Теория и практика переработки отходов алюминия в роторных наклонных печах
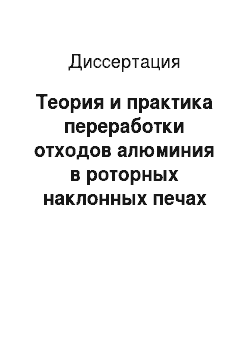
Выявлено, что уровень равновесной концентрации остаточного алюминия в шлаке определяется габаритами и формой РНП, интенсивностью ее вращения, массой шихты, консистенцией шлака, наличием в шлаке крупных твердых кусков, температурой шлака, составом металла и флюса. На основе аналитических, экспериментальных и модельных исследований проведено теоретическое обобщение закономерностей физико-химических… Читать ещё >
Содержание
- Раздел 1. Литературный обзор
- 1. 1. Современное состояние производства вторичного алюминия
- 1. 2. Техника и технология получения вторичного алюминия
- 1. 3. Влияние ресурсной базы производства вторичного алюминия на развитие роторных наклонных печей
- 1. 4. Технологии получения вторичного алюминия из низкосортных алюминий содержащих отходов
- 1. 5. Роторные наклонные печи в России
- 1. 6. Состав флюса — решающий фактор в увеличении эффективности переработки алюминиевых отходов в РНП
- 1. 7. Выводы
- Раздел 2. Исследования процессов переработки алюминиевых отходов в роторных наклонных пенах
- 2. 1. Изучение процессов при плавлении отходов алюминия во вращающемся тигле
- 2. 2. Особенности плавки алюминиевых отходов в лабораторной РНП
- 2. 2. 1. Окисление магния при плавке в РНП
- 2. 3. Эксперименты на опытно-промышленной РНП
- 2. 4. Роль масштабного фактора при переработке отходов алюминия в РНП
- 2. 5. Коалесценция в РНП
- 2. 5. 1. Обзор литературных источников по коалесценции
- 2. 5. 2. Анализ опубликованных экспериментальных данных
- 2. 5. 3. Коалесценция в жидком флюсе и реальные плавки
- 2. 5. 4. Влияние на коалесценцию механического воздействия
- 2. 6. Влияние геометрии печи на эффективность ее работы
- 2. 7. Другие проявления масштабного фактора
- 2. 8. Выводы
- Раздел 3. Влияние физико-химических процессов в РНП на технологические потери при плавке
- 3. 1. Формализация процессов, происходящих в РНП при различных технологических режимах
- 3. 2. Исследование процессов коалесценции на заключительном этапе плавки. 103 3.3 Субсоединения. Потери алюминия за счет химических реакций
- 3. 4. Потери металла на различных этапах плавки
- 3. 4. 1. Влияние состава флюса, температуры и времени
- 3. 4. 2. Влияние примесей и легирующих элементов на потери металла в сплавах алюминия
- 3. 4. 3. Потери алюминия из-за окисления печной атмосферой
- 3. 4. 4. Потери металла от химического взаимодействия алюминия или легирующих компонентов сплава с флюсами
- 3. 4. 5. Замешивание капель алюминия в шлаке
- 3. 4. 6. Окисление алюминия остаточным кислородом, влагой и органическими примесями, вносимыми в расплавленный металл
- 3. 4. 7. Общие потери алюминия
- 3. 5. Выводы
- Раздел 4. Влияние состава флюса на структуру солевого шлака
- Оптимизация состава флюса
- 4. 1. Структура и свойства солевых шлаков
- 4. 2. Повышение вязкости флюса оксидами. Экспериментальные данные
- 4. 3. Влияние оксидов на плотность расплавленных солей
- 4. 4. Механизм повышения вязкости флюса оксидами
- 4. 5. Модель оксидных блоков
- 4. 6. Связь модели оксидных блоков с реальными условиями производственных процессов
- 4. 7. Оптимизация состава флюса
- 4. 7. 1. Общие вопросы рециклинга алюминиевого сырья
- 4. 7. 2. Межфазное натяжение алюминия и его сплавов в расплавленных солях
- 4. 7. 3. Смачивание алюминия расплавленными солями
- 4. 7. 4. Смачивание оксидов расплавленными солями
- 4. 7. 5. Применяемые покровно-защитные флюсы
- 4. 7. 6. Оптимальное соотношение между NaCl и KCl во флюсе
- 4. 7. 7. Влияние добавок к смеси NaCl-KCl на выход годного
- 4. 8. Температуры плавления и кристаллизации флюсов различного состава
- 4. 9. Исследования влияния добавок фторидов к флюсу на выход металла
- 4. 10. Выводы
- Раздел 5. Математическое моделирование. Компьютерная оптимизация оборудования и процессов
- 5. 1. Общие представления об особенностях процессов в печи при вращении
- 5. 2. Моделирование нестационарного теплообмена с футеровкой
- 5. 2. 1. Постановка задачи
- 5. 2. 2. Численный метод решения уравнения теплопроводности
