Термодиффузионное упрочнение деталей гидроцилиндров из серого чугуна алюминием и ванадием в порошковой среде
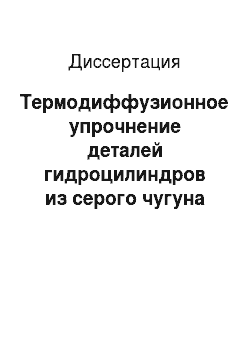
Испытания алюмованадированного покрытия трением в условиях сухого скольжения позволило установить высокую его износостойкость. Образцы из исходного чугуна СЧ 20 оказались не пригодными для этих испытаний, так как их износ при времени испытаний — 2 часа и нагрузке 2 кг/см" составил 0,1 мм, а износ упрочненного слоя при этом близок к нулю, а дальнейшее сравнение вообще не возможно, так как износ… Читать ещё >
Содержание
- 1. Состояние вопроса, постановка цели и задач исследований
- 1. I '
- 1. )
- 1. 1. Спектр применения деталей из серого чугуна
- 1. 2. Анализ способов повышения долговечности деталей из серого чугуна
- 1. 3. Влияние легирующих элементов на формирование износостойкой структуры в белых чугунах
- 1. 4. Постановка цели и задач исследований.'
- 2. Оборудование, материалы и методика проведения экспериментов по созданию алюмованадированных слоев
- 2. 1. Выбор компонентов и агрегатного состояния насыщающих сред для термодиффузионного упрочнения
- 2. 2. Используемые порошковые реактивы
- 2. 3. Установка для проведения термодиффузионного упрочнения
- 2. 4. Алюмованадирование образцов из серого чугуна
- 2. 4. 1. Подготовка образцов и компонентов шихты
- 2. 4. 2. Методика проведения термодиффузионного ванадирования серого чугуна
- 2. 4. 3. Методика алюмованадирования серого чугуна
- 2. 5. Методы исследования алюмованадированных покрытий
- 2. 5. 1. Методика проведения металлографического анализа упрочненных образцов
- 2. 5. 2. Методика проведения микрорентгеноспектрального и количественного фазового анализа упрочненных образцов
- 2. 5. 3. Методика испытаний на коррозионную стойкость
- 3. 1. Результаты ванадирования серого чугуна
- 3. 2. Результаты алюмованадирования серого чугуна
- 3. 3. Кинетика совместного диффузионного насыщения серого чугуна алюминием и ванадием
- 3. 4. Определение температурно-временных зависимостей процесса насыщения
- 4. 1. Карбидные диффузионные слои
- 4. 2. Алюминидные диффузионные слои
- 5. 1. Остаточные напряжения в покрытии
- 5. 2. Исследование износостойкости покрытия в условиях сухого трения скольжения
- 5. 2. 1. Методика проведения испытаний
- 5. 2. 2. Результаты проведенных испытаний
- 5. 3. Исследование износостойкости покрытия в условиях трения со смазкой, содержащей абразивный материал
- 5. 4. Износостойкость алюмованадированого слоя в условиях абразивного истирания
- 5. 5. Результаты испытаний коррозионной стойкости в модельных средах и их обсуждение
Термодиффузионное упрочнение деталей гидроцилиндров из серого чугуна алюминием и ванадием в порошковой среде (реферат, курсовая, диплом, контрольная)
Развитие многих отраслей современной техники, повышение надежности машин и механизмов, увеличение производительности оборудования и труда в значительной мере зависят от разработки и практического использования различных типов защитных покрытий. Нанесение защитных покрытий позволяет увеличить твердость, износои окалиностойкость, улучшить коррозионные свойства, а также придать специфические эксплуатационные характеристики рабочим поверхностям деталей машин, приборов, производственного оборудования, инструмента. Это обеспечивает повышение срока службы и надежность соответствующих деталей и узлов, снижение трудоемкости и металлоемкости производства, дает возможность заменить дорогие и дефицитные материалы более дешевыми и доступными.
