Моделирование процесса накатывания резьбы на стержневых изделиях с целью повышения точности и качества
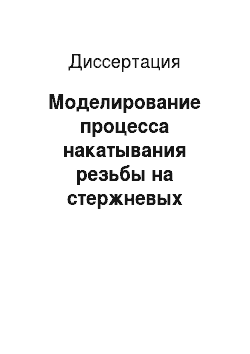
Разработана методика аппроксимации непрерывными функциональными зависимостями экспериментальных кривых упрочнения и экспериментальных значений термомеханических коэффициентов для случаев холодного и горячего пластического деформирования. В ее основу положен критерий метода наименьших квадратов. Для случая холодного деформирования получены экспоненциальные зависимости сопротивления деформации… Читать ещё >
Содержание
- 1. ПРОБЛЕМЫ ФОРМИРОВАНИЯ РЕЗЬБ НА СТЕРЖНЕВЫХ ИЗДЕЛИЯХ ПЛАСТИЧЕСКИМ ДЕФОРМИРОВАНИЕМ
- ЗАДАЧИ ИССЛЕДОВАНИЯ
- 1. 1. Способы формирования наружных резьб
- 1. 2. Исследования процессов накатывания наружных резьб
- 1. 3. Точность резьб и проблемы обеспечения точности при накатывании
- 1. 4. Задачи исследования
- 2. РЕОЛОГИЧЕСКИЕ СВОЙСТВА СТАЛЕЙ, ПРИМЕНЯЕМЫХ ПРИ ИЗГОТОВЛЕНИИ СТЕРЖНЕВЫХ ИЗДЕЛИЙ С РЕЗЬБОЙ
- 2. 1. Сопротивление деформации при холодном пластическом деформировании и аппроксимация кривых упрочнения
- 2. 2. Сопротивление деформации при горячем пластическом деформировании. Термомеханические коэффициенты и их аппроксимация
- 2. 3. Выводы
- 3. ИССЛЕДОВАНИЕ ПРОЦЕССА ФОРМИРОВАНИЯ РЕЗЬБОВЫХ ПРОФИЛЕЙ ПЛАСТИЧЕСКИМ ДЕФОРМИРОВАНИЕМ
- 3. 1. Вариационное уравнение и функционал принципа минимума полной работы деформации жестко-пластической упрочняемой среды
- 3. 2. Математическое моделирование процесса внедрения клина треугольного сечения в упрочняемое жестко-пластическое полупространство
- 3. 3. Математическое моделирование процесса внедрения трапецеидального выступа резьбонакатного инструмента в металл заготовки
- 3. 4. Расчет силовых параметров процесса формирования профиля резьбы
- 3. 5. Расчет силового воздействия на инструмент при накатывании наружной резьбы плоскими плашками
- 3. 6. Выводы
- 4. ПРОГНОЗИРОВАНИЕ ИЗНОСОСТОЙКОСТИ РЕЗЬБОНАКАТНОГО ИНСТРУМЕНТА
- 4. 1. Основные положения метода конечных элементов в задачах теории упругости
- 4. 2. Напряженно-деформированное состояние в трапецеидальном выступерезьбонакатного инструмента
- 4. 3. Расчет энергосиловых параметров трения на контактной поверхности выступа плашки при накатывании
- 4. 4. Расчет износа выступов плашки и совершенствование ее конструкции
- 4. 5. Выводы
- 5. ПРОГНОЗИРОВАНИЕ ТОЧНОСТИ НАРУЖНЫХ РЕЗЬБ, СФОРМИРО ВАННЫХ НАКАТЫВАНИЕМ
- 5. 1. Методика определения погрешностей диаметров накатанных резьб
- 5. 2. Применение методики оценки погрешностей резьб для случая холодного накатывания
- 5. 3. Выводы
- 6. СОВЕРШЕНСТВОВАНИЕ ПРОЦЕССА ГОРЯЧЕГО НАКАТЫВАНИЯ РЕЗЬБЫ НА ПУТЕВЫХ ШУРУПАХ
- 6. 1. Расчет энергосиловых параметров процесса горячего накатывания резьбы на путевых шурупах
- 6. 2. Прогнозирование износостойкости плоских плашек для накатывания резьбы путевых шурупов
- 6. 3. Прогнозирование точности резьбы путевых шурупов, сформированной горячим накатыванием плоскими плашками
- 6. 4. Выводы
Моделирование процесса накатывания резьбы на стержневых изделиях с целью повышения точности и качества (реферат, курсовая, диплом, контрольная)
Стержневые крепежные изделия с резьбой (болты, винты, шурупы, шпильки и т. п.) находят широкое применение в различных отраслях промышленности. Как правило, они составляют 60−70% от общего числа деталей, входящих в конструкцию машин [1,2]. В настоящее время при массовом производстве таких изделий формирование резьбы осуществляют, как правило, накатыванием. Применение процессов накатывания наружных резьб по сравнению с процессами нарезания обеспечивает повышение производительности труда примерно в 3−5 раз, экономию металла, снижение шероховатости поверхности резьбы, а также повышение надежности и долговечности деталей в несколько раз [1,3].