- 5. 2. 3. Нагрев футеровки во вращающейся печи
- 5. 2. 4. Численное решение одномерного уравнения теплопроводности для цилиндрической стенки
- 5. 2. 5. Влияние неодномерности геометрии на точность расчёта нагрева стенки
- 5. 2. 6. Модель теплообмена с шихтой во вращающейся печи
- 5. 2. 7. Расчёт нагрева поверхностного слоя шихты во вращающейся печи
- 5. 2. 8. Теплообмен между футеровкой и шихтой во вращающейся печи
- 5. 3. Моделирование факельного горения
- 5. 3. 1. Моделирование турбулентной аэродинамики многокомпонентной смеси
- 5. 3. 2. Горение газового топлива
- 5. 3. 3. Теплоотдача от факела к поверхности шлака, расплава и футеровке за счет конвективного и радиационного теплообмена
- 5. 3. 4. Результаты моделирования процесса горения с использованием параметров реальной печи
- 5. 3. 5. Анализ результатов моделирования процессов горения. Сравнение с экспериментальными данными
- 5. 3. 6. Выбор геометрии при проектировании роторной печи
- 5. 3. 7. Анализ влияния размеров печи на технологические параметры
- 5. 4. Моделирование движения расплава в роторных печах
- 5. 5. Равновесное моделирование химических процессов при плавке отходов алюминия
- 5. 5. 1. Модель химического равновесия для проведения расчета параметров процессов при получении вторичного алюминия
- 5. 6. Моделирование и прогнозный расчет технологических результатов при переработке отходов в роторных печах
- 5. 6. 1. Общие представления об этапах процесса прогрева шихты
- 5. 6. 2. Моделирование теплового процесса прогрева шихты и образования расплава
- 5. 6. 3. Моделирование динамических режимов
- 5. 6. 4. Результаты расчета выхода алюминия в роторной печи
- 5. 7. Выводы
- Раздел 6. Переработка алюминийсодержащих шлаков
- 6. 1. Шлаки алюминиевого производства, свойства и классификация
- 6. 2. Совершенствование процессов подготовки шлаков для переработки в РНП
- 6. 3. Сравнение стоимости переработки шлаков на различных печных агрегатах
- 6. 4. Выводы
- Раздел 7. Контроль технологического процесса плавки на РНП. Разработка новых конструкций печей и технологий плавки алюминиевых отходов
- 7. 1. Измерение момента на оси привода роторной наклонной печи
- 7. 1. 1. Общая картина изменения нагрузки на привод барабана в процессе плавки
- 7. 2. Измерение температуры отходящих газов над горловиной РНП
- 7. 3. Использование инфракрасного дистанционного измерителя температуры шихты
- 7. 4. Измерение температуры шихты и связь ее с процессами, происходящими в РНП
- 7. 5. Технологический мониторинг. Автоматизация производства
- 7. 6. Использование мониторинга для повышения эффективности производства
- 7. 7. Разработка универсальной конструкции РНП
- 7. 8. Металлургический комплекс ОАО «МОСОБЛПРОМОНТАЖ», как главный результат данной работы
- 7. 9. Выводы
- 7. 1. Измерение момента на оси привода роторной наклонной печи
- Раздел 8. Экологические проблемы и состояние отрасли вторичной переработке отходов алюминиевого сырья
- 8. 1. Виды сырья и виды оборудования
- 8. 2. Выбросы загрязняющих веществ. Виды выбросов и причины выбросов
- 8. 3. Методы очистки выбросов и оборудование, применяемое на заводах России
- 8. 4. Экологические требования законодательства и регулирование
- 8. 5. Перспективы развития отрасли в плане экологических требований
- 8. 6. Выводы
Теория и практика переработки отходов алюминия в роторных наклонных печах (реферат, курсовая, диплом, контрольная)
Вторичный алюминий — это прежде всего накопленная человечеством энергия при производстве первичного алюминия, которую необходимо в свете последних энергетических проблем использовать бережно и эффективно, как по экономическим так и по экологическим соображениям. Это возможно при эффективной переработке отходов алюминия. Не нужно никаких политических решений, чтобы создать производство по переработке отходов алюминия. Производство высококачественных алюминиевых сплавов развивалось уже в то время, когда думали, что запасы естественного сырья неисчерпаемы, по причинам того, что затраты энергии на первичное производство значительно больше.