Важные научные исследования в области защитных покрытий выполнены в вузах, отраслевых научно-исследовательских институтах и на заводах страны. Большое внимание при этом было уделено вопросам теории диффузионного насыщения, реакционной диффузии, структуре и ' эксплуатационным свойствам диффузионных покрытий (Одесский политехнический институт, Воронежский технологический институт), особенностям плазменного, денотационного и других видов покрытий (УралНИИЧермет, Калининский политехнический институт). Особое внимание уделено многокомпонентному насыщению (Белорусский политехнический институт, Воронежский технологический институт).
Разработке и промышленному применению различных методов и типов защитных покрытий уделяется большое внимание в США, Японии, Англии, Франции.
Программы работ в этой области финансируются правительством и частными компаниями многих отраслей промышленности.
В США свыше 50 крупных научно-исследовательских центров и лабораторий занимаются разработкой и практическим применением высокотемпературных покрытий для тугоплавких металлов и сплавов. Особое внимание при этом уделяется методам термического напыления.
В Великобритании с 1964 года функционирует Комитет по коррозии и защите от нее. По данным комитета, на основе обработки информации из 1650 источников, показано, что потери от коррозии в промышленности оцениваются суммой 1365 млн. фунтов стерлингов в год. Только одно лишь правильное применение известных методов защиты от коррозии без дополнительных исследований в этом направлении может уменьшить потери на 310 млн. фунтов стерлингов.
В США, Великобритании, Японии и др. странах широко используются тонкие покрытия (5−10 мкм) из карбидов и нитридов тугоплавких металлов, осаждаемых из газовой фазы на рабочую поверхность стального и твердосплавного инструмента для обработки металла.
В области диффузионных защитных покрытий уже создана теория диффузии в многокомпонентных сибтемах, позволяющая понимать природу особенностей диффузионных процессов, при наличии взаимодействия и количественно описать эти закономерности.
При анализе диффузионных явлений широко и успешно применяются принципы и методы термодинамики неравновесных процессов и положения теории электронного строения вещества, в том числе в рамках I конфигурационной модели. Успехи теории многокомпонентной диффузии позволяют разработать 1 методы прогнозирования долговечности диффузионных защитных покрытий.
В настоящее время накоплены обширные экспериментальные данные по свойствам материалов с диффузионными защитными покрытиями, в частности по влиянию диффузионных покрытий на кратковременную статическую и усталостную прочность защищенных изделий на воздухе и в различных средах. Изучена роль остаточных напряжений, возникающих в процессе диффузионного насыщения, и предложена их классификация. Работы в этой области имеют важное значение для раскрытия механизма деформации и разрушения металлов с покрытиями, для создания теории прочности таких материалов.
Анализируя выше изложенное, можно сказать, что успешное решение всего комплекса сложных практических задач возможно лишь на основе достаточно обоснованных теоретических предпосылок и поисковых исследований. Поэтому, наряду с совершенствованием существующих типов покрытий и методов их нанесения, а также организации их внедрения в народное хозяйство, необходимо постоянно вести поисковые исследования по синтезу новых типов соединений, 1 перспективных в качестве материалов для покрытий, и разработке новых высокопроизводительных методов их нанесения, основанных на новейших технических возможностях. 1.
Выводы по пятой главе.
1. Произведена оценка остаточных напряжений в покрытии. При содержаниях алюминия в шихте 0,75% они составят (-260±140) МПа, при содержании 2% - (-340±170) МПа, при содержании 2,5%- (380 ±30) МПа. Полученные напряжения являются сжимающими.
2. Испытания алюмованадированного покрытия трением в условиях сухого скольжения позволили установить высокую его износостойкость. Образцы из исходного чугуна СЧ 20 оказались не пригодными для этих испытаний, так как их износ при времени испытаний — 2 часа и нагрузке 2 кг/см" составил 0,1 мм, а износ упрочненного слоя при этом близок к нулю, а дальнейшее сравнение вообще не возможно, так как износ серого чугуна асимптотически стремится вверх.
3. Износостойкость упрочненного чугуна при трении со смазкой, содержащей абразивный материал (окись алюминия) в количестве 5% по.
