Исследование и разработка технологических процессов изготовления деталей с учетом взаимного влияния формируемых показателей качества
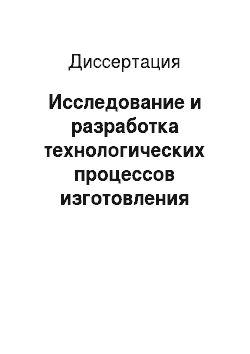
Предложена модель процесса формирования показателей качества, структура которой построена на основе функциональных связей между показателями качества в процессе изготовления валка ТЭС. Выявленные в ходе исследований факты наследования и взаимного влияния показателей качества позволили разработать структурную модель процесса формирования показателей качества, которая дает возможность наглядно… Читать ещё >
Содержание
- Глава 1. Технологическое обеспечение качества деталей
- 1. 1. Способы технологического обеспечения заданных показателей качества
- 1. 2. Моделирование и автоматизация проектирования техноЛогических процессов
- 1. 3. Выводы по главе 1
- 1. 4. Цель и задачи исследования
- Глава 2. Направленное формирование показателей качества
- 2. 1. Общие принципы направленного формирования показателей качества
- 2. 2. Разработка структурной модели процесса формирования показателей качества
- 2. 3. Выводы по главе 2
- Глава 3. Разработка математической модели процесса формирования показателей качества
- 3. 1. Определение сил резания при чистовом точении фасонного профиля
- 3. 2. Определение отклонений реального профиля рабочей поверхности валка от теоретического, вызванных упругими отжатиями элементов технологической системы
- 3. 3. Определение отклонений от круглости поперечного сечения валка, вызванных перемещениями инструмента относительно заготовки
- 3. 3. 1. Отклонения от круглости, возникающие при точении
- 3. 3. 2. Отклонения от круглости, возникающие при алмазном выглаживании
- 3. 4. Определение показателей шероховатости наружной поверхности валка
- 3. 5. Определение показателей напряженно-деформированного 72 состояния поверхностного слоя
- 3. 6. Взаимное влияние шероховатости и микротвердости обрабатываемой заготовки
- 3. 7. Выводы по главе 3
- Глава 4. Экспериментальные исследования по определению влияния исходной микротвердости на шероховатость обработанной поверхности
- 4. 1. Задачи и методика проведения экспериментов
- 4. 2. Влияние исходной микротвердости на шероховатость, получаемую после точения
- 4. 3. Влияние исходной микротвердости на шероховатость, получаемую после алмазного выглаживания
- 4. 4. Измерение отклонений фасонного профиля в поперечном сечении
- 4. 5. Выводы по главе 4
- Глава 5. Моделирование технологического процесса с учетом взаимного влияния формируемых показателей качества. 108 '
- 5. 1. Разработка компьютерной модели процесса формирования показателей качества
- 5. 2. Методика разработки технологического процесса с учетом взаимного влияния формируемых показателей качества
- 5. 3. Выводы по главе 5
Исследование и разработка технологических процессов изготовления деталей с учетом взаимного влияния формируемых показателей качества (реферат, курсовая, диплом, контрольная)
Комплексный подход к технологическому обеспечению работоспособности деталей основан, с одной стороны, на оценке показателей качества деталей (характеризующих их геометрическую форму, качество поверхностного слоя и объемные свойства) в зависимости от технологических факторов и, с другрй стороны, на прогнозировании эксплуатационных свойств (износостойкости, контактной жесткости, коррозионной стойкости и пр.) деталей в зависимости от их показателей качества.
Если рассматривать множества эксплуатационных свойств и показателей качества детали, очевидно, что отдельным элементам множества свойств соответствуют подмножества показателей, которые в общем случае пересекаются. Таким образом, определенные изолированные показатели качества не могут гарантировать необходимые эксплуатационные свойства детали в целом, необходимо обеспечить некоторую совокупность взаимосвязанных показателей.