Однако в России ситуация несколько иная, чем в развитых странах. Производство первичного алюминия из-за сильнейшего государственного лоббирования имеет рентабельность свыше 100%, в отличие от производства вторичного алюминия, которая как любая отрасль машиностроения имеет рентабельность не более 15%, рис. 1.1. Производством вторичного алюминия в России [116] по данным Межрегионального Центра вторичной цветной металлургии на 2005 год занимается более 180 официальных предприятий, на которых официально производится 400 000 тонн, причем 165 тыс. т на 8 предприятиях, Рис. 1.1 Выпуск вторичных сплавов в России, [109].
800 600 С 400 ^ 200 0.
1—?95.
Ч43 034,.
— о—о—.
2002 2003 год.
Производство сплавов Л Экспорт сплавов «Экспорт скрапа.
В связи с этим, данной отрасли не придается никакого, тем более важного значения, и научное и технологическое развитие ее держится только на энтузиазме нескольких мелких компаний. Поэтому любые их успехи и достижения следует поддерживать как важную часть всей Российской науки.
Рис. 1.2 Количество выбросов вредных отходов при производстве вторичного (голубой цвет) и первичного алюминия (черный цвет).
Особо следует отметить экологические проблемы, возникающие при производстве первичного алюминия в условиях растущих требований к защите окружающей среды. Фтористые соединения и бензапирен, выбрасываемые в атмосферу при производстве алюминия, являются одними из самых опасных факторов с точки зрения воздействия на человека [3,5,9]. Количество выбросов при вторичном производстве составляет всего лишь 5% от выбросов производства первичного алюминия на 1 т, рис. 1.2.
Непрерывное расширение областей применения алюминия и увеличение объемов его потребления привело к увеличению количества мелкодисперсных и загрязненных отходов с содержанием алюминия от 40 до 85%, эффективная переработка которых невозможна на традиционном оборудовании, вследствие нестабильного химического и дисперсного состава. Поэтому в последние годы в промышленно развитых странах наблюдается рост интереса к разработке новых плавильных агрегатов, имеющих более высокие технологические и экологические характеристики. В связи с этим, разработка научной концепции по созданию современных технологий извлечения алюминия из отходов алюминия с применением роторных наклонных печей (РНП), создание новых конструкций печей, для внедрения на российских предприятиях вторичной металлургии алюминия являются актуальными.
Цель работы заключается в разработке теоретических основ переработки отходов алюминия в РНП, концепции создания новых конструкций печей и технологий на основе применения научно-обоснованных методов исследований для решения комплексной государственной задачи утилизации отходов производства.
Объектом исследования является класс плавильных роторных наклонных печей для переработки отходов алюминия и физико-химические процессы, происходящие при плавке алюминиевых отходов. На защиту выносятся:
— Теория физико-химических процессов переработке отходов алюминия в РНП.
— Классификация и механизмы процессов, происходящих в шихте, образование структуры солевых шлаков.
— Методики исследований, анализ закономерностей и обобщенные результаты экспериментов.
— Механизмы процессов образования субсоединений при переработке отходов алюминия в расплавах галогенидов.
— Математические модели процессов теплообмена, аэродинамики и выхода металла;
— Результаты математического моделирования и технико-экономической оптимизации РНП.
— Новые составы флюса для использования в РНП при переработке отходов алюминия.
— Новые конструкции печей и технологические приемы, позволяющие увеличивать эффективность процесса плавки отходов алюминия в роторных наклонных печах.
— Классификация и результаты исследований свойств аломинийсодержащих шлаков с учетом особенностей их формирования и хранения, технологические процессы подготовки шлака к переработке в РНП.
