Усовершенствование технологии удаления водотопливных фракций из отработанного смазочного масла путём оптимизации процессов тепломассообмена
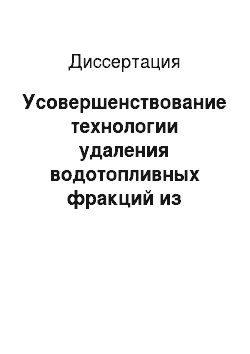
Разработанная модель процесса тепломассообмена и технология её реализации обеспечивает сокращение энергетических затрат на удаление ВТФ из ОСМ на 25% за счёт введения в ОСМ добавок воды от 15% до 40% и понижения температуры теплоносителя от 130 140 С до ЮО С. При увеличении процентного содержания воды более 40% в смеси с ОСМ исчезает экономическая эффективность добавки воды, так как… Читать ещё >
Содержание
- 1. Состояние вопроса и задачи исследований
- 1. 1. Старение, очистка и регенерация смазочных масел
- 1. 2. Способы удаления водотопливных фракций из смазочных масел
- 1. 2. 1. Анализ способов удаления водотопливных фракций
- 1. 2. 2. Плёночное испарение как способ удаления воды и топлива из отработанного смазочного масла
- 1. 3. Задачи исследования
- 2. Расчётно-теоретическое исследование процессов тепломассообмена при удалении водотопливных фракций из отработанных смазочных масел
- 2. 1. Обоснование необходимости усовершенствования процесса удаления водотопливных фракций
- 2. 2. Расчётно-теоретический анализ процессов тепломассообмена вроторно-плёночной установке
- 2. 3. Расчёт процессов газодинамики роторно-плёночной установки
- 2. 3. 1. Моделирование процессов газодинамикироторно
- 2. 3. 2. Решение уравнения радиальной скорости
- 2. 3. 3. Решение уравнения тангенциальной скорости
- 2. 4. Расчётные характеристики процессов газодинамики
- 2. 5. Выводы
- 3. 1. Общая методика и программа исследований
- 3. 2. Методика обоснования выбора компонентов исследуемой смеси
- 3. 3. Методика подготовки многокомпонентных смесей
- 3. 4. Методика расчёта теплового баланса роторно-плёночной установки
- 3. 5. Методика лабораторных исследований процесса удаления водотопливных фракций из отработанных смазочных масел
- 3. 6. Методика исследований процессов удаления водотопливных фракций нароторно-плёночной установке
- 3. 7. Методика определения физико-химических показателей регенерируемых масел
- 3. 8. Экспериментальная установка, применяемая аппаратура. Погрешность измерений
- 4. 1. Результаты расчёта теплового баланса роторно--плёночной установки
- 4. 2. Результаты лабораторных исследований процесