Повышение качества деталей при деформирующем протягивании на основе применения металлоплакирующих смазок
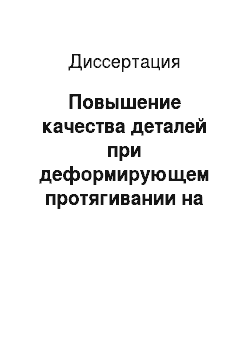
На основании теоретической части данной работы и анализа ранее выполненных работ, а также с учетом научно-технической литературы разработана методика проведения исследовательских работ по определению влияния управляющих параметров (натяга, толщины стенки, твердости материала, исходной шероховатости, вида смазки и других факторов) на осевое усилие протягивания, исправление погрешностей форм… Читать ещё >
Содержание
- ОСНОВНЫЕ ПРИНЯТЫЕ ОБОЗНАЧЕНИЯ
- ГЛАВА 1. СОСТОЯНИЕ ВОПРОСА, ЦЕЛЬ И ЗАДАЧИ ИССЛЕДОВАНИЯ
- 1. 1. Анализ работ и опыта промышленности по обработке отверстий деталей машин методом деформирующего протягивания
- 1. 2. Точность обработки и качество поверхностного слоя отверстий деталей машин обработанных методом деформирующего протягивания
- 1. 2. 1. Точность формы и размера отверстия
- 1. 2. 2. Шероховатость поверхности отверстия и износ
- 1. 2. 3. Упрочнение поверхностного слоя, микроструктура и износ
- 1. 2. 4,Остаточные напряжения и деформащЕи., ,
- 1. 3. Анализ изнашивания и избирательного пёрёноса при деформирующем протягивании
- 1. 3. 1. Анализ изнашивания и избирательного переноса при трении
- 1. 3. 2. Деформирующее протягивание в условиях граничного трения
- 1. 1. 3.3. Деформирующее протягивание в условиях избирательного переноса
- 1. АТриботехнические свойства металлоплакирующих смазок на основе ЦИАТИМ-201, легированных медными композитами
- 1. 5. Выводы, цели и задачи исследования
- 2. 1. Физическая модель деформирующего протягивания в условиях применения металлоплакирующих смазок
- 2. 1. 1. Взаимодействие поверхности трения и металлоплакирую-щей смазки
- 2. 1. 2. Контактные явления
- 2. 2. Выбор и обоснование основных управляющих параметров процесса
- 2. 3. Площадь контакта
- 2. 4. Поля напряжений
- 2. 5. Остаточные деформации
- 2. 6. Выводы
- 3. 1. Объект исследования
- 3. 2. Инструмент, применяемый в эксперименте
- 3. 3. Оборудование и приспособления для проведения эксперимента
- 3. 4. Приборы и средства измерения
- 3. 5. Смазки применяемые для эксперимента
- 3. 6. Методика проведения экспериментов
- 3. 6. 1. Общий порядок проведения экспериментов
- 3. 6. 2. Методика проведения исследования сил притягивания
- 3. 6. 3. Методика проведения исследования шероховатости поверхности обработанного отверстия
- 3. 6. 4. Методка проведения исследования точности формы и размера обработанного отверстия
- 3. 6. 5. Методика проведения исследования физико-механических свойств поверхностного упрочненного слоя обработанного отверстия
- 3. 7. Методика проведения исследований износостойкости обработанной поверхности отверстия детали
- 3. 7. 1. Метод испытания и оборудование
- 3. 7. 2. Объект исследования
- 3. 7. 3. Режимы испытания
- 3. 7. 4. Измерение величины износа
- 3. 7. 5. Длительность испытаний
- 3. 7. 6. Порядок проведения испытаний
- 3. 8. 0. бработка результатов экспериментов
- 3. 9. Выводы
- 4. 1. Исследование влияния основных управляющих параметров и смазки на усилие протягивания
- 4. 2. Погрешности геометрии отверстия детали
- 4. 2. 1. Исправление погрешности формы поперечных сечений детали после предварительной обработки
- 4. 2. 2. Остаточные деформации и погрешности отверстий после деформирующего протягивания
- 4. 3. Исследование влияния основных управляющих параметров и смазки на шероховатость поверхности отверстия детали
- 4. 4. Исследование влияния основных управляющих параметров и смазки на формирование физико-механических свойств поверхностного слоя отверстия детали
- 4. 5. Исследование влияния применяемой технологической смазки на износостойкость поверхности, обработанной методом деформирующего протягивания
- 4. 6. Выводы
- 5. 1. Рекомендации по применению метода деформирующего протягивания в среде металлоплакирующих смазок
- 5. 2. Перспективы развития метода
- 5. 3. Технико-экономическая оценка метода
Повышение качества деталей при деформирующем протягивании на основе применения металлоплакирующих смазок (реферат, курсовая, диплом, контрольная)
В современном машиностроении одной из главных задач повышения долговечности, работоспособности и надежности машин является повышение износостойкости деталей машин через улучшение качества трущихся поверхностей.
Исследования и практика эксплуатации машин показывают, что наибольшим воздействием в процессе эксплуатации подвергаются поверхностные слои металла, которые противостоят изнашиванию, коррозии, тепловому воздействию и т. д. Поэтому повышение точности формы, размера и качества поверхностного слоя деталей машин различными технологическими методами, предусматривающими значительное увеличение прочности и износостойкости рабочей поверхности деталей" становится одной из главных задач и направлений исследований.
Одним из таких методов является метод деформирующего протягивания, обеспечивающий путем холодного пластического деформирования металла не только упрочнение поверхностного слоя, но и значительное повышение точности обработки, и снижение параметров шероховатости поверхности.
В ряде случаев точность и прочность деталей могут быть увеличены в 2—10 раз, а износостойкость в 1,5−5 раз. При этом значительно возрастает производительность труда, достигается экономия металла, упрощается процесс обработки, создаются условия для его механизации и автоматизации.
Существенный вклад в разработку теоретических основ, совершенствование технологических процессов, оснастки, инструмента внесли исследования, выполненные Ю. Г. Проскуряковым, В. П. Монченко, А. М. Розенбергом и О. А. Розенбергом, А. М. Кузнецовым и В. А. Кузнецовым, А. З. Мариным, И. В. Симоновым, А. А. Крючковым, Т. И. Ковбас, А. С. Лобановым, В. Н. Черкесовым и другими авторами.
Однако, хотя этот метод и все предыдущие исследования и дали возможность промышленности, изменив технологии, повысить износостойкость и качество поверхности деталей, он все-таки полностью не решил всех проблем и еще не использованы все резервы повышения качества и износостойкости деталей.
Это обусловливается тем, что при обработке отверстий в заготовках, особенно из вязких и труднообрабатываемых металлов и сплавов, возникающие в зоне контакта инструмента с обрабатываемой поверхностью большие удельные давления и сдвиговые деформации приводят к схватыванию металлов, резкому увеличению усилия протягивания, ускоренному наростообразованию и снижению стойкости инструмента, образованию и развитию в поверхностных слоях металла трещин, надрывов и других дефектов, которые вызывают резкое ухудшение качества, точности и износостойкости поверхности трения деталей.
Установлено, что одна из основных причин возникновения подобных отрицательных явлений, которые проявляются в наибольшей степени при деформирующем протягивании, заключается в несовершенстве применяемых технологических смазок.
Проблема может быть решена путем применения нейтрально-адгезионных прослоек в виде специально подобранных металлоплакирующих смазок между деформирующим инструментом и поверхностью обрабатываемой детали. В результате применения таких смазок и оптимально подобранных режимов деформирующего протягивания возникает эффект «избирательного переноса». Кроме того, решая технологические проблемы повышения качества поверхности при обработке мы закладываем и дополнительное эксплуатационное снижение износостойкости (кроме того что получаем от деформирующего протягивания) за счет образования на обработанной поверхности полимерной металлоплакирующей пленки.
Исследованиями в области механизма избирательного переноса занимались такие авторы как И. В. Крагельский, Д. Н. Гаркунов, Н. М. Михин В.Н.Литвинов, В. Н. Черкесов и другие. Они показали также, что при наличии такой пленки время приработки и величина износа в эксплуатации снижаются.
Целесообразность и возможность его использования при деформирующем протягивании отверстий деталей машин до настоящего времени полностью не изучена. Этим объясняется отсутствие научных и практических данных и рекомендаций по этому методу.
Поэтому в основу настоящей работы положено экспериментально-теоретическое исследование процесса деформирующего протягивания отверстий в условиях применения металлоплакирующих смазок (М.П.С.).
Работа выполнена на кафедре «Автоматизированные станочные системы и инструменты» Московского Государственного Технического Университета (МАМИ). Экспериментальная часть работы проводилась в лабораториях института, а также на ряде предприятий.
Основные применяемые обозначения do — исходный диаметр отверстия заготовкиdi — диаметр отверстия после деформирующего протягивания;
Ad — остаточная деформация отверстия;
Dh — наружный диаметр заготовки перед обработкой;
Di — наружный диаметр заготовки после обработки;
AD — остаточная деформация по наружному диаметруto — исходная толщина стенки заготовки;
L — длина обрабатываемой заготовкиm=D/d — относительная толщина стенки;
Rao, Rzoисходная шероховатость поверхности отверстия;
Rai, tpi — параметры шероховатости поверхности обработанного отверстия;
Л овотклонение профиля овальности отверстия после обработки;
Ап.с — отклонение профиля продольного сечения отверстия после обработкиот — предел текучести материала заготовки;
НВ — твердость материала по Бринелю;
HV — твердость материала по Виккерсу;
Hjj. — микротвердостьh|a — глубина упрочненного слоя;
Е — модуль упругостиав — предел прочности ат — предел текучестит — касательное напряжение;
Gr, Gt, az — главные нормальные радиальное, тангенциальное, и осевое напряженияsr, st,?z — главные относительные радиальная, тангенциальная, и осевая деформацииqk — контактное давлениеп — количество деформирующих элементова — натяг деформирующего протягивания;
— суммарный натягап — натяг на деформирующий элементd — диаметр деформирующего элемента по ленточкеа — угол рабочего конуса деформирующего элементаho — толщина медной пленкиV — скорость деформирующего протягиванияQ — усилие протягиванияF — сила тренияf — коэффициент тренияS — площадь контактаjj, — коэффициент Пуассона;
Общие выводы.
1. В данной работе представлен анализ научно технической литературы, посвященной вопросам формирования качества обработанной поверхности при деформирующем протягивании. Показано, что несмотря на имеющиеся работы по разработке метода деформирующего протягивания, имеющихся результатов исследования явно не, достаточно для раскрытия закономерностей формирования параметров качества обрабатываемой поверхности. На основании анализа показано, что процесс деформирующего протягивания в среде металлоплакирующей смазки раскрыт недостаточно и требует дополнительных исследований. Вообще, не раскрыто формирование физикомеханических свойств поверхностного слоя, влияние метода обработки деформирующего протягивания в среде М.П.С. на изнашивание поверхности в эксплуатации.
2. В теоретической части данной работы показано, что деформирующее протягивание в среде М.П.С. является согласующимся процессом и инициирующим механизм избирательного переноса для повышения качества поверхности деталей.
Кроме того, на основании теоретических исследований, разработаны:
— физическая модель взаимодействия поверхности трения (инструментдеталь) в среде металлоплакирующей смазки, классифицированы контактные явления;
— разработана структурная схема формирования качества поверхности детали при деформирующем протягивании в среде М.П. С. На основании данной схемы предложен выбор и обоснование основных управляющих параметров процесса. При этом теоретически обосновано их влияние на формирование процесса избирательного переноса;
— разработаны аналитические модели площади контакта, формирования полей напряжений, интенсивности напряжений, остаточных напряжений и деформаций, установлены параметры, влияющие на поля напряженней определены теоретические предпосылки формирования качества поверхностного слоя детали.
3. На основании теоретической части данной работы и анализа ранее выполненных работ, а также с учетом научно-технической литературы разработана методика проведения исследовательских работ по определению влияния управляющих параметров (натяга, толщины стенки, твердости материала, исходной шероховатости, вида смазки и других факторов) на осевое усилие протягивания, исправление погрешностей форм отверстия, шероховатость поверхности и формирование физико — механических свойств в поверхностном слое. Подобраны режимы обработки, оборудование, приборы, объекты исследования и инструмент, разработаны и изготовлены специальные приспособления.
4.Проведенные экспериментальные исследования подтвердили теоретические выводы о закономерностях изменения осевого усилия, формирования показателей качества поверхности при обработке, о влиянии коэффициента трения на остаточные радиальные деформации и о положительном влиянии М.П.С. на повышение эксплуатационных характеристик деталей. Показано, что применение М.П.С. обеспечивает снижение осевого усилия деформирующего протягивания в среднем на 1015%, что в масштабе серийного производства должно привести к экономии электроэнергии. Экспериментально подтверждены теоретические выводы в том, что деформирующее протягивание является процессом, инициирующем механизм избирательного переноса. На поверхности почти всех обработанных образцов при натягах а=0,2 — 0,8 мм было визуально обнаружено наличие медной пленки.
5. Экспериментальными исследованиями установлено, что для повышения эффективности использования М.П.С. исходная шероховатость не должна превышать для Као=2,5 — 4 мкм. Исходя из этих условий должны подбираться соответствующие виды обработки с поперечным расположением рисок микрорельефы.
6. На основании анализа результатов исследований по выявлению влияния управляющих параметров на шероховатость поверхностей установлено, что при деформирующем протягивании в среде М.П.С. шероховатость поверхности ниже на 5 — 10% по сравнения с применением сульфофрезола почти во всем диапазоне проводимых исследований. Подтверждено наличие оптимального натяга на деформирующий элемент, при котором возможно получение наименьшей шероховатости обработанной поверхности. Установлено также, что при многоэлементной обработке наименьшая шероховатость поверхности достигается при таком распределении натягов, когда натяг на каждый из элементов уменьшается от предыдущего к последующему.
7. В результате анализа установлено, что исправление погрешности формы отверстия в поперечном сечении происходит за счет поверхностных и объемных деформаций. Объемные деформации поверхностного слоя для деталей Он/(1о<2 начинают уже происходить в диапазонах натягов, а = 0,2 — 0,4 мм. Для каждого вида материалов Он/(!о имеются оптимальные натяги, обеспечивающие наибольшую точность отверстия.
8. Исправление погрешностей формы от количества циклов обработки при БнЛ1о<2 и при обработке с сульфофрезолом идет до третьего прохода и? а-0,5 мм, а при М.П.С. до шестого прохода Е а=0,7 мм. Это происходит от того, что М.П.С., воспринимая на себя часть касательных напряжений, замедляет нарастание объемных деформаций.
9. Остаточные радиальные деформации (усадка) отверстия при деформирующем протягивании в среде М.П.С. в среднем на 3−5% ниже по сравнению с сульфофрезолом во всем диапазоне проводимых исследований, что подтверждает теоретические выводы о влиянии коэффициента трения на остаточнве радиальные деформации .
10. По результатам анализа экспериментов, исследующих формирование физико-механических свойств поверхности от управляющих параметров, установлено, что с увеличением натяга степень упрочнения и глубина упрочненного слоя возрастают, при этом при обработке в среде М.П.С. менее интенсивно и в зависимости от натяга от 3 до 10%. Установлено, что чем пластичнее материал, тем выше степень упрочнения и глубина упрочненного слоя. С увеличением толщины стенки увеличивается степень упрочнения и глубина упрочненного слоя в среднем на 10% (в зависимости от толщины стенки). Установлено также, что наибольшее влияние на степень упрочнения оказывает твердость обрабатываемого материала, а на глубину упрочненного слоя в наибольшей степени влияет натяг пластического деформирования и в меньшей степени толщина стенки.
При обработке в среде М.П.С. степень упрочнения и глубина упрочненного слоя на 8 — 10% ниже, чем при обработке в среде сульфофрезола почти во всем диапазоне проводимых исследований. Это происходит из-за меньшего коэффициента трения и больших экранирующих свойствах у М.П.С.
11. Применяя методику планирования многофакторного эксперимента получены эмпирические зависимости величин осевого усилия — О, шероховатости поверхностиЯа, степени упрочнения поверхности — 5ну, глубины упрочненного слоя — И от основных управляющих параметров.
12. На основании проведенных сравнительных испытаний изнашивания поверхности образцов можно сделать вывод, что обработка с применением М.П.С. позволяет по сравнению с обработкой в среде сульфофрезола снизить величину приработки в 1,5 раза, а время приработки в 1,3 раза, что существенно скажется на эксплуатационные характеристики деталей, особенно при условии наличия в смазочной среде соответствующих присадок, вызывающих эффект избирательного переноса.
13. Составлены рекомендации по разработке и внедрению метода деформирующего протягивания в среде М.П.С. в условиях серийного производства.
Список литературы
- Алехин В.П. Физика прочности и пластичности поверхностных слоев металла, М., Наука, 1983 г, 124с.
- Адлер Ю.П., Маркова Е. В., Грановский Ю. В. Планирование эксперимента при поиске оптимальных условий М., Наука, 1976 г, 279с.
- Амбросимов С.К. Интенсификация деформирующе-режущего протягивания отверстий на основе упругопластического нагружения зоны обработки. Дисс. к.т.н. М., 1985 г, 177с.
- Аркулис Г. Э. Дорогобид В.Г. Теория пластичности М., Металлургия, 1987 г, 351с.
- Ахматов A.C. Молекулярная физика граничного трения. М., Физматгиз, 1963 г, 472с.
- Беляев Н.М. Вычисление наибольших расчетных напряжений при сжатии соприкасающихся тел, с. 233−260. Сборник Трение и теории упругости ипластичности. М., Гостехтеориздат, 1957 г.
- Боуден Ф.Б., Тейбор Д. Трение и смазка твердых тел. Пер. с англ. М., Машиностроение, 1968 г, 543с.
- Браун Э.Д., Евдокимов Ю. А., Чичинадзе A.B. Моделирование трения и изнашивания в машинах. М., Машиностроение, 1982 г, 191с.
- Бернштейн М.А. Структура деформированных металлов. М., Металлургия, 1977 г.
- Бэкофен В. Процессы деформации. Пер. с англ. М., Металлургия, 1911 т, 288с.
- Баринов В.В. Влияние технологических факторов на уровень погрешности поверхностного слоя деталей при обработке. Дисс. к.т.н. 1984 г, 173с.
- Буйлов Е.А. Повышение износостойкости деталей машин. //Материал международного сборника научных трудов.-МГИУ, М., 1998 г. с.141−143.
- Валяев Ф.Ф. Исследование процесса дорнования с большими натягами цилиндрических отверстий тонкостенных втулок и гильз. Дисс. к.т.н. Ростов на Дону, 1977 г.
- Вейлер С .Я., Лихтман В. И. Действие смазок при обработке металлов давлением. М., Изд-во, АНСССР, 1960 г, 231с.
- Глаголев Н.И., Томило Э. А. Трение качения, тяга, напряженное состояние и износ пар качения. М., НПЦ «Финпол» 1996 г., 188с.
- Гаркунов Д.Н., Мельниченко И. М., Подалов А. Н. О влиянии альдегидов на установление режима избирательного переноса. М., Машиностроение, 1969 г, 88с.
- Гаркунов Д.Н., Поляков A.A. и др. Избирательный перенос в тяжелонагруженных узлах трения. М., Машиностроение, 1982 г, 207с.
- Гаркунов Д.Н., Поляков A.A. Повышение износостойкости деталей конструкции самолетов. М., Машиностроение, 1974 г, 200с.
- Гаркунов Д.Н., Крачельский И. В., Поляков A.A. Избирательный перенос в узлах трения. М., Транспорт, 1969 г, 1
- Гаркунов Д.Н. Повышение износостойкости на основе избирательного переноса. М., Машиностроение, 1977 г, 215с.
- Губкин С.И., Звороно Б. П., Катков В. Ф. Основы теории обработки металлов давлением. М., Машгиз, 1959 г, 539с.
- Гуляев А.П. Металловедение. М., Металлургия, 1977 г.
- Гесим, Винер. Влияние предельного напряжения сдвига на толщину УГД пленки. Проблемы трения и смазки. Труды американского общества инженеров механиков. М., Мир, 1980 г, № 2 с. 88−89.
- Дальский A.M. Технологическое обеспечение надежности высокоточных деталей машин. М., Машиностроение, 1975 г.
- Демкин Н.Б. и др. Оценка шероховатости и волнистости при расчете контактного взаимодействия деталей машин. Вестник машиностроения, 1975 г, № 8, с. 27−29.
- Демкин Н.Б., Рыжов Э. В. Качество поверхности и контакт деталей машин. М., Машиностроение, 1981 г, 244с.
- Джунусбеков Ж.К. Повышение эффективности деформирующе режущего протягивания на основе совершенствования деформирующих элементов. Дисс. к.т.н. М., МАМИ, 1980 г, 247с.
- Дунин-Барковский Н.В., Карташова А. Н. Измерения и анализ шероховатости, волнистости и некруглости. М., Машгиз, 1978 г.
- Дьяченко П.Е. и др. Площадь фактического контакта сопряженных поверхностей. Изд.-во АН СССР, 1963 г.
- Зайцев Д.Е., Дель В. Д., Дель Г. Д. Напряженное состояние при деформирующем протягивании. «Вестник машиностроения.» 1973 г, № 6 с.63−65.
- Зайцев Д.Е. Исследования напряжений при деформирующем протягивании. Дисс. к.т.н., Воронеж, 1971 г, 204с.
- Зельдович Я.Б., Мышкис А. Д. Элементы прикладной математики. М., Наука, 1972 г.
- Зимон А.Д. Адгезия пленок и покрытий. М., Химия, 1977 г, 352с.
- Избирательный перенос при трении. Под ред. Д. Н. Гаркунова. М., Наука, 1975 г, 88с.
- Ильин В.Н. Разработка и исследование нового метода деформирующе-режущего протягивания отверстий. Дисс. к.т.н., М., МАМИ, 1981 г, 179с.
- Ильюшин A.A. Пластичность. ОГИЗ, М., — JI., 1948 г.
- Ильюшин A.A., Огибалов П. М. Действие высокого давления упрочняющего полый цилиндр . Изв., АН СССР, ОТН, 1959 г. № 6.
- Кангун В.Р. Определение высоты неровностей после дорнования. Вестник машиностроения, 1977 т, с.66−68.
- Канета М., Камерон Н. Роль микронеровностей в условиях гидродинамической смазки. Проблемы трения и смазки. Труды Американского общества инженеров механиков. М., Мир, 1980 г, № 3 с.120−126.
- Ковбас Т.Н. Влияние технологических факторов на основные параметры деформирующе-режущего прошивания отверстий в тонкостенных втулках. Дисс. к.т.н., М., МАМИ, 1980 г, 170с.
- Качанов JI.M. Основы теории пластичности. М., Наука, 1969 г, 420с.
- Кащеев В.Н. Процессы в зоне фрикционного контакта металлов М., Машиностроение, 1978 г.
- Клепцов A.A. Разработка методики оптимальных технологических процессов обработки при обеспечении заданных параметров качества поверхностного слоя. Дисс. к.т.н., М., 1979 г.
- Крючков A.A. Разработка и исследование метода обработки шлицевых отверстий деформирующе режущими протяжками. Дисс. к.т.н., М., МАМИ, 1974 г.
- Кузнецов А.М. Технологические основы создания методов обработки в машиностроении. Дисс. доктор технических наук, М., МАМИ, 1975 г.
- КузнецовА.М., Буйлов Е. А. Точность обработки отверстия деталей в условиях применения металлоплакирующих смазок. //Автомобильная промышленность, № 5,1999 г., с. 26−28.
- Кузнецов В.А. Исследование качества поверхностного слоя при деформирующе режущем протягивании. Дисс. к.т.н., М., МАМИ, 1985 г, 211с.
- Кроха В.А. Упрочнение металлов при холодной пластической деформации. Справочник, М., Машиностроение, 1980 г, 156с.
- Крагельский И.В., Добычин Н. М., Комбалов B.C. Основы расчетов на трение и износ. М., Машиностроение, 1911 т, 525с.
- Крагельский И.В., Михин Н. М. О влиянии природы твердых тел на внешнее трение и о соотношении между адгезионной и объемной составляющими. ст. Теория трения и износа. Изд.-во «Наука», 1965 г.
- Крагельский И.В., Михин Н. М. Узлы трения машин. Справочник. М., Машиностроение, 1984 г, 200с.
- Крагельский И.В., Алисина В. В. Трение, изнашивание и смазка. Справочник в 2-х кн. М., Машиностроение, 1978 г, 800с.
- Кужаров A.C., Фисенко О. В. Влияние медьсодержащих добавок на триботехнические свойства пластичной смазки ЦИАТИМ-201. Трение и износ. М., Т. 13, № 2,1992 г, с.317−322.
- Кудрявцев И.В. Поверхностный наклеп для повышения прочности и долговечности деталей машин. М., НТО Машпром, 1969 г.
- Курлов О.Н., Поляков A.A. Исследование механизма избирательного переноса с учетом кинематики и геометрии трущихся пар. В кн.: Применение избирательного переноса в узлах трения машин. М., ВИСМ, т.1,1976 г, с.50−62.
- Литвинов В.Н., Михин Н. М., Мышкин Н. К. Физко-химическая механика избирательного переноса при трении. М., Наука, 1979 г, 187с.
- Лихтман В.И., Ребиндер П. А., Карпенко Г. В. Влияние поверхностно-активной среды на процессы деформации металлов. М., Изд.-во АН СССР. 1954 г, 208с.
- Лобанов A.C. Повышение эффективности деформирующе-режущего протягивания на основе совершенствования характеристик поверхностного слоя деформирующих элементов. Дисс. на соискание ученой степени к.т.н. М., МАМИ, 1989 г, 198с.
- Лобанов A.C., Буйлов Е. А. Физические явления при деформирующем протягивании в условиях применения металлоплакирующей смазки. //Автомобильная промышленность, № 9,1998 г., с. 25−27.
- Лихтман В.И., Щукин Е. Д., Ребиндер Л. А. Физико-химическая механика металлов. М., Изд.-во АН СССР, 1962 г, 303с.
- Луковникова В.Н., Азаревич Г. М. Особенности расчета экономической эффективности при внедрении упрочняюще-калибрующей обработки ППД. М., Тракторы и сельхозмашины, 1962 г, № 1, 16−25с.
- Матвеевский P.M. Температурная стойкость граничных смазочных слоев и твердых смазочных покрытий при трении металлов и сплавов. М., Наука, 1971 г, 227с.