Для обеспечения качества прецизионных деталей (имеющих допуски показателей в несколько микрометров или долей микрометров) необходимо учитывать две составляющие погрешностей показателей: первая характерна непосредственно для процесса обработки, вторая имеет наследственную природу, т. е. определяется предшествующими процессами. Вторая составляющая устойчива и с трудом поддается как ликвидации, так и уменьшению. Если при изготовлении деталей нормальной точности наследственная составляющая представляет собой весьма малую часть допуска показателя, то при изготовлении прецизионных деталей она составляет его основную часть, а в некоторых случаях и превосходит допуск.
Кроме того, следует учитывать взаимное влияние показателей качества, т. е. изменения одного показателя в зависимости от другого и изменения второго показателя в зависимости от первого, проявляющиеся в одном и том же переходе. В настоящее время этому явлению уделяется мало внимания, хотя признано, что такое влияние, может существенно сказаться на получаемых значениях показателей качества, особенно при изготовлении прецизионных деталей.
Особую сложность представляет изготовление различных деталей типа тел вращения, исполнительные поверхности которых ограничены сложным фасонным профилем (рис. 1), поскольку в данном случае составляющие силы резания, параметры режима обработки, а, следовательно, и величины показателей качества могут меняться вдоль профиля. К числу подобных деталей относятся формовочные валки трубоэлектросварочных и прокатных становподающие и калибровочные валки правильных становвалки рольгангов и транспортеров для перемещения фасонных деталейбегунки колесных, гусеничных, подъемно-транспортных машинпуансоны, матрицы штампов и прессформ и др. Фасонные поверхности деталей типа тел вращения могут работать как в паре с ответными фасонными поверхностями, так и практически с любыми другими поверхностями, например плоскостями, цилиндрами, торами и пр.
В настоящей работе в качестве представителей рассматриваемой группы деталей выбраны формовочные валки трубоэлектросварочных станов (ТЭС) (рис. 1, а — в). Такой выбор оправдан тем, что формовочные валки, обладая всеми присущими данной группе деталей элементами, отличаются жесткими техническими требованиями [1], в частности: диаметральные размеры сопрягаемых поверхностей и линейные размеры валков выполняют по 7 квалитету точности ISOотклонение реального профиля от теоретического не должно превышать 0,01 ммшероховатость исполнительных поверхностей должна быть в пределах Ra 0,4. 1,6 мкм.
При эксплуатации валок подвергается различным видам изнашивания и знакопеременным нагрузкам. Наиболее важными эксплуатационными свойствами валка ТЭС являются износостойкость, контактная жесткость, усталостная прочность, коррозионная стойкость. Основное внимание следует уделить качеству рабочей поверхности валка, от которого зависят.
6П+П о?
30±0,01.
R20.
Ra 1,6 2 фаски а).
Г) б).
В).
0,05.
V У У т 2- щ / / / /.
Y//A /////J 1 [N ж.
Ra 0,05.
Д).
Рис. 1. Примеры деталей типа тел вращения, имеющих фасонную поверхность: аX б), в)-формовочные валкиг) — пуансонд) — матрица штампа о производительность ТЭС и качество продукции. Перечисленные выше эксплуатационные свойства существенно зависят от таких показателей качества поверхности, как шероховатость, микротвердость (твердость поверхностного слоя), остаточные напряжения, глубина и степень упрочнения.
Показатели качества рабочей поверхности валка формируются, в основном, на заключительной стадии процесса изготовления валка, включающей чистовое точение и алмазное выглаживание фасонного профиля. Это связано с тем, что в технологическом процессе предусмотрена объемная закалка, которая вызывает существенные деформации заготовки, что предопределяет весьма большие (до 2 мм) припуски на чистовую обработку профиля. Именно заключительная стадия изготовления валка детально исследована в данной работе.
Предусмотреть формирование необходимых значений показателей качества целесообразно уже на этапе технологической подготовки производства. Принципы направленного формирования показателей качества деталей нацелены на то, чтобы при заданных значениях показателей качества готовой детали, известном диапазоне значений показателей качества исходной заготовки с учетом информации об их трансформации, технологическом наследовании (переносе) и взаимном влиянии в процессе обработки разработать эффективный технологический процесс и обеспечить получение требуемых показателей качества.
Объектом исследования в данной работе является процесс формирования проектных технологических решений уровня маршрутно-операционной технологии изготовления деталей.
