Применение АВС-анализа при управлении логистическим процессом на складе
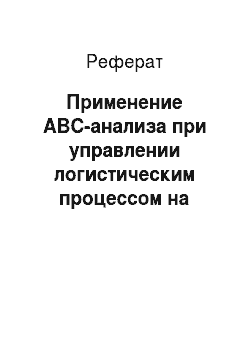
На четвертом этапе проводится оценка разных вариантов, после чего делается выбор наиболее рационального варианта размещения товаров. В вариантах размещения, учитывающих условие модернизации склада и объединенных во второй блок, появляются пустые места: для трехмерного оптимизированного размещения товаров на складе с учетом матрицы расстояний (распределение по принципу «чет-нечет») при… Читать ещё >
Применение АВС-анализа при управлении логистическим процессом на складе (реферат, курсовая, диплом, контрольная)
Рассмотрим применение метода ABC-анализа, о котором шла речь в гл. 6, к решению задачи оптимального размещения товаров на складе с учетом одно-, двухи трехмерного расположения грузовых единиц. В качестве параметра ранжирования товаров на группы А, В, С будет использоваться количество требований (заказов) на конкретные товары. Последовательность действий проиллюстрируем примером.
Па первом, подготовительном, этапе следует собрать необходимые данные:
- • пространственные размеры склада;
- • габаритные размеры мест хранения, длина, ширина проезда (прохода) между стеллажами;
- • габаритные размеры грузовых мест;
- • ассортимент и количество товаров, размещенных на складе;
- • существующее размещение товаров в ячейках склада (для последующего перепроектирования размещения товаров);
- • другие сведения, влияющие на решение о размещении товаров.
В качестве примера рассмотрим склад, имеющий площадь 1250 м² (25×50 м) и высоту 12 м. Ассортимент склада включает в себя 100 позиций. Предположим, что товары размещены в случайном порядке[2]. Товары сформированы в грузовые единицы — поддоны стандартного размера (1000×1200 мм) и отпускаются целыми грузовыми единицами (пакетами). Склад полностью механизирован.
Допустим, что размер одного места хранения (длина х ширина х высота) составляет 1,4×1,1×1,5 м, а расстояния проходов и проездов: а = 4 м, Ь = 6 м. Тогда упрощенная схема склада будет выглядеть так, как это представлено на рис. 7.3, где цифрами обозначено количество заказов по определенной позиции за период.
На втором этапе необходимо составить матрицу минимальных расстояний до 1-го места хранения, которая может быть получена с помощью: а) математических вычислений с учетом размеров проездов, проходов, мест хранения, а также размеров самого склада; б) некоторого измерительного прибора.

Рис. 7.3. Первоначальное (случайное) размещение товаров на складе.
Также на этом этапе следует определить критерий, по которому будет осуществляться выбор наилучшего варианта размещения товаров.
В нашем примере мы в качестве критерия выбора варианта будем использовать суммарный пробег автопогрузчиков, считая, что пробег — это фактор, влияющий на уровень затрат на эксплуатацию техники и, соответственно, общих затрат па складе.
Третий этап проведения АВС-анализа с целью определения мест размещения товаров на хранение — основной. Па данном этане выполняется расчет по различным вариантам размещения. Эти варианты условно можно объединить в три блока.
Блок 1.
Этот блок формируют варианты размещения товаров, не предусматривающие модернизации склада.
- 1.1. Частично оптимизированное размещение товарных позиций на складе только для группы Л, предложенное в работе, из которой были взяты исходные данные1.
- 1.2. Двумерное оптимизированное размещение товарных позиций на складе без учета матрицы расстояний. Группировка товарных позиций выполнена на основе АВС-анализа эмпирическим методом2, при этом не учтены расстояния от входа до г'-го места хранения.
- 1.3. Двумерное оптимизированное размещение товарных позиций на складе с учетом матрицы расстояний. Здесь могут быть рассмотрены два варианта размещения товаров: распределение «чет-нечет» и распределение «по часовой стрелке» .
Размещение товарных позиций по принципу «чет-нечет» с учетом матрицы расстояний предлагается выполнить следующим образом. Расстояния, которые проезжает автопогрузчик, необходимо проранжировать по возрастанию, причем если в матрице расстояний встречаются одинаковые расстояния, то сначала нумеруется расстояние, расположенное на схеме склада справа от выхода (участка отгрузки), а затем симметричное ему расстояние относительно центрального проезда.
Вариант распределения «по часовой стрелке» с учетом матрицы расстояний аналогичен предыдущему, отличие состоит в нумерации расстояний относительно выхода (участка отгрузки) — они нумеруются по часовой стрелке по мере увеличения.
Поскольку в предлагаемых вариантах рассматриваются одни и те же расстояния, то выбор варианта распределения не оказывает существенного влияния на конечный результат. Отличие вариантов состоит в способе учета и ранжирования расстояний. Для выполнения дальнейших расчетов остановимся на варианте распределения «чет-нечет». Упрощенная схема склада при двумерном оптимизированном размещении товарных позиций с учетом матрицы расстояний представлена на рис. 7.4.
Результаты вычислений для вариантов первого блока можно представить в виде табл. 7.3, из которой видно, что суммарный пробег техники при последнем варианте расположения товаров на складе существенно сократится (на 45%).