При накатывании резьбы в процессе пластической деформации изменяется физическая природа и физико-механические свойства поверхностного слоя металла: за счет наклепа повышаются твердость и прочность, возникают остаточные сжимающие напряжения с благоприятным распределением их по сечению детали, видоизменятся форма и ориентация кристаллов, металл накатанной резьбы приобретает волокнистую текстуру и становится анизотропным. Таким образом, в результате изменения физико-механических свойств увеличивается сопротивление поверхностного слоя пластической деформации и разрушению, а также значительно повышается усталостная прочность деталей [2].
Исследованию процессов накатывания резьб посвящены работы М.И. Пи-саревского [1,3−6], Ю. А. Миропольского, Э. П. Лугового [2,7−9], A 3. Журавлева [10−13], В. Г. Якухина [14,15], И. А. Биргера, Г. Б. Иосилевича [16,17] и др. Исследования, проведенные указанными авторами, в основном направлены на изучение технологии резьбонакатного производства. Между тем, недостаточно внимания уделяется исследованию процесса образования профиля резьбы под давлением инструмента. В частности, малоизученной на сегодняшний день является проблема влияния изменения реологических свойств металла в ходе пластической деформации на энергосиловые параметры процесса накатывания. Кроме этого, современное машиностроение предъявляет жесткие требования к точности резьбовых соединений, которая обеспечиваются стабильностью процесса накатывания. Однако, несмотря на множество трудов, посвященных исследованию процессов образования резьб, проблема получения изделий необходимой точности и качества не решена в полной мере и в настоящее время.
Точность резьбы зависит от колебаний различных факторов процесса накатывания (размеры заготовки, механические свойства, условия трения, температура и т. п.), а также жесткости силовой системы станка. На стадии проектирования технологического процесса накатывания резьбы необходимо прогнозировать влияние этих колебаний на погрешности геометрических размеров получаемых резьб. В не меньшей мере точность готовых изделий зависит и от совершенства конструкции накатного инструмента, профиль которого должен идеально соответствовать профилю получаемой резьбы. Как известно, в производственных условиях часто наблюдается быстрый износ рабочей части инструмента и, как следствие, снижение точности изделий. Износостойкость накатного инструмента, в свою очередь, существенно зависит от усилий накатывания, а также от материала, из которого выполнен инструмент, его геометрических параметров и способа обработки его поверхности. При разработке технологии накатывания (выбор оборудования, поиск рациональных скоростных и температурных режимов деформирования) и проектировании инструмента нужно точно знать усилия, действующие на инструмент. Для оценки прочности и износостойкости инструмента интерес представляет также схема распределения сжимающих напряжений в тех частях инструмента, которые осуществляют формирование профиля резьбы, а также распределение напряжений трения по их контактной поверхности. Для осуществления подобного рода расчетов также необходимо наличие соответствующих методов. Несмотря на то, что в последнее время и предлагались некоторые методы для осуществления расчетов подобного рода, не все они, как будет показано далее, обеспечивают требуемую точность. Поэтому очевидна необходимость разработки новых математических моделей и методов, применение которых к расчетам процессов различных способов накатывания позволит правильно оценивать требуемые энергозатраты, а также проектировать износостойкий накатной инструмент.