Предложена модель процесса формирования показателей качества, структура которой построена на основе функциональных связей между показателями качества в процессе изготовления валка ТЭС. Выявленные в ходе исследований факты наследования и взаимного влияния показателей качества позволили разработать структурную модель процесса формирования показателей качества, которая дает возможность наглядно представлять причинно-следственные связи при формировании показателей качества в процессе обработки деталей в виде графа, а также прослеживать наследование и взаимное влияние показателей качества по ходу технологического процесса изготовления детали.
Математическое описание коэффициентов трансформации и его компьютерная реализация позволяют анализировать механизмы формирования показателей качества, оценивать влияние изменения отдельного показателя качества на комплекс показателей в целом, определять параметры, посредством изменения которых целесообразно управлять значениями показателейкачества. В результате моделирования можно, задаваяпараметры технологической системы, в частности параметры режимов обработки, рассчитывать величины показателей качества детали на определенных этапах обработки, а также определять такие диапазоны значений параметров, которые обеспечивают необходимые значения показателей качества детали.
Такое трехуровневое моделирование, включающее разработку структурной, математической и компьютерной моделей, хорошо встраивается в методику разработки технологического процесса для изготовления прецизионных деталей, способствуя более точному прогнозированию получаемых показателей качества и проектированию эффективный технологического процесса.
Теоретические исследования в работе базировались на научных основах технологии машиностроения, в частности, теоретических положениях направленного формирования показателей качества, а также на теории системного анализа. Математическая модель построена с использованием геометрических зависимостей, аналитических зависимостей теорий сопротивления материалов, теоретической механики и регрессионных зависимостей, полученных в ходе экспериментальных исследований. Прикладное программное обеспечение компьютерной модели разработано в программном комплексе «Моделирование в технических устройствах» («МВТУ»).
Научная новизна работы заключается в выявлении закономерностей формирования показателей качества поверхностного слоя детали при алмазном выглаживании с учетом взаимного влияния формируемых показателей.
Практическую ценность работы определяют:
1) пакет программ, позволяющий для деталей типа тел вращения, имеющих фасонную поверхность, вычислять, с одной стороны, показатели качества при заданных параметрах технологической системы, с другой стороны, параметры технологической системы, обеспечивающие требуемые показатели качества;
2) методика проектирования технологического процесса с учетом взаимного влияния формируемых показателей качества, которая включает в себя трехуровневое моделирование процесса формирования показателей качества, подразумевающее разработку структурной, математической и компьютерной моделей процесса.
На защиту выносятся:
1) результаты экспериментальных исследований по определению влияния исходной микротвердости на шероховатость, получаемую после точения и алмазного выглаживания заготовок;
2) структурная, математическая и компьютерная модели процесса формирования показателей качества для деталей типа тел вращения, имеющих фасонную поверхность.
Полученная в результате работы методика разработки технологических процессов с учетом взаимного влияния формируемых показателей качества принята к внедрению на ОАО «НПО «Сатурн», что подтверждено соответствующим актом.
Общие выводы.
1. Предложена методика проектирования технологического процесса с учетом взаимного влияния формируемых показателей качества, включающая трехуровневое моделирование процесса формирования показателей качества, подразумевающее разработку структурной, математической и компьютерной моделей.
2. Причинно-следственные связи при формировании показателей качества могут быть определены с помощью структурной модели процесса формирования показателей качества детали, представленной в виде графа, обеспечивающей возможность мониторинга наследования и взаимного влияния показателей качества по ходу технологического процесса изготовления детали.
3. Предложено представлять коэффициенты трансформации показателей качества не постоянными величинами, а математическими зависимостям. Это позволит определять параметры, регулирующие величину показателей.
4. Разработана математическая модель процесса формирования показателей качества деталей типа тел вращения, имеющих фасонную поверхность, дающая возможность анализировать механизмы формирования отдельных показателей качества и комплекса показателей в целомвыявлять параметры, посредством изменения которых целесообразно управлять значениями показателей качества.