О О объему при нагрузке 2 кг/см в 4 раз, а при нагрузке 3 кг/см в 8 раз выше износостойкости исходного чугуна СЧ 20. При более сильном нагружении сравнение износостойкостей не возможно, так как кривая, характеризующая линейный износ исходного чугуна приближается к вертикальной асимптоте и не дает сравнительных показателей.
4. В условиях сухого абразивного истирания алюмованадированные слои имеют коэффициент износостойкости в сравнении с отожженной сталью 45- Кн= 5- в сравнении с исходным чугуном — Ки = 24.
5. Коррозионные испытания алюмованадированных покрытий показали высокую стойкость в сравнении с чисто ванадированнными покрытиями на сером чугуне во всех модельных растворах, кроме 1% раствора соляной кислоты, 25% раствора ЫаС1 и морской воды. .
1. Выявлена актуальность создания износостойких и коррозионностойких покрытий на серых чугунах, являющегося экономически I выгодным материалом для всех отраслей машиностроения.
Определены химические элементы, позволяющие создать такое покрытие, а также материалы, содержащие их, используемые в целях снижения дефицитности и дороговизны — это феррованадий ФВо50У0,3 и алюминиевый порошок, марки А5.
2. Разработана и запатентована установка для алюмованадирования деталей типа колец и втулок.
3. Экспериментальными исследованиями определены рациональные содержания феррованадия ФВо50У0,3 в шихте- 60−65% масс, и 1,5−2,5% I масс.- порошка алюминия. Данный состав обеспечивает высокие значения микротвердости 24 000−25 000 МПа на поверхности образцов из серого чугуна с плавным понижением ее вглубь, что говорит о высокой работоспособности слоя.
4. Исследована кинетика совместного диффузионного насыщения серого чугуна алюминием и ванадием. Определено, что при температуре 840 °C коэффициент диффузии ванадия в серый чугун составляет.
1 П 1 1А Л.
7,35 «10″ см7сек, а алюминия — 3,913−10 см/сек, но при рабочей температуре процесса — 1020 °C кинетика меняется и коэффициент диффузии ванадия становится равным 14,8-Ю» 10см/сек, а коэффициент диффузии алюминия- 9,33−10″ 9см2/сек.
Выявлены коэффициенты диффузии компонентов под влиянием потоков друг друга для температурного интервала 840−1020°С. При этом коэффициент диффузии ванадия под влиянием потока алюминия (Т)У, Л1) с повышением температуры увеличивается, а коэффициент диффузии алюминия под влиянием потока ванадия (рд^у) остается примерно одинаковым, но на порядок ниже, чем в случае чистого алитирования.
5. Микроструктура диффузионного слоя определяется управляющими параметрамиконцентрацией алюминия в реакционной среде (содержание феррованадия зафиксировано на уровне 60% масс.), временем насыщения и температурой процесса.
В зависимости от содержания алюминия в реакционной среде можно выделить два типа структур диффузионного покрытиякарбидные, образующиеся при содержании алюминия в реакционной среде до 2−3% и алюминидные — образующиеся при более высоких содержаниях алюминия.
6. Количественный фазовый анализ, проведенный на установке ДРОН-4 с использованием программы идентификации фаз PHAN, показал в карбидных слоях наличие кроме карбидов ванадия V2C и VC еще и следующих фаз: Fe3AlCo, 9 и a-Fe. Причем доля фазы Fe3AlCo, 9 увеличивается с увеличением содержания алюминия, а доля карбидов ванадия снижается.
7. Методом SIN" |/ были оценены остаточные напряжения в покрытии, которые являются по природе сжимающими и по величине составляют 260 380 МПа.
8. Испытания алюмованадированного покрытия трением в условиях сухого скольжения позволило установить высокую его износостойкость. Образцы из исходного чугуна СЧ 20 оказались не пригодными для этих испытаний, так как их износ при времени испытаний — 2 часа и нагрузке 2 кг/см" составил 0,1 мм, а износ упрочненного слоя при этом близок к нулю, а дальнейшее сравнение вообще не возможно, так как износ серого чугуна асимптотически стремится вверх.