Таким образом, целью настоящей работы являлось повышение точности размеров накатанных резьб за счет обеспечения стабильности процесса накатывания, а также повышение износостойкости резьбонакатного инструмента за счет совершенствования его конструкции. Основными научными результатами, полученными впервые, являются:
— математическая модель процесса формирования профиля резьбы, в основу которой положен вариационный принцип минимума полной работы деформации, позволяющая при расчетах энергосиловых параметров учитывать изменение значения сопротивления деформации в зависимости степени деформации, температуры и скорости деформации;
— методика расчета работы сил трения и износа на контактной поверхности накатного инструмента;
— методика, позволяющая оценивать влияние колебаний геометрических, реологических, механических и технологических факторов процесса накатывания на точность размеров получаемых резьб с учетом жесткости резьбонакат-ных станков.
Результаты работы использованы в ОАО «Магнитогорский калибровочный завод» при разработке нового инструмента и технологии горячего накатывания резьбы на путевых шурупах.
ОБЩИЕ ВЫВОДЫ.
1. Разработана методика аппроксимации непрерывными функциональными зависимостями экспериментальных кривых упрочнения и экспериментальных значений термомеханических коэффициентов для случаев холодного и горячего пластического деформирования. В ее основу положен критерий метода наименьших квадратов. Для случая холодного деформирования получены экспоненциальные зависимости сопротивления деформации от логарифмической степени деформации для свинца и сталей 10, 20, 35, 40Х. Для случая горячего деформирования для сталей 08кп, 25 и 45 получены экспоненциальные выражения для термомеханических коэффициентов, выражающих зависимость сопротивления деформации от логарифмической степени деформации, температурных и скоростных условий деформационного процесса.
2. Разработана математическая модель процесса формирования профиля резьбы, в основу которой положен вариационный принцип минимума полной работы деформации. Модель позволяет учитывать влияние на усилие деформирования сопротивления деформации, температуры, скорости деформации, а также коэффициента трения при холодном и горячем накатывании. Используя составленную программу для ЭВМ, был рассчитан ряд конкретных технологических процессов накатывания. Экспериментальная проверка показала, что расхождение результатов теоретических расчетов и опытных данных не превышает 10−12%. Разработанная модель использовались при расчетах радиального усилия накатывания резьб плоскими плашками, износостойкости резьбонакатного инструмента, а также при прогнозировании точности накатанных резьб.
3. Используя метод конечных элементов, проведены расчеты напряженно-деформированного состояния в выступе накатного инструмента при формировании профиля резьбы. Анализ результатов позволил сделать вывод о том, что местами наибольшей концентрации напряжений являются те области выступа, которые осуществляют формирование верхней части профиля резьбы.
4. Проведены расчеты работы сил трения и износа на контактных поверхностях выступов плоских плашек при накатывании. Установлено, что применение в качестве материала рабочих частей плашек твердых сплавов вместо инструментальных сталей обеспечивает снижение величины износа в 1,5−1,7 раза.
5. Разработана новая конструкция накатных плашек, у которых в специальном пазу в конце заборной и начале калибрующей частей устанавливается вставка из высокопрочного износостойкого материала. При достижении определенной степени износа рабочей части вставки имеется возможность регулирования ее положения в пазу с помощью винтов. Применение разработанного технического решения позволяет повысить срок службы плашек.
6. Разработана методика прогнозирования точности размеров накатанных наружных резьб. Методика позволяет рассчитывать отклонения диаметров готовых резьб, которые возникают в результате малых колебаний различных факторов процесса накатывания. При этом учитывается жесткость резьбонакатных станков. Выполнены соответствующие расчеты для ряда конкретных случаев процесса накатывания, на основании которых установлено, что, при равных долях отклонений факторов от их номинальных значений, наибольшее влияние на колебания размеров получаемой резьбы оказывают колебания диаметров заготовки (70−80% от суммарной погрешности), а наименьшее — колебания коэффициента трения (менее 1% от суммарной погрешности).