5. Экспериментально получены зависимости, описывающие взаимосвязь высотных параметров шероховатости с исходной микротвердостью заготовки и параметрами режимов обработки для процессов точения и алмазного выглаживания, позволяющие точнее спрогнозировать значения данных показателей после обработки заготовки. При этом определено, что степень влияния исходной микротвердости на высотные параметры шероховатости при алмазном выглаживании в 2 раза больше, чем при точении.
6. Установлен факт взаимного влияния шероховатости и микротвердости при алмазном выглаживании, учет которого позволяет повысить достоверность прогнозирования значений высотных параметров шероховатости не менее чем на 10. .15%.
7. Расчет показателей качества при обработке деталей типа тел вращения, имеющих фасонную поверхность, может быть выполнен с помощью разработанной компьютерной модели и пакета программ.
8. Компьютерная модель позволяет задавать коэффициенты трансформации показателей качества оригинальными математическими зависимостямирассчитывать величины показателей качества деталей на определенных этапах изготовления с учетом наследования и взаимного влияния показателей качества, задавая параметры технологической системы и режимов обработкиоценивать влияние изменения отдельного показателя качества на другие показатели и на комплекс показателей в целома также определять диапазоны значений параметров технологической системы, которые обеспечивают необходимые значения показателей качества детали.
Список литературы
- Технологические основы высокоэффективных методов обработки деталей: Учеб. пособие / П. И. Ящерицын, M.JI. Хейфец, Б. П. Чемисов и др. -Новополоцк: ПТУ, 1996. 136 с.
- Хейфец M.JI., Кожуро Jl.M., Мрочек Ж. А. Процессы самоорганизации при формировании поверхностей. Гомель: ИММС НАНБ, 1999. — 276 с.
- Базров А.А. Эмиссионная технологическая диагностика. Библиотека технолога. М.: Машиностроение, 2005. — 300 с.
- Рыжов Э.В. Контактная жесткость деталей машин. М.: Машиностроение, 1966.- 182 с.
- Рыжов Э.В., Суслов А. Г., Федоров В. П. Технологическое обеспечение эксплуатационных свойств деталей машин. М.: Машиностроение, 1979. -175 с.
- Суслов А.Г. Технологическое обеспечение параметров состояния поверхностного слоя деталей. — М.: Машиностроение, 1987. — 208 с.
- Рыжов Э.В., Колесников Ю. З., Суслов А. Г. Контактное взаимодействие деталей машин при статических и динамических нагрузках. — Киев: Наукова думка, 1983. 178 с.
- Суслов А.Г. Технологическое обеспечение и повышение качества деталей. Разработка новых методов обработки // Справочник. Инженерный журнал. -1998.-№ 9(18).- С. 9- 13.
- Безъязычный В.Ф. Расчет режима обработки, обеспечивающего комплекс параметров поверхностного слоя и точность обработки // Справочник. Инженерный журнал. 1998. — № 9. — С. 13−18.
- Безъязычный В.Ф. Влияние качества поверхностного слоя после механической обработки на эксплуатационные свойства деталей машин // Справочник. Инженерный журнал (Приложение) 2001. — № 4. — С. 9−16.
- Балакшин Б.С. Основы технологии машиностроения. — М.: Машиностроение, 1969. -358 с.
- Колесов ИМ. Основы технологии машиностроения: Учеб. для машиностроит. спец. вузов. -М.: Высшая школа, 1999. 591 с.
- Технологическая наследственность в машиностроительном производстве / A.M. Дальский, Б. М. Базров, А. С. Васильев и др.- Под ред. A.M. Дальского. М.: Изд-во МАИ, 2000. — 364 с.
- Кондаков А.И., Васильев А. С. Проектирование маршрутов изготовления деталей с учетом технологического наследования // Известия вузов. Машиностроение. 1998.-№ 10. -С. 31 -41.
- Базров Б.М. Расчет точности машин на ЭВМ. М.: Машиностроение, 1984. -256 с.
- Кондаков А.И., Васильев А. С. Системное моделирование взаимодействий в технологических средах // Известия вузов. Машиностроение. — 1998. — № 4−6.-С. 92−100.
- Васильев А.С. Статистическая модель трансформации свойств изделий в технологических средах // Вестник МГТУ. Машиностроение. 1997. — № 4 -С. 13−20.