9. Износостойкость упрочненного чугуна при трении со смазкой, содержащей абразивный материал (А1203) в количестве 5% по объему при нагрузке 2 кг/см2 в 4 раза, а при нагрузке 3 кг/см2 в 8 раз выше износостойкости исходного чугуна СЧ 20. При более сильном нагружении сравнение износостойкостей не возможно, так как кривая, характеризующая линейный износ исходного чугуна приближается к вертикальной асимптоте и не дает сравнительных показателей.
10. В условиях сухого абразивного истирания алюмованадированные слои имеют коэффициент относительной износостойкости в сравнении с отожженной сталью 45- Ки= 5- в сравнении с исходным чугуном — Ки = 24.
11. Коррозионные испытания алюмованадированных покрытий показали высокую их стойкость во всех модельных растворах коррозионных сред в сравнении с чисто ванадированными покрытиями, кроме 1% раствора соляной кислоты, 25% раствора №С1 и морской воды.
Список литературы
- Шерман А.Д., Жуков A.A., Чугун. Справочник, 1991, 576 с.
- Канторович В.И., Шерман А. Д., Семенов В. М. и др. Отечественный и зарубежный опыт применения чугунов для деталей тракторных дизелей. -М.: Изд-во ЦНИИТЭИТракторсельхозмаш, 1980. 72 с.
- Материалы карбюраторных двигателей/ Справочное пособие под редакцией A.B. Лакедемонского. М.: Машиностроение. 1969. — 223с.
- Филлипов Г. С. Разработка покрытий плазменного напыления для повышения долговечности деталей оборудования пищевой и зерноперерабатывающей промышленности / Диссертация на соискание ученой степени к.т.н.- М., МТИПП, 1983 г.
- Ройтбурд А.Г. Повышение стойкости вальцев вальцевых станков элеваторной промышленности /Диссертация на соискание ученой степени к.т.н.-М., МТИПП., 1982 г.
- Коденеев А.Г. Повышение стойкости молотков молотковых дробилок комбикормовой промышленности /Диссертация на соискание ученой степени к.т.н. М., МТИПП., 1979 г.
- Костецкий Б.И. Износостойкость металлов.- М: Машиностроение, 1980. с.51
- Словарь-справочник по трению, износу и смазке деталей машин / E. JI Шверков, Д. Я. Ровинский, В. Д. Зозуля, Э. Д. Браун. Киев: Наук. Думка, 1979. с. 183.
- Станчев Д.И. Конструкционные материалы для лесных машин.-Воронеж: Издательство Воронежского университета, 1982 г, 172с.
- Костецкий Б.И. Сопротивление изнашиванию деталей машин.- М.: Киев- Машиностроение. 1979, с. 354.
- Веселовский A.A., Завалищин А. Н. Исследование кинетики совместного термодиффузионного насыщения серого чугуна алюминием и ванадием из порошковой смеси контактным способом. //Упрочняющиетехнологии и покрытия. 2008 г. № 8.
- Шерман А.Д., Якушин H.H. Чугуны для гильз цилиндров автомобильных двигателей. Вып.4 Автомобильные двигатели и топливная аппаратура. — М.: Изд-во НИИНАвтопром, 1978, с. 71.
- Гречин В.П. Легированное чугунное литье. М: Оборонгиз, 1952 г.
- Колисниченко А.Г., Оболенский В. К., Демченко В. И. Расчет герметичности чугунных отливок // Литейное производство, 1982 г. № 4.
- Герчиков A.M., Шевчук С. А., Самсонов В. И. Влияние качества чугуна на износостойкость базовых деталей станков // Станки и инструмент. -1979. № 3.
- Войнов Б.А. Износостойкие сплавы и покрытия. М.: Машиностроение, 1980. — 120 с.