— Комплексная система контроля технологическими процессами. Диссертация состоит из введения, 8 разделов, изложена на 348 страницах текста и содержит 257 рисунков, 49 таблицы, список литературы из 210 наименований.
Основные выводы и результаты.
1. Впервые в России разработаны теоретические основы переработки отходов алюминия в РНП с применением научно-обоснованных методов исследований, для решения комплексной государственной задачи утилизации отходов производства.
2. Впервые выявлены закономерности механического воздействия на шихту и оксидные оболочки при плавке отходов алюминия в РНП, связанные с размерами и конструкциями печей, впервые введено понятие масштабного фактора для РНП и определены границы его применения.
3. Введены новые понятия, классификация и определена схема процессов перехода элементов шихты в расплавленную ванну металла, разработаны научные методы определения стадий технологического процесса переработки отходов алюминия в РНП, с учетом характера и механизмом коалесценции. Определены механизмы коалесценции, происходящие при плавке отходов алюминия на разных этапах плавления.
4. Впервые выявлен механизм образования структуры солевого шлака в зависимости от компонентов шихты, основанный на предположении об определяющей роли оксидов, имеющих форму пластинок, которые определяют свойства фшоса при его выборе. Введено понятие оксидных блоков. Установлено, что при избытке флюса оксидные пластинки определяют его вязкость и тиксотропные свойства шлака. С позиций модели оксидных блоков даны объяснения различным эффектам, наблюдающимся при плавках алюминиевого сырья.
5. Установлен механизм возникновения динамического равновесия между шихтой и ванной жидкого металла, при котором движение капель жидкого алюминия в ванну, компенсируется захватом капель из ванны в солевой шлак. Этот механизм определяет экстремальные зависимости величины металлургического выхода годного от основных технологических параметров, температуры плавки, времени плавки, скорости вращения печи.
6. Выявлено, что уровень равновесной концентрации остаточного алюминия в шлаке определяется габаритами и формой РНП, интенсивностью ее вращения, массой шихты, консистенцией шлака, наличием в шлаке крупных твердых кусков, температурой шлака, составом металла и флюса. На основе аналитических, экспериментальных и модельных исследований проведено теоретическое обобщение закономерностей физико-химических процессов, происходящих в процессе плавки алюминиевых отходов, что позволило разработать методику подбора флюса для переработки отходов алюминия.
7. Установлены закономерности образования субсоединений при плавке отходов алюминия, потери за счет которых, сопоставимы с потерями за счет окисления.
8. Впервые создан комплекс математических моделей, с помощью которых реализована технико-экономическая оптимизация РНП, технологические процессы плавки, разработаны новые конструкции печей, методика управления РНП.
9. Разработана современная классификация алюминийсодержащих шлаков, позволяющая увеличить эффективность технологии их переработки.
10.Установлено существование оптимального сочетания режимных (частота вращения, тепловая мощность горелки) и конструктивных (диаметр, угол наклона ее оси вращения) параметров РНП в зависимости от производительности и конкретных экономических условий.
11. У станов лена целесообразность повышения скорости вращения РНП для увеличения эффективности тепловой работы при переработке высокодисперсных шлаков и повышения стойкости футеровки.
12. Определена оптимальная ориентация факела на футеровку, наиболее выгодная с точки зрения повышения коэффициента использования теплоты, снижения потерь алюминия со шлаками ориентация факела на футеровку.
13. Обоснованы, разработаны, исследованы, реализованы в конструкциях и запущены в промышленную эксплуатацию РНП объемом 800 кг, 1000 кг, 3000 кг, 3500 кг, 10 000 кг (2 пгг), что позволило увеличить производство алюминия при переработке низкосортного сырья и уменьшить объем отходов, который захоранивался на промышленных полигонах.
14.Экономический эффект от внедрения результатов работы составил более 76 млн. рублей без учета снижения экологической нагрузки на окружающую среду.
Список литературы
- Прокопов И. Герой нового времени. Алюминий в XXI веке. Металлы Евразии // -2000.- № 5- С.46−49.
- Давыдов В.Г. Современное состояние и некоторые актуальные проблемы использования алюминиевых сплавов//Цветные металлы.-1999.-№ 8 С. 49−53.
- Pawlek R.P. Secondary Aluminum Industry Annual Review// Light metal Age, August -2000.-P. 13−20.
- The Aluminium Situation of the USA. //Aluminium, 76 Jahrgang, 14−2000.- p.6−8.