- Васильев А.С. Определение количественных характеристик оперативной трансформации свойств изделий в технологических средах // Известия вузов. Машиностроение. 1999. — № 4. — С. 42 — 47.
- Направленное формирование свойств изделий машиностроения / А. С. Васильев, A.M. Дальский, Ю. М. Золотаревский, А.И. Кондаков- Под ред. А. И. Кондакова. М.: Машиностроение, 2005. — 325 с.
- Технологические основы управления качеством машин / А. С. Васильев, A.M. Дальский, С. А. Клименко и др. М.: Машиностроение, 2003. -256 с.
- Кондаков А.И. Векторная интерпретация технологических процессов и синтез их структур // Известия вузов. Машиностроение, 1987. — № 8.-С. 111−115.
- Кондаков А.И., Васильев А. С., Цыганов B.C. Эффективность взаимодействия технологических методов разной физической природы при направленном формировании качества деталей машин // Известия вузов. Машиностроение. 2002. — № 1. — С. 39 — 45.
- Цыганов B.C. Обеспечение качества изготовления деталей при взаимодействии технологических методов разной физической природы:
- Автореферат дис.. канд. техн. наук. М.: Изд-во МГТУ им. Н. Э. Баумана, 2007. — 16 с.
- Каширский Ю.В., Колосков М. М. Информационный банк по машиностроительным и энергетическим материалам // Сучасне машинобудування. 2000. — № 1 — 2 (3 — 4). — С. 81 — 87.
- Васильев А.С., Кондаков А. И. Выбор заготовок в машиностроении: Учеб. пособие. М.: Изд-во МГТУ им. Н. Э. Баумана, 2000. — 80 с.
- Патраков Н.Н. Моделирование и анализ технологических систем обеспечение качества ответственных деталей авиакосмической техники. -М.: Изд-во МАИ, 2003. 197 с.
- Марецкая В.В. Моделирование технологических процессов механической обработки с использованием программного комплекса «Моделирование В Технических Устройствах» («МВТУ») // Известия вузов. Машиностроение. 2004. — № 4. — С. 39 — 52.
- Дальский A.M. Технологическое обеспечение надежности высокоточных деталей машин. — М.: Машиностроение, 1975. — 223 с.
- Дальский A.M., Васильев А. С., Кондаков А. И. Технологическое наследование и направленное формирование эксплуатационных свойств изделий машиностроения // Известия вузов. Машиностроение. — 1996. — № 10−12.-С. 70−76.
- Дальский A.M. Аналитическое и графическое описания механизма технологического наследования // Вестник МГТУ. Машиностроение. -1996.-№ 3.-С. 29−35.
- Суслов А.Г., Дальский A.M. Научные основы технологии машиностроения. — М.: Машиностроение, 2002. 684 с.
- Ящерицын П.И., Рыжов Э. В., Аверченков В. И. Технологическая наследственность в машиностроении. — Минск: Наука и техника, 1977. -256 с.
- Камсюк М.С. Влияние частоты изменения некруглости центровых отверстий и наружной поверхности заготовки на точность обработки // Известия вузов. Машиностроение. 1975. — № 3. — С. 172- 175.
- Шарипов Б.У. Технологическая наследственность состояния поверхностного слоя обработанной детали // Оптимизация процессов резания жаро- и особопрочных материалов: Межвуз. тематич. науч. сб. — Уфа, 1989.-С. 119−122.
- Шарипов Б.У. Повышение эффективности процессов механообработки на основе аналитической оценки напряженного состояния рабочей зоны контакта инструмента и заготовки: Дис.. д-ра техн. наук. Уфа, 2000. — 455с.: ил.
- Постнов В.В., Шарипов Б. У., Шустер Л. Ш. Процессы на контактных поверхностях, износ режущего инструмента и свойства обработаннойповерхности: Учеб. пособие. — Свердловск: Изд-во Урал, ун-та, 1988. — 221 е.: ил.
- Эль-Занин Б. Х. Технологическое обеспечение эксплуатационных характеристик деталей машин при алмазном выглаживании: Дис.. канд. техн. наук 05.02.08. Самара, 1996. — 166 е.: ил.
