. являющейся дочерней фирмой Р «Транс-Магистраль» Саратов.
- Внедрены с декабря 1999 года в слесарно-сварочном цехе предприятия ганизации).