- Повышение стойкости лопастей дробеметных машин / О. С. Комаров, Н. И. Урбанович, A.B. Муравский и др. // Литейное производство. — 1988. № 5.- с. 31
- Лещенко А.Д., Кузовов А. Ф., Лунев В. В. Состав хромистого чугуна с заданными свойствами // Литейное производство. 1988. — № 6. с. 8.
- Жуков A.A., Сильман Г. И., Фрольцов М. С. Износостойкие отливки из комплексно-легированных белых чугунов. М.: Машиностроение, 1984 г, 104 с.
- Сильман Г. И. Диаграмма состояния сплавов Fe-C-V и ее использование в металловедении сталей и чугунов //. Металловедение и термическая обработка металлов 1992. № 11. с. 4−7
- Таран Ю.Н., Калинина Л. Т., Иванов Л. И. Структура эвтектик в сплавах Fe-C-V // Известия вузов. Черная металлургия. — 1966. № 6, с. 145 150.
- Крукович М.Г. Разработка теоретических и прикладных аспектов управления структурой и свойствами борированных слоев и их использование при производстве транспортной техники / Диссертация на соискание ученой степени д.т.н. М.: МПС — МИИТ 1995, 416 с.
- Переверзев В.М., Барботако А. И. Силицирование серого чугуна. // Защитные покрытия на металлах, вып.5. Киев, Наукова думка, 1971. с 77−78.
- Крукович М.Г., Микевич А. Н., Тонэ Э. Р. Технологические методы повышения износостойкости и восстановления деталей машин. — М.: Машиностроение, 2002 г., с. 322.
- Лахтин Ю.М., Арзамасов Б. Н. Химико-термическая обработка металлов. М.: Металлургия, 1985 г., с. 256.
- Удовицкий В.И. Технология и практика внедрения силицирования стальных изделий // Металловедение и термическая обработка металлов, 1984, № 5, с 15−16. N
- Сонин В.Н. Газотермическое напыление материалов в машиностроении. -М.: Машиностроение, 1973 г., с. 254.
- Геллер Ю.А., Рахштадт А. Г. Материаловедение. М, Металлургия, 1989, с. 454.
- Похмурский В.И., Далисов В. Б. Повышение долговечности деталей машин с помощью диффузионных покрытий. Киев: Наукова думка, 1980 г.
- Кокора А.Н., Зулаев В. Б., Коряев E.H. Лазерное поверхностное упрочнение деталей оборудования, инструмента // Электрофизические и электрохимические методы обработки материалов 1978 г., № 2 с. 127−135.
- Цыпин И.И. Белые износостойкие чугуны. Структура и свойства. — М.: Металлургия, 1988. 56с.
- Гарбер М.Е. Отливки из белых чугунов.- М.: Машиностроение, 1972.-112с.
- De Melbo J.D.B., Durand- Charre M., Matia M. Abrasionmechanismus of white cast iron.l. Influence of the metallurgical structure ofmolybdenum white cast irons // Mater. Sci and Eng., 1985. p. 203−213.i
- Хорошев A.B. Защитные плиты из износостойкого чугуна //
- Литейное производство.- 1988. № 4. с. 26.
- Щебатинов М.П., Алабин П. А., Сбитнев П. П. ИзносостойкийIбелый чугун для сменных деталей очистного оборудования // Литейное производство. — 1985, № 2. с. 7−8.
- Пути повышения износостойкости стальных отливок / В.М.I
- Колокольцев, Е.Г. Кодзаев, В.И. Кирюшкин // Прогрессивные технологии производства литых заготовок. Челябинск, 1988 г., с. 61−62.
- Колокольцев В.М. Основы синтеза износостойких литейных сталей и чугунов // Литейное производство, 1995 г., с. 5−7.
- Гетьман А.А. Качество и надежность чугунных отливок. — Л.: Машиностроение, 1970. с. 224.
- Удовицкий В.И. Технология и практика внедрения силицирования стальных изделий // Металловедение и термическая обработка металлов, 1984, № 5, с 15−16.
- Лахтин Ю.М. Поверхностное упрочнение стали и сплавов // Металловедение и термическая обработка металлов, 1988, № 11, с 14−25.