- Суслов А.Г., Васильев А. С., Сухарев С. О. Влияние технологического наследования на качество поверхностного слоя деталей машин // Известия вузов. Машиностроение. 1999. — № 1. — С. 69 — 76.
- Папшев Д.Д. Отделочно-упрочняющая обработка поверхностным пластически деформированием. М.: Машиностроение, 1978 — 152 с.
- Камсюк М.С., Арсланов Ф. Х. О расчете сил при точении криволинейной режущей кромкой инструмента // Известия вузов. Машиностроение. -1985. -№ 11.-С. 116−199.
- Арсланов Ф.Х. Технологическое обеспечение качества изготовления сложнопрофильных валков трубоэлектросварочных станов: Дис.. канд. техн. наук 05.02.08. М., 1986. — 185 с.
- Технология машиностроения: Учеб. для вузов- В 2 т. М.: Изд-во МГТУ им. Н. Э. Баумана, 1997. — Т. 1. Основы технологии машиностроения / В. М. Бурцев, А. С. Васильев, A.M. Дальский и др.- Под ред. A.M. Дальского. — 564 с.
- Корсаков B.C. Точность механической обработки. — М.: Машгиз, 1961. — 380 с.
- Гемба И.Н. Приспособление для алмазного выглаживания профильных поверхностей // Опыт передовиков и новаторов производства: Экспрессинформация. ВНИИТЭМР. Серия 6. — 1987. — Вып. 10. -С. 9−10.
- А.С. 1 258 680 (СССР). МКИ В 24 В 39/04. Устройство для обработки поверхностей тел вращения криволинейного профиля / И. Н. Гемба, М. С. Камсюк, И. Е. Лазари и др.//Открытия. Изобретения. 1986. — № 35.-С. 69.
- Абакумов A.M., Видманов Ю. И., Михелькевич В. Н. Алгоритмизация процесса продольного точения // Станки и инструмент. — 1972. № 9. -С. 29−31.
- Беляков В. И., Горнев В. Ф. Математическая модель процесса продольного точения // Известия вузов. Машиностроение. 1980. — № 10. — С. 115 — 120.
- Кудинов В.А. Динамика станков. — М.: Машиностроение, 1967. 358 с.
- Гозман Я.Б., Пиковский Ю. Д. Исследование передаточной функции процесса резания как звена адаптивной системы // Станки и инструмент. — 1974.-№ 8- С. 90−92.
- Зориктуев В.Ц., Лютов А. Г. Дискретная динамическая модель процесса точения // Оптимизация процессов резания жаро- и особопрочных материалов: Межвуз. темат. науч. сб. Уфа, 1989. — С. 57 — 61.
- Чистяков Ю.П. Разработка математической модели оптимизации процесса чистового точения // Математическое обеспечение оптимизации операций механической обработки: Сб. науч. тр. / Ярославский политехнический институт. Ярославль, 1988 — С. 44 — 47.
- Кроль О.С. Использование программной среды MATLAB при моделировании процесса продольного точения //СТИН. 1995. — № 4.-С. 32−34.
- Эльясберг М.Е. Автоколебания металлорежущих станков. Теория и практика. СПб.: Изд-во ОКБС, 1993.- 180 с.
- Вейц B. JL, Максаров В. В., Лонцих П. А. Динамика и моделирование процессов резания при механической обработке. Иркутск: РИО ИГИУВа, 2000.- 189 с.
- Грановский Э.Г., Камсюк М. С. О динамике алмазного выглаживания //Известия вузов. Машиностроение. 1969. — № 4. — С. 132- 136.
- Грановский Э.Г., Камсюк М. С. О колебаниях инструмента в процессе алмазного выглаживания круглых цилиндрических поверхностей // Известия вузов. Машиностроение. 1969. — № 6. — С. 155 — 160.
- Камсюк М.С., Гемба И. Н. О динамике процесса алмазного выглаживания рычажными механизмами // Известия вузов. Машиностроение. 1988.-№ 4.-С. 139- 143.