Рис. 7.4. Двумерное оптимизированное размещение товаров на складе с учетом матрицы расстояний, выполненное по принципу «чет-нечет» .
Таблица 7.3. Сравнение вариантов по блоку 1
Вариант расположения товаров на складе | Общий пробег техники, м | Уменьшение пробега, % | |
Случайное. | 272 685.4. | ||
Частично оптимизированное. | 173 756.6. | 36*. | |
Двумерное оптимизированное без учета матрицы расстояний. | 159 912,4. | ||
Двумерное оптимизированное с учетом матрицы расстояний (распределение «чет-нечет»). | 151 128,6. |
Расчет производился, но формуле (272 685.4 — 173 756.6)/272 685,4−100 = 36%. Таким образом, все варианты сравнивались со случайным расположением товаров.
Блок 2.
Рассмотрим тот же склад, но предусмотрим условие стеллажного складирования в два и пять ярусов. Фактически это означает, что вместимость склада возрастает в два раза при двухъярусном расположении, в пять раз — при пятиярусном. Второй блок формируют следующие варианты.
- 2.1. Трехмерное оптимизированное размещение товаров на складе с учетом матрицы расстояний и высоты при расположении паллетов на двухъярусном стеллаже. Такой вариант размещения товаров должен производиться следующим образом: паллеты с наибольшим средним количеством заказов находятся на нижней полке (ярусе), а паллеты с наименьшим средним количеством заказов — на верхней. Упрощенная схема склада при таком расположении паллетов представлена на рис. 7.5. На данном рисунке числа обозначают номер стека, в котором два яруса. Например, цифра 1 -это первое отделение стеллажа, в котором два яруса. Очевидно, что увеличение количества ячеек приводит к перераспределению товара ближе к зоне отгрузке и часть ячеек освобождается.
- 2.2. Трехмерное оптимизированное размещение товарных позиций на складе с учетом матрицы расстояний и высоты при расположении паллетов

Рис. 7.5. Трехмерное оптимизированное размещение товаров с учетом матрицы расстояний по принципу «чет-нечет» и при двухъярусном расположении паллетов.
на пятиярусном стеллаже. При этом варианте размещения учитывается следующее: паллеты с наибольшим средним количеством заказов должны находиться на нижней полке, а паллеты с наименьшим средним количеством заказов — на верхней. Схема, соответствующая данному варианту, приведена на рис. 7.6.
2.3. Вариант, когда часть груза хранится не на паллетах, а в ящиках, что приводит к появлению свободного места в ячейках. Однако этого можно избежать, разместив несколько видов груза в одной ячейке при условии, что груз нельзя делить на разные ячейки, а также невозможно разместить одновременно паллет и ящики в одной ячейке.
Из-за достаточно большого объема расчетов и пояснений этот вариант подробно не рассматривается.

Рис. 7.6. Трехмерное оптимизированное размещение товаров с учетом матрицы расстояний по принципу «чет-нечет» и при расположении паллетов на пятиярусном стеллаже.
Результаты моделирования по второму блоку можно представить в виде табл. 7.4, из которой видно, что суммарный пробег техники при последнем варианте расположения товаров на складе существенно сократится (на 45%).
Таблица 7.4. Сравнение вариантов по блоку 2
Вариант расположения товаров на складе | Общий пробег техники, м | Уменьшение пробега, % |
Случайное, скорректированное с учетом наличия стеллажей. | 185 820,0. | —. |
Трехмерное оптимизированное размещение товарных позиций на складе с учетом матрицы расстояний (распределение «чет-нечет») при двухъярусном расположении паллетов. | 116 490,8. | |
Трехмерное оптимизированное размещение товарных позиций па складе с учетом матрицы расстояний (распределение «чет-нечет») при расположении паллетов на пятиярусном стеллаже. | 88 386,4. | |
Трехмерное оптимизированное размещение товарных позиций на складе с учетом матрицы расстояний при расположении паллетов на пятиярусном стеллаже с условием размещения в одной ячейке нескольких товаров. | 82 992.0. |
Блок 3.
В третий блок должны входить варианты, учитывающие капитальные вложения в модернизацию склада и другие дополнительные затраты. Расчеты по нашему примеру здесь не приводятся.
На четвертом этапе проводится оценка разных вариантов, после чего делается выбор наиболее рационального варианта размещения товаров. В вариантах размещения, учитывающих условие модернизации склада и объединенных во второй блок, появляются пустые места: для трехмерного оптимизированного размещения товаров на складе с учетом матрицы расстояний (распределение по принципу «чет-нечет») при двухъярусном расположении паллетов — на 50%; для трехмерного оптимизированного размещения товаров с учетом матрицы расстояний (распределение «чет-нечет») при расположении паллетов на пятиярусном стеллаже — на 80%; для трехмерного оптимизированного размещения товарных позиций на складе с учетом матрицы расстояний при расположении паллетов на пятиярусном стеллаже с условием размещения в одной ячейке нескольких товаров — на 82%. Эти освободившиеся зоны можно использовать под размещение других товаров или сдать в аренду, что будет приносить дополнительный доход. Однако при этом необходимы капитальные вложения на сооружение стеллажей.
Следует отметить, что мы рассматривали только один критерий сравнения вариантов, соответствующий снижению суммарного пробега автопогрузчиков. В действительности переход к и-ярусному хранению — это более сложная задача, в которой следует учитывать временные затраты, связанные с обслуживанием потребителей, энергетические затраты на операции «подъема/опускания» груза и другие составляющие затрат. Кроме того, необходима оценка экономической целесообразности внедрения проекта, предполагающая расчет размера капитальных вложений, срока окупаемости, доходности инвестиций и др. Таким образом, каждому предприятию необходимо самостоятельно решить, на каком варианте ему следует остановиться исходя из своих собственных возможностей и задач. Нужно заметить, что даже без модернизации, а только лишь при рациональном размещении товаров на складе наблюдается значительная экономия.