- Малинин Н.И. Прикладная теория пластичности иползучести. М., Машиностроение, 1968 г.
- Марин А.Э. Исследование процесса одновременного пластического деформирования и резания при протягивании (прошивании) отверстий деталей из вязких материалов. Дисс. на соискание ученой степени к.т.н., М., МАМИ, 1969 г, 208с.
- Мельниченко И.И. и др. О роли смазочной среды в осуществлении безызносного режима трения. В кн.: Среда и трение в механизмах. Таганрог: ТПИ, 1974 г, вып. № 4 с. 17−19.
- Митропольский A.K. Техника статистических вычислений. М., Физматгиз, 1961 г, 479с.
- Мещеряков Р.К. Точность обработки тонкостенных цилиндров методом калибрования. Вестник машиностроения. 1973 г, № 4, стр.25−27.
- Михин Н.М. Трение в условиях пластического контакта. М., Наука, 1968 г, 103с.
- Михин Н.М. Внешнее трение твердых тел. М., Наука, 1977 г, 211 с.
- Монченко В.П. Эффективная технология производства полых цилиндров. М., Машиностроение, 1980 г, 247с.
- Надан А. Пластичность и разрушение твердых тел. Т.1, пер. с англ., М., изд.-во ин. лит., 1954 г, 648с.
- Надан А. Пластичность и разрушение твердых тел. Т.2, пер. с англ., М., изд.-во «Мир», 1969 г, 864с.
- Обеспечение износостойкости изделий. Метод оценки служебных свойств смазочных масел и присадок к ним с использованием роликовых испытательных установок. Методические указания. М., 1980 г, 60с.
- Остроумов В.П. Процесс образования микронеровностей при обработке легированной стали методом протягивания. В кн.: Вопросы точности металлорежущих станков и механической обработки. М., Машгиз, 1959 г.
- Пашпев Д.Д. Отделочно-упрочняющая обработка поверхностным пластическим деформированием. М., Машиностроение, 1978 г, 278с.
- Перлин И.А., Шарико В .Я. Механизм и закономерности контактного трения при обработке металлов давлением. ОНТИ, 1965 г, 59с.
- Попов Е.А. Основы теории листовой штамповки. М., Машиностроение, 1971 г.
- Прокопенко А.К., Гаркунов Д. Н. и др. Метод проведения триботехнических испытаний конструкционных и смазочных материалов в режиме избирательного переноса. Методические указания. М., 1984 г, 40с.
- Прокопенко А.К., Порохов B.C. Устройство для непрерывной регистрации износа образцов на машине трения. Заводская лаборатория 1977 г, № 9, с.1152−1153.
- Прокопенко А.К., Симаков Ю. С. Установка для испытания материалов на трение и износ в различных средах. Заводская лаборатория. 1979 г, № 2, с.169−170.
- Посвятенко Э.К. Исследование обрабатываемости металлов, упрочненных черновым деформирующим протягиванием. Дисс. на соискание ученой степени к.т.н., Киев, 1973 г, 210с.
- Проскуряков Ю.Г. Технология упрочняюще-колибрующей и формообразующей обработки металлов. М., Машиностроение, 1971 г, 208с.
- Проскуряков Ю.Г., Шелвинский Г. И. Дорнование цилиндрических отверстий с большими натягами. Ростов на Дону, изд.-во Ростовского государственного университета, 1982 г, 166с.
- Проскуряков Ю.Г., Романов В. И., Исаев А. Н. Объемное дорнование отверстий, М., Машиностроение, 1984 г, 222с.
- Расчетно-экспериментальные методы оценки трения и износа. Отв. ред. И. В. Крачельский. М., Наука, 1980 г, 108с.
- Ребиндер П.А., Щукин Е. Д. Поверхностные явления в твердых телах в процессах их деформации и разрушения. Успехи физических наук, 1972 г, т.108, вып.1, с.3−42.
- Розенберг A.M., Розенберг O.A., Гриценко Э. И., Посвятенко Э. К. Качество поверхности, обработанной деформирующим протягиванием. 1977 г, 188с.
- Розенберг A.M. и др. Расчет и проектирование твердосплавных деформирующих протяжек и процесса протягивания. Киев, Наукова думка, 1978 г, 256с.
- Розенберг A.M. Физические явления при деформирующем протягивании и резании пластических материалов. Киев, институт сверхтвердых материалов АН УССР, 1978 г, 187 с.
- Розенберг A.M., Розенберг O.A. Механика пластического деформирования в процессах резания и деформирующего протягивания. Киев, Наукова думка, 1990 г, 320с.