- Сулима A.M., Шулов В. А., Ягодкин Ю. Д. Поверхностный слой и эксплуатационные свойства деталей машин. М.: Машиностроение, 1988.-240 с.
- Палей М. М'. Технология производства приспособлений пресс-форм и штампов. — М.: Машиностроение, Ленинградское отделение, 1982. 248 с.
- Шорин Ю.С. Технологическое обеспечение станков с ЧПУ. М.: Машиностроение, 1986. — 176 с.
- Васев В.А. Автоматизированный выбор режимов резания при заданной шероховатости криволинейных поверхностей, обрабатываемых на токарных станках с ЧПУ: Автореферат дис.. канд. техн. наук. -Свердловск, 1991. 16 с.
- Хворостухин Л. А., Гасилин В. И., Журавлев Д. А. О влиянии вибраций инструмента на чистоту поверхности при алмазном выглаживании // Известия вузов. Машиностроение. 1974. — № 3. — С. 149- 152.
- Конечнова С.В. Теоретическое исследование параметров шероховатости при точении в трехмерном" измерении // Качество поверхностного слоя и эксплуатацинные свойства деталей авиационных двигателей: Сб. науч. тр.
- Рыбинский авиационный институт- Ярославский политехнический институт. Ярославль, 1990. — С. 31 — 39.
- Заковоротный В.Д., Бордачев Е. В. Научные основы прогнозирования и диагностики качества обрабатываемой на металлорежущем станке детали // Диагностика и управление в технических системах: Межвуз. сб. науч. тр. Ростов н/Д, 1995. — С. 31 — 41.
- Смелянский В.М., Чоудхури Н. А. Расчетная модель формирования остаточных напряжений при ППД обкатыванием и выглаживанием // Повышение качества изготовления деталей и изделий в машиностроении: Материалы семинара. М., 1988. — С. 72 — 78.
- Блюменштейн В.Ю. Описание программы нагружения на стадии свободного ортогонального резания // Обработка металлов. 2001. — № 2. -С. 32−35.
- Мальсагов А.А. Моделирование технологических процессов выглаживания с учетом упругопластических свойств материала // Вестник машиностроения. 1999. — № 9. — С. 35 — 38.
- Хандожко А. В. Напряженно-деформированное состояние в поверхностном слое деталей при обработке резанием // Справочник. Инженерный журнал. (Приложение)-2001.-№ 10.-С. 13−16.
- Губанов В.Ф. Обеспечение заданных параметров шероховатости поверхности и микротвердости в процессе выглаживания цилиндрических деталей: Дис.. канд. техн. наук. — Тюмень, 2003. 160 с.
- Полетаев В.А. Методы обеспечения требуемого качества поверхностного слоя деталей машин: методическое пособие по выполнению курсовой работы. Электронный ресурс. Режим доступа: http.7/elib.ispu.ru/library/lessons/Poletaev, свободный
- Спиридонов А.А. Планирование эксперимента при исследовании технологических процессов. — М.: Машиностроение, 1981. — 184 с.
- Захарцев С.Н. Математическая статистика и планирование эксперимента в технологии машиностроения: Учеб. пособие. — М.: Изд-во МГТУ им. Н. Э. Баумана, 1991. Ч. 1. — 52 с.
- Захарцев С.Н. Математическая статистика и планирование эксперимента в технологии машиностроения: Учеб. пособие. М.: Изд-во МГТУ им. Н. Э. Баумана, 1992. -Ч. 2. — 32 с.
- Машиностроение. Энциклопедия / Ред. совет: К. В. Фролов (пред.) и др. Т. III-3: Технология изготовления деталей машин / A.M. Дальский, А. Г. Суслов, Ю. Ф. Назаров и др.- Под общ. ред. А. Г. Суслова. М.: Машиностроение, 2000. 840 с.
- Гемба И.Н. Разработка и исследование автоматизированного алмазного выглаживания фасонных тел вращения: Дис.. канд. техн. наук. М., 1991.-214с.
- Марецкая В.В. К вопросу автоматизации направленного формирования показателей качества деталей // Вестник компьютерных и информационных технологий. 2008. — № 3. — С. 29 — 34.