7. Проведено исследование процесса накатывания плоскими плашками резьбы на путевых шурупах. Установлено, что применение горячего способа накатывания обеспечивает для плашек 6-й класс износостойкости. В то же время холодное накатывание дает лишь 5-й класс. Выявлено, что применение твердосплавных вставок на плашках позволяет на единицу повысить разряд износостойкости. Кроме этого, рекомендовано применять для обработки рабочих поверхностей плашек шлифование, которое также обеспечивает повышение разряда износостойкости на единицу. Использование горячего накатывания плоскими плашками вместо накатывания с использованием трех-роликовых станков в условиях ОАО «Магнитогорский калибровочный завод» позволит повысить качество изделий, снизить долю брака по диаметру и искривлению стержня готовой резьбы, а также затраты на производство нового инструмента, сокращения простоев и снижения стоимости изготовления инструмента.
8. Установлено, что при рекомендуемом минимально допустимом значении коэффициента жесткости станка для накатывания резьбы путевых шурупов ЦП-54, равном 500 кН/мм, и при 10%-х отклонениях диаметра заготовки, коэффициента трения, базисного сопротивления деформации сг0, температуры заготовки и скорости деформации от их номинальных значений диаметры получаемой резьбы укладываются в допустимое поле допуска (± 500 мкм).
Список литературы
- Писаревский М.И. Накатывание точных резьб, шлицев и зубьев. Л.: Машиностроение, 1973. — 200 с.
- Миропольсшй Ю.А., Луговой Э. П. Накатывание резьб и профилей. М.: Машиностроение, 1976. — 175 с.
- Писаревский М. И, Самсонов В И. Новое в технологии накатывания резьб, шлицев и зубьев. ЛДНТП, 1978. — 20 с.
- Писаревский М.И. Накатывание точных резьб: Автореф. дисс. на соиск. уч. ст. канд. техн. наук. ЛИИ им. М. И. Калинина, 1954
- Писаревский М.И. Накатывание точных резьб и шлицев. М.-Л.: Машгиз, 1963.- 180 с.
- Писаревский М.И. Новый инструмент для накатывания резьб и шлицев. М -Л: Машиностроение, 1966. — 152 с.
- Мирополъский Ю.А. Исследование прессов-автоматов для объемной штамповки. М.: Машиностроение, 1968. — 155 с.
- Мирополъский Ю.А., Луговой Э. П., Дмитриенко В. Д. Экспериментальные исследования резьбонакатного автомата модели А2522 с ролик-сегментом // Кузнечно-пггамповочное производство. 1974. — № 5. — С. 27−29.
- Мирополъский Ю.А., Насонов, А Н. Технология и оборудование для накатывания резьб и профилей // Кузнечно-прессовое машиностроение. Серия С.-III, М., НИИМАШ. — 1971. — 175 с:
- Журавлев А.З., Луговой Э. П. Контроль и прогнозирование точности резьбы, накатанной на автоматах // Кузнечно-пггамповочное производство. 1990. -№ 8.-С. 23−25.
- Журавлев А.З., Ефремова Е. А. Проблемы точности и качества резьбы, накатываемой на автоматах // Кузнечно-пггамповочное производство. 1998. — № 10.-С. 10−13.
- Андреев A M., Журавлев А. З., Луговой Э. П. Графоаналитический метод определения радиальных усилий накатки резьбы // Кузнечно-штамповочное производство. 1979. — № 11. — С.7−9.
- Журавлев А.З., Луговой Э.П, Илясов В. В. Определение усилий накатывания резьбы на автоматах с роликами и сегментами с учетом жесткости системы // Кузнечно-штамповочное производство. 1992. — № 4. — G.7−9.
- Якухин В.Г. Оптимальная технология изготовления резьб. М.: Машиностроение, 1985.- 184 с.