- Гегузин Л.Е. Диффузионная зона. — М.: Наука, 1979 г., 72с.
- Пинес Б.Я. К кинетике спекания в твердой фазе. // ФММ, 1960, т. 10 № 5, с 750.
- Дубинин Г. Н. О механизме формирования диффузионного слоя // Защитные покрытия на металлах. Киев: Наукова думка, 1976. вып. 10, с 12.
- Таран Ю.Н., Мазур В. И. Структура эвтектических сплавов. М.: Металлургия, 1978, 311с
- Бунин К.П., Таран Ю. Н. Строение чугуна. М.: Металлургия, 1972 г., — 162с.
- Голубец В.М., Пурич Е. Н., Пашечко М. И. и др. Хрупкость эвтектических покрытий при деформации царапанием. // ФХММ, 1984, № 5,с. 123−124
- Яненский Н.Е., Винницкий А. Г., Колесниченко Л. Ф. Получение покрытий эвтектического типа диффузионной металлизацией в порошках. // Защитные покрытия на металлах: Сборник, Киев: Наукова думка, 1976, вып. 10, с. 78−80.
- Ткачев В.Н., Поляков Б. Н., Сидельникова В. И. Микроструктураи свойства боридных слоев, образующихся при индукционном нагреве стали.
- Металловедение и термическая обработка металлов. 1979, № 1, с. 2−5.
- Назаренко П.В., Папарин В. Е., Микуляк О. В. Износостойкость плазменных покрытий из эвтектических сталей // Трение и износ. 1983, Т.5, № 6, с. 1074−1079.
- Картер В.И. Металлические противокоррозионные покрытия.- Л: Судостроение, 1980 г. с. 168.
- Белый A.B., Карпенко Г. Д., Мышкин Н. К. Структура и методы формирования износостойких поверхностных слоев. М.: Машиностроение, 1997 г. С. 208.
- Потапов М.Г. Разработка нового состава износостойкого чугуна для отливок деталей насосов / Диссертация на соискание ученой степени к.т.н. -М: Магнитогорск, 2002 г.
- Карпитьянц М.Х., Дракин СЛ. Общая и неорганическая химия.// Учебное пособие для вузов. -М.: Химия, 1981.С.632.
- Жуков A.A., Зволинская В. В. Отливки из железоуглеродистых славов, легированных ванадием: Обзор / НИИмаш. М., 1978. с. 48.
- Виноградов В.Н., Сорокин Г. М. Износостойкость сталей и сплавов. — М: Нефть и газ, 1994. с. 417.
- Виноградов В.Н., Сорокин Г. М. Механическое изнашивание сталей и сплавов. -М.: Недра, 1996. с. 364.
- Хрущов М.М., Бабичев М. А. Абразивное изнашивание. М: Наука, 1970. с. 270.
- Титов Н.Д., Степанов Ю. А. Технология литейного производства. -- М Машиностроение, 1985 г.
- Грызунов В.И., Шамова В.А, Кувшинов A.A. Сборник задач по физической химии. -Москва, 1997 г.
- Жуховицкий A.A., Шварцман A.A. Физическая химия.- Москва, 1963 г.
- Лукашкнн Н.Д., Кохан Л. С., Якушев A.M. Конструкция и расчет машин и агрегатов металлургических заводов: учебник для вузов. М.: ИКЦ «Академкнига», 2003 г. с. 456.
- Некрасов В.И. Многофакторный эксперимент. Планирование и обработка результатов.//Учебное пособие. Курган, 1998 г. I
- ГрачевЮ.П.Математические методы планирования экспериментов.-М: Пищевая промышленность, 1979. с. 198.
- Веселовский A.A. Завалищнн А. Н. Исследование микротвердости алюмованадированных слоев на серых чугунах, полученных термодиффузионным упрочнением // Упрочняющие технологии и покрытия № 5 2007 г.-с. 18−21.
- Новое в области испытаний на микротвердость./ Под ред. Хрущова М. М. -М.: Наука, 1974. с. 270.