- Производство алюминия / В. Г. Терентьев, Р. М. Школьников, И. С. Гринберг, А. Е. Черных, Б. И. Зельберг, В. И. Чалых. Иркутск- 1998. — 350 с.
- Г. В. Галевский, Н. М. Кулагин, М. Я. Минцис. Металлургия вторичного алюминия: Учебное пособие для вузов. -Новосибирск: Наука, Сибирское предприятие РАН, 1988. -289 с.
- Технология вторичных цветных металлов. Под ред. И. Ф. Худякова.- М.: Металлургия, 1981.- 277 с.
- Altenpohl Dietrich G. Aluminum: technology, application and environment, Washington, D.C., 1999.- 473 p.
- Г. В. Галевский, Н. М. Кулагин, М. Я. Минцис. Экология и утилизация отходов при производстве алюминия. -Новосибирск: Наука, Сибирское предприятие РАН, 1996. -146 с.
- Aluminium Industry Energy Conservation, Workshop VIII // Washington, Sept. 1984.pp.59.-61−71.-123−132.
- J. H. L. van Linden, Aluminium Recycling. Everybody’s Business, Technological Challenges and Opportunities. Light Metals: 1990.- p. 675−681.
- Pinkham M. Big player aims higher still. IMCO Recycling, Aluminium today, June/July -1999.- p. 43−44.
- Schroers I. Automobile Recycling Today and Tomorrow. Light Metals 1994. p. 1129−1135.
- Пал М. Х. Энергия и защита окружающей среды. Падерборн: Изд-во FIT, Verlag. 1996, -449 с.
- Atkins P. R. Recycling Can Cut Energy Demand Dramatically. Engineering and Mining Journal, May 1973.-№ 5 Vol. 174
- Steverson W. Bryan. MRFs and UBCs: A Concern Yet an Opportunity. Light Metals 1995.-p. 1303−1307.
- Patricia A. Plunkert, Aluminium Recycling in the United States. A Historical Perspective, Second International Symposium Recycling of Metal and Engineered Materials, 1990, -p. 61- 68.
- Локшин M.3., Макаров Г. С. Современные тенденции в рециклировании алюминия.// Цветные металлы. 2001.- № 11.- С. 1−7.
- Proc. 8th International Secondary Aluminium Conference, Singapore, 2000.
- Ларионов Г. В. Вторичный алюминий. -M.: Металлургия, 1967.- 271 с.
- Радзиховский В.А. Машины и технологии непрерывного литья во вторичной цветной металлургии.- М.: Металлургия, 1979.- 48 с.
- Kovohute Mnisek finds synergy in pump and multi-well. //Aluminium today, June/July 2000. P. 38−40.
- Electromagnetic systems for improved recycling. //Aluminium today. June/July 2000.-p. 41−42
- Фишер А.Я. Техника производства вторичных алюминиевых сплавов за рубежом. М.: Цветметинформация, 1970.- 64 с.
- Шкляр М.С. Печи вторичной цветной металлургии. М.: Металлургия, 1987.216 с.
- Шлотт Г. Вторичные цветные металлы (Материалы Лейпцигской конференции стран членов СЭВ и СФРЮ). -М.: Цветметинформация, 1971. -74−80с.
- Becker J. S, Heffron F. The Changing Role of Oxygen-Based Combustion in Aluminum Melting.// Light Metal Age, June, 1994.
- Paget Michael W., Heffron James F., Richer Pierre The Evolution Of Rotary Melting At Recyclage Aluminum Quebec Inc: Two Aluminum Dross Processing Plants June. 1994
- Schmidt H.D. Stirring Device in Rotary Drum Furnaces. ALUMINIUM. 76, Jahrgang. 2000, !/2, P.34.
- Койбаш В.А., Резняков А. А. Оборудование предприятий вторичной цветной металлургии. -М.: Металлургия, 1976.- 231 с.
- Новое оборудование вторичной металлургии./ Сост. Хоменко Л.Е.// М., ЦНИИцветмет экономики и информации., 1984.-Зс. (Вторичная металлургия цветных металлов и химическое производство цветной металлургии: Экспресс-информация- выпуск 14).
- Андреев А.Д., Гогин В. Б., Макаров Г. С. Высокопроизводительная плавка алюминиевых сплавов. -М.: Металлургия, 1980, — 136 с. 34.