- Якухин В.Г., Ставров В. А. Изготовление резьбы: Справочник.- М.: Машиностроение, 1989 192 с.
- Биргер И.А., Иосилевич Г. Б. Резьбовые соединения. М.: Машиностроение, 1973.-256 с.
- Биргер И.А., Иосилевич Г. Б. Резьбовые и сварные соединения. М.: Машиностроение, 1990. — 364 с.
- Фрумин Ю.Л. Высокопроизводительный резьбообразующий инструмент. Изд. 2-е, перераб. и доп. М.: Машиностроение, 1977. 183 с.
- Apel Н. Gewindewalzen. Carl Hanser Verlag. Mflnchen, 1952.
- Naser W., Meichsner H. Technologie des Gewindewalzens. Leipzig Fachbuch-verlag, 1959.
- Montag G, Konig D. Kraft, Arbeit und Machinengrundzeit beim Gewindewalzen zwei RoUen im Einstechverfahren // Fertigungstechnik und Betrieb. 1965. — N 4. — S. 227−230.
- Forres T. The Cold Rolling of Spline Shafts // Australian Machinery and Production Engineering. October, 1966.
- Ямамото А., Акаси К, Есгшото И. Усилие накатывания и расчет межцентрового расстояния накатных роликов // Перевод ВИНИТИ № 52 847/5. Статья из журнала «Никой кикай гаккай ромбунсю». 1960. — № 166. — С. 813 -826.
- Jamamoto A. Investigations on thread rolling // Bulletin of the Tokyo Institute of Technology. 1959. — N 2. — Ser. B. — P. 27−34.
- Jamamoto A, Joshimoto /. Investigations on thread rolling // Bulletin of the Tokyo Institute of Technology. 1961. — N 40. — P. 141−145-
- Dallas D. B. Getting the most of thread rolling attachments // The Tool and Manufacturing engineer. 1966. — Apr. — P. 170−173.
- Губин А.П. Накатывание резьбы роликами. М.: Машгиз, 1947.
- Загурский В.И. Исследование процесса накатывания наружных резьб с продольной подачей: Автореф. канд. дисс. М., Институт машиноведения АН СССР, 1959.
- Загурский В.И. Прогрессивные способы обработки резьбы. М.: Машгиз, 1960.- 125 с.
- Загурский В.И. Автоматизированное производство резьбовых крепежных изделий. М.: Машгиз, 1962. — 121 с.
- Дейнеко В.Г. Новые способы непрерывного накатывания резьбы и других профилей. М.: Машгиз, 1961. — 159 с.
- Рыжов Э.В., Андрейчиков О. С., Стешков А. Е. Раскатывание резьб. М: Машиностроение, 1974 — 122 с.
- Ардеев Ж.А. Исследование процесса накатывания резьбы роликами // Вестник машиностроения. 1980. -№ 11. — С. 65−67.
- Грубое, А А., Комаров П. Н. Силы при накатывании резьб // Станки и инструмент. 1981. — № 1. — С.19−21.
- Усов В.П. Кинематика пластического течения металла при деформировании резьбового профиля. // Кузнечно-пггамповочное производство. 1977. — № 9. -С.16.
- Хостиков М.З. Исследование силовых зависимостей процесса накатывания резьб тангенциальными головками // Прогрессивный режущий инструмент. Высокопроизводительное резание. М. — 1978. — С. 48−70.
- Симонов JI.Р. Стойкость резьбонакатных головок // Вестник машиностроения. 1986. -№ 10. — С. 62−63.
- Таурит Г. Э., Пуховский Е. С., Добрянский С. С. Прогрессивные процессы резьбоформирования Киев: Техшка, 1975.- С. 240.
- Мокринский В.И., Железков О. С. Новые прогрессивные виды и технологические процессы изготовления крепежных изделий // Сер. Метизное производство. Вып. 2. М: Ин-т Черметинформация, 1990. — С. 22
- Мокринский В.И., Железков О. С. Повышение прочности, точности и стойкости крепежных изделий // Черная металлургия: Бюл. Ин-та Черметинформация. 1987. -№ Ц. — С. 19−32.