- Евдокимов Ю.А., Колесников В. И., Тетерин А. И. Планирование и анализ экспериментов при решении задач трения и износа. М.: Наука, 1980, с. 228.
- Исследование условий получения и некоторых свойств карбидохромовых покрытий на железоуглеродистых сплавах. Г. Л. Жуковский, М. И. Олиевский, М. В. Лучка, Т. Е. Гайдукова. // Защитные покрытия на металлах, 1974, вып. 8, с. 102−104.
- Распределение элементов в стали 45, подвергнутойхромоалитированию. В. И. Похмурский, В. Б. Далисов, A.M. Мокрова, ЯЛ. Бродяк. // Защитные покрытия на металлах. 1979 г., вып. 3, с. 130−132.
- Лидин P.A., Молочко В. А., Андреева Л. Л. Задачи по неорганической химии.- Москва., 1990 г.
- MapKiB В.Я., Теслюк М. Ю. Доповщц АН УРСР, серия А, 1962, № 12, с. 16
- Аргеенков В.Г., Михин Я. Я. Металлургические расчеты.// Мталлургиздат, 1962 г.
- Карапетьянц М.Х. Химическая термодинамика.// Металлуриздат, 1949 г.
- Синельникова B.C. и др. Алюминиды.- Киев: Наукова думка, 965 г.
- Хансен М, Анд ер ко К. Структуры двойных сплавов.// Металлургиздат, 1962 г.
- Синельникова B.C. и др. Алюминиды, — Киев: «Наукова думка», 1965 г.
- Термодинамические свойства неорганических веществ.- М., Автомиздат, 1985 г. 460с. Авт. У. Д. Верятин, В. П. Маширев, Н. Г. Рябцев и др.
- Арзамасов Б.Н., Сидорин Н. И. и др.// Материаловедение. Машиностроение, 1976 г.81Скатецкин В.Г., Свиридов Д. В., Яшкин В. И. Математические методы в химии.- Минск. Тетра Системе, 2006 г.
- Новое в области испытаний на микротвердость./Под ред. Хрущова М.М.- М.: Наука, 1974. с. 270.
- Веселовский A.A. Формирование многофункционального покрытия на деталях из серого чугуна совместным термодиффузионным насыщением алюминием и ванадием. // Технология машиностроения 2007 № 1- с.45−47.
- Минкевич А.Н. Химико-термическая обработка металлов и сплавов. Издательство «Машиностроение», 1985 г.
- Шелехов Е.В., Свиридова Т. А. Программы для рентгеновского анализа поликристаллов.//Металловедение и термическая обработка металлов № 8, 2000 г. стр. 16−19.
- Испытания на микротвердость / Под ред. Хрущова М. М. — М.: Наука, 1974 г. с. 270.
- Шаповалов В.П., Горбунов Н.С, Ковальчук Г. Н., Байдак Н. П. Диффузионное титанирование металлов и сплавов./ Тезисы докладов 2-й Всесоюзной научной конференции по химико-термической обработке металлов и сплавов. Минск., 1974 г.
- Похмурский В.И., Толстова C.B., Мокрова A.M. Ванадированиеметаллов и сплавов, строение и свойства диффузионных слоев.// ЗащитныеIпокрытия на металлах. Киев. Наукова Думка. 1974 г. с. 106−108.
- Дубинин Г. Н., Карпман М. Г., Альтшуллер Д. Ф. Защитные покрытия на металлах.- Киев. Наукова думка. № 5 1973 г. с. 14−16.
- Ума некий Я.С., Скаков Ю. А., Иванов А. Н. Кристаллография, рентгенография и электронная микроскопия- Металлургия, 1982 г.
- Горелик С. С, Скаков Ю. А., Расторгуев JI.H. Рентгенографический и электронно-оптический анализ «МИСиС», 2002 г.
- Полясков Ю.В., Табаков В. П., Тамаров А. П. Технологические методы повышения износостойкости режущего инструмента и деталей машин// Учебное пособие. Ульяновск: УлГУ.1999 г. 69 с.