- Рыбакова Л.М., Куксенова Л. И. Структура и износостойкость металла. М., Машиностроение, 1982 г, 209с.
- Рыжов Э.В., Харченков B.C. Экспериментальное исследование шероховатости поверхности в условиях избирательного переноса. В кн.: Применение избирательного переноса в узлах трения машин. М., ВИСМ, 1976 г, т.1, с.29−34.
- Рыжов Э.В., Харченко B.C. Расчет шероховатости поверхности в условиях избирательного переноса в узлах трения машин. М., ВИСМ, 1976 г, т.1, с.35−40.
- Ряховский A.M. К расчету коэффициента трения конструкционных материалов. Трение и износ. 1989 г, т.10, вып.№ 5, с.851−860.
- Симахин Я.А. Исследование процесса обработки цилиндрических отверстий многозубыми дорнами. Дисс. на соискание ученой степени к.т.н., Челябинск, 1966 г, 198с.
- Скворцов В.Ф. Исследование процесса дорнования как метода повышения точности и качества поверхности отверстия в термообработанных деталях. Дисс. на соискание ученой степени к.т.н., Куйбышев, 1981 т, 204с.
- Солонин И.С. Математическая статистика в технологии машиностроения. М., Машиностроение, 1972 г.
- Симонов И.В. Повышение производительности и качества дорнования на основе применения твердых смазочных покрытий. Дисс. на соискание ученой степени к.т.н., М., МАМИ, 1985 г, 204с.
- Спиридонов A.A. Планирование эксперимента при исследовании технологических процессов. М., Машиностроение, 1981 г, 184с.
- Смелянский В.М. Механика упрочнения поверхностного слоя деталей машин в технологических процессах ППД. М., Машмир., 1992 г, 60с.
- Силин С.С., Макаров В. Н. Экономический критерий оценки эффективности смазочно-охлаждающей жидкости. М., ЦИОНТ, ПИК ВИНИТИ № 3,с.83−86.
- Сторожев И.В., Попов В. А. Теория обработки металлов давлением. М., Машиностроение, 1971 г, 424с.
- CT СЭВ 545−77. Прикладная статистика. Правила оценки анормальности результатов наблюдений. М., изд.-во стандартов, 1978 г.
- Тарновский И.Я. и др. Теория обработки металлов давлением. М., Металлургиздат, 1963 г.
- Томило Э. А., Буйлов Е. А. Поля напряжений и глубина упрочнения полых цилиндров при деформирующем протягивании. //Производство подшипников, № 2,1998 г. с. 32−34.
- Уляхин Ю.М. Исследование метода обработки отверстий деформирующе-режущими протяжками с помощью ЭВМ. Дисс. к.т.н., М., МАМИ, 1982 г, 189с.
- Цеханов Ю.А. Механика процесса деформирующего протягивания. Автореферат на соискание ученой степени к.т.н., Воронеж, 1974 г.
- Цеханов Ю.А. Определение пластического коэффициента трения с помощью линий скольжения. Кузнечно-штамповочное производство. 1977 г, № 2, с. 18−19.
- Чертавских А.К., Белосевич В. К. Трение и технологическая смазка при обработке металлов давлением. М., Металлургия, 1968 г, 361с.
- Черкесов В.Н. Повышение эффективности деформирующего протягивания за счет регулирования процесса избирательного переноса. Дисс. на соискание ученой степени к.т.н., М., МАМИ, 1997 г, 123с.
- Шацких И.И. Повышение эффективности метода деформирующе-режущего протягивания отверстий на основе совершенствования его характеристик. Дисс. к.т.н., М., МАМИ, 1988 г, 178с.
- Шехтер P.C. Вариационный метод в инженерных расчетах. М., Мир, 1971 г.
- Шнейдер Ю.Г., Бунга Л. А., Вялло A.A. Качество поверхности и эксплуатационные свойства деталей, обработанных давлением. Станки и инструмент, 1967 г, № 1, с. 14−17.
- Шнейдер Ю.Г. Инструмент для чистовой обработки металлов давлением. JI., Машиностроение, 1971 г, 247с.
- Щедрин A.B. Повышение эффективности деформирующе-режущего прошивания на основе совершенствования динамических характеристик метода обработки. Дисс. к.т.н., М., МАМИ, 1991 г, 246с.
- Ярославцев В.М. Расчет глубины пластически деформированного слоя при обкатке роликом с первоначальным контактом по линии. Изв., Вузов, Машиностроение, № 6, 1975 г.1. Зав. кафедройА^И-—проф. д.т.н. О-рДЧГ^-М. Кузнецов."" «1998 г.