- Паршин ВТ., Железков О. С., Савинкина О. В. Прогнозирование прочности холодновысаженных стержневых изделий из низкоуглеродистой стали // Изв. АН СССР. Металлы. -1990. № 4. — С. 158−161.
- Железков О.С. Исследование энергосиловых параметров процессов холодной высадки и точности стержневых крепежных изделий: Автореф. Дисс. на соиск. уч. ст. канд. техн. наук.- Магнитогорск, 1979. 20 с.
- Железков О.С. Развитие теории и ресурсосберегающих технологий изготовления крепежных изделий на высокопроизводительном автоматическом оборудовании: Автореф. дисс. на соиск. уч. ст. докт. техн. наук. Магнитогорск, 1998.-37 с.
- Герасимова О.В. Закономерности упрочнения металла при накатывании резьбы на редуцированных стальных изделиях // Сталь. № 7. — 2000. — С. 5152.
- Арсенъев В.В. Состояние и основные направления развития метизного производства // Сталь. 2000, — № 1. — С. 58−60.
- Аршанский М.М., Кульков И. Б. Способы нестационарного резьбонакатыва-ния с радиальной подачей // Вестник машиностроения. 2003. — № 9. — С. 4853.
- Gorke М. Verschleiparm Gewinde furchen // Ind. Anz. 1995. -117. — № 35.
- Бушенин Д.В., Киричек А. В. Кульков И.Б. Сравнение твердости резьбовых профилей, полученных разными методами пластического деформирования // Вестник машиностроения. 1999. — № 10.
- Поперечно-кттовая прокатка / Г. В. Андреев, В. А. Клушин, Е. М. Макушок и др./ Под общ. ред. Е. М. Макушка. Минск: Наука и техника, 1974. — 160 с.
- Механические свойства сталей и сплавов при пластическом деформировании / Третьяков А. В., Трофимов Т. К., Гурьянова М. К. М.: Машиностроение, 1971.-64 с.
- Смирнов-Аляев Г. А., Розенберг В. М. Теория пластических деформаций металлов. М.: Машгиз, 1956. — 368 с.
- Никифоров А.Д. Точность и технология изготовления метрических резьб. -М.: Высшая школа, 1963. 180 с
- Гжиров Р.И. Краткий справочник конструктора: Справочник. JI.: Машиностроение, Ленингр. отд-ние, 1983. — 464 с.
- ГОСТ 16 093–81.Основные нормы взаимозаменяемости. Резьба метрическая. Допуски. Посадки с зазором.
- ГОСТ 9150–81. Основные нормы взаимозаменяемости. Резьба метрическая. Профиль.
- ГОСТ 8724–81. Основные нормы взаимозаменяемости. Резьба метрическая. Диаметры и шаги.
- ГОСТ 24 705–81. Основные нормы взаимозаменяемости. Резьба метрическая. Основные размеры.
- Теория обработки металлов давлением / И .Я. Тарновский, А. А. Поздеев, О. А. Ганаго и др. М.: Металлургиздат, 1963. — 672 с.
- Качанов Л.М. Основы теории пластичности. М.: 1969. — 420 с.
- Соколовский В В. Теория пластичности. М.: Высшая школа, 1969. — 608 с.
- Гун Г. Я. Теоретические основы обработки металлов давлением: Теория пластичности.- М.: Металлургия, 1980. 456 с.
- Громов ЕЛ. Теория обработки металлов давлением. М.: Металлургия, 1978.-360 с.
- Кроха В.А. Упрочнение металлов при холодной пластической деформации: Справочник. -М.: Машиностроение, 1980. 157 с.
- ТурчакЛ.И. Основы численных методов: Учебн. пособие. М.: Наука, 1987. -320 с.65- Третьяков А. В., Зюзин В. И. Механические свойства сталей и сплавов при обработке давлением. М: Металлургия, 1973. — 224 с.