- Самсонов Г. В., Эпик А. П. Покрытия из тугоплавких соединений.-Металлургия. М. 1964.
- Лахтин Ю. М. Пчелкина М.А.- В кн. Металловедение и термическая обработка металлов. Машиностроение- М., 1964 г.
- Эванс Ю.Р. Коррозия и окисление металлов.- Машгиз, 1962.
- Можаров М.В. и др.- Изв. Вузов. Черная металлургия, 1974 г. 1
- Глухов В.П. Боридные покрытия на железе и сталях.- Киев: «Наукова думка», 1970 г.
- Завалищин А.Н. Исследование возможности улучшения качества боридного слоя и подслоя на высокопрочных чугунах с шаровидным графитом./ Автореферат дисс. на соиск. уч. степени канд. техн. наук -Киев. 1976 г. i
- Земсков Г. В., Коган P.JI. Шевченко И.М.- Защитные покрытия на металлах. Киев: «Наукова думка», 1971, № 4.
- Земсков Г. В., Коган PJL, Мороз В.И. Многокомпонентноеiдиффузионное насыщение из суспензий. Защитные покрытия на металлах.-Киев 1971 г.
- Самсонов Г. В., Винницкий И. М. Тугоплавкие соединения. Справочник. М: Металлургия, 1976 г. i
- Веселовский A.A., Завалищин А. Н. Упрочнение поверхностей трения направляющих телескопических гидроцилиндров термодиффузионным алюмованадированием // Трение и смазка в машинах и механизмах 2008 г. № 2 с. 14−16.
- Веселовский A.A., Завалищин А. Н. Новая установка для термодиффузионного упрочнения изделий типа колец //У прочняющиетехнологии и покрытия. 2008 г. № 6. с.37−38.
- Веселовский A.A., Завалищин А. Н. Исследование кинетики совместного термодиффузионного насыщения серого чугуна алюминием и ванадием из порошковой смеси контактным способом // Упрочняющие технологии и покрытия, 2008 г. № 8.
- Результаты количественного фазового анализа образца 0,75% (№ 1) алюминия в шихте, от поверхности.
- Маркировка: № 0,75, исходный, СоК"-изл., ДРОН-4, 05.09.07, Ъ2
- Отобранная фаза Код Пирсона, А бс., ИНТ. Номер
- V С (type Bl) СГ8/2 50,, 473 100
- V2 С -beta (L'3, T>800~C) ЬР4 / 6 72. .704 1315
- Al2 03 ЬИ10/1 9,. 455 3249
- Fe3 V3 С (type E9.3) сГ112/2 26.. 563 69 505 a-Fe (type A2) С12/1 24.. 177 12 468
- Полуширина окна допуска AD = C*DAN, В = а/п (анг.), С = 0.003, N = 2I
- Эксперимент (излучение СоКа) Данные из банкафаз
- Fe3 V3 C (type E9. 3) 1 .282 2325 90. 70 1 .258 0 .7 V C (type B1) 1 .257 32
- V2 C -beta (L'3, T>800~C) 1 .257 2
- Fe3 V3 C (type E9. 3) 1 .256 726 92. 40 1 .240 0 .5 Al2 03 1 .239 1427 96. 00 1 .204 0 .6 V C (type B1) 1 .204 1828 96. 50 1 .200 0 .5 V C (type B1) 1 .204 1829 97. 60 1 .190 0 .1 Al 2 03 1. 192 0.51. 189 5
- V2 C -beta (L'3, T>800~C) 1 .041 21. Al2 03 1 .042 1637 123. 20 1 .018 0 .2 Al2 03 1 .017 2a-Fe (type A2) 1 .018 9
- Результаты качественного фазового анализа образца с содержаниемI2% (№ 2) алюминия в шихте, от поверхности Маркировка: № 2, исходный, СоКа-изл., ДРОН-4, 06.09.07, Ь21. Отобранная фаза1. Код Пирсона1. Абс.инт. Номер1 2