- ЛагранжЖ.Л. Аналитическая механика. Т.1 M.-JL: ГТТИ, 1950. — 594 с.
- Ritz W. Uber eine neue Methode zur Losung gewisser Variationsprobleme der mathematischen Physik, J. f. d. reine und angewandte Math. 135, H. 1 (1908)
- Ritz W. Theorie der Transwersalschwingungen einer quadratischen Platte mit freien Randern, Gesammelte Werke. Paris, 1911.
- Краснов М.Л., Макаренко Г. И., Киселев A.M. Вариационное исчисление. -М: Наука, 1973. 192 с.
- Михлин С.Г. Вариационные методы в математической физике. Изд. 2-е, переработ. и доп. М.: Наука, 1970. — 512 с.
- Губкин С И. Пластическая деформация металлов. М.: Металлургиздат, 1960. — Т. I — Ш.
- Смирнов-Аляев /".^. Сопротивление материалов пластическому деформированию. 3-е изд., перераб. и доп. JL: Машиностроение, Ленингр. отд-ние, 1978.-368 с.
- Ильюшин А.А. Механика сплошной среды. М.: Изд. МГУ, 1978. — 288 с.
- УнксовЕ.П. Инженерная теория пластичности. М.: Машгиз, 1959.-251 с.
- Унксов Е.П. Инженерные методы расчета усилий при обработке металлов давлением. М: Машгиз, 1939. — 191 с.
- Ун/ccoe Я. Я. Пластическая деформация при ковке и штамповке. М.: Машгиз, 1939 -191 с.
- Тарновский И.Я., Поздеев А. А., Ганаго О. А. Деформации и усилия при обработке металлов давлением. М.: Машгиз, 1959. — 304 с.
- Мейз Дж. Теория и задачи механики сплошных сред. М.: Мир, 1974. -319с.
- Хилл Р. Математическая теория пластичности.- М.: Гостехиздат, 1956.-462с.
- Томленое АД. Теория пластического деформирования металлов. М.: Металлургия, 1972. — 408 с.
- Колмогоров.B.J1. Механика обработки металлов давлением.- М.: Металлургия, 1986.-688 с.
- Седов Л.И. Механика сплошной среды. Т.1. М.: Наука, 1983. — 528 с.
- Джонсон У., Меллор П. Теория пластичности для инженеров.- М.: Машиностроение, 1979. -568 с.
- Е. Orowan. The Calculation of Roll Pressure in Hot and Cold Flat Rolling -Proc. Inst. Mech. Engr. v. 150,4. — 1943.
- McuiUHWi H.H. Прикладная теория пластичности и ползучести. М.: Машиностроение, 1979.400 с.
- Сторожев М.В., Попов Е. А. Теория обработки металлов давлением. М.: Машиностроение, 1977. — 424 с.
- Соколов Л.Д. Сопротивление металлов пластической деформации. М., Ме-таллургиздат, 1963. 284 с.
- Томсен Э., Янг К., Кабояши Ш. Механика пластических деформаций при обработке металлов. М.: Машиностроение, 1969. — 503 с.
- Соколовский В.В. Построение полей напряжений и скоростей в задачах пластического течения // Инженерный журнал. Вып.З. 1961.
- Underwood L.R. The Rolling of Metals. Sheet Met. Ind., 1945.
- Рейнер M. Деформация и течение. Введение в реологию. (Пер. с англ.). -М., Изд-во иностр. лит., 1963. 381 с.
- Марков А.А. О вариационных методах в теории пластичности // Известия АН СССР. Сер. Прикладная математика и механика, 1947, вып. 3, т. 11, с. 339−350.
- Тарновский И.Я. Вариационные методы механики пластических сред в теории обработки металлов давлением // Инженерные методы расчета технологических процессов обработки металлов давлением. М. — 1963. — С. 45−72.
- Колмогоров В.Л., Тарновский И. Я., Ериклинцев В. В. Новый метод расчета напряжений в обработке металлов давлением // Изв. вузов. Черная металлургия. 1964.-№ 9.-С. 74−92.
- Расчет напряженного состояния при прокатке вариационными методами / И. Я. Тарновский, В. Л. Колмогоров, Э. Р. Римм и др. // Изв. вузов. Черная металлургия. 1964. — № 12. — С. 78−80.
- Тарновский И.Я., Паршин В. Г. Исследование холодной деформации тел с неоднородными механическими свойствами // Изв. вузов. Черная металлургия. 1968.-№ 5. — С. 81−86.
- Ериклинцев В.В., Тарновский И. Я., Колмогоров В. Л. Определение напряжений при осадке высокой полосы с внешними зонами в условиях объемной деформации // Изв. вузов. Черная металлургия. 1967. — № 1. — С. 92−97.
- Тарновский И.Я., Поздеев А. А., Тарновский В. И. Вариационные методы в теории обработки металлов давлением // Прочность и пластичность. М. -1971.-С. 175−178.
- Тимошекнко С.П., ГулъдерД. Теория упругости (Пер. с англ.). М.: Наука, 1975. — 576 с.
- Мясищев АЛ, Ренне И. П., Смарагдов И. А. Аналитическое решение задачи образования выступов при вдавливании острых симметричных клиньев // Обработка металлов давлением: Сб. науч. тр. Вып.8. Свердловск: Изд. УПИ, — 1981. -С23−31.
- Демидович Б.П., Марон И. А. Основы вычислительной математики. М.: Наука, 1966. — 664 с.
- Снеговский Ф. П. Малыгин Б.В. Теория и практика магнито-импульсного упрочнения инструмента и деталей машин // Резание и инструмент. Респ. межвед. науч.-техн. сборник. 1989. — № 41. — с. 18−23.
- Контроль качества инструментальных материалов / А. А. Кондратюк, В. П. Нестеренко, В. Д. Руднев и др. // Современные технологии и материаловедение: Сб. науч. тр./ Под ред. Ю. А. Баландина. Магнитогорск: МГТУ, 2003. -С. 118−119.
- Повышение стойкости инструмента для формирования резьб крепежных изделий / О. С. Железков, А. А. Старушко, С. В. Кочуков и др. // Современные технологии и материаловедение: Сб. науч. тр./ Под ред. Ю. А. Баландина. -Магнитогорск: МГТУ, 2003. С. 102−106.
- Железное ОС., Старушко А. А., Кочуков С. В. Перспективные способы повышения стойкости резьбообразующего инструмента // Труды пятого конгресса прокатчиков. М.: Черметинформация, 2004. — С. 443−444.
- Norrie D.H., de Vries G. The Finite Element Method Fundamentals and Applications. — Academic Press, New York, 1973.
- Крагельский KB. Muxuh Н.М. Узлы трения машин: Справочник М.: Машиностроение, 1984. — 280 с.
- Жиркин Ю.В. Надежность, эксплуатация и ремонт металлургических машин: Учебник. Магнитогорск: МГТУ, 2002. — 230 с.
- Трение, износ и смазка (трибология и триботехника) / А. В. Чичинадзе, Э. М. Берлинер, Э. Д. Браун и др.- Под общ. ред. А. В. Чичинадзе. М.: Машиностроение, 2003. — 576 е.- ил.
- Пат. на п.м. 39 101 РФ, МПК7 В 21 Н 3/06. Инструмент для накатывания наружной резьбы / О С. Железков, С. В. Кочуков, С. О. Железков (РФ) — заявл. 09.03.2004- опубл. 20.07.2004: Бюл. № 20.
- Ланской Е.Н. Характеристика точностных параметров кузнечно-прессового оборудования // Вестник машиностроения. 1965. — № 12. — С. 51−56.
- Ланской Е.Н. Общий метод анализа жесткости прессов для объемной штамповки // Кузнечно-нггамповочное производство. 1969. — № 5. — С. 2932.
- ГОСТ 809–71. Шурупы путевые.
- Журавлев В.Н., Николаева О. И. Машиностроительные стали: Справочник. -Изд. 4-е, переработ, и доп. М.: Машиностроение, 1992: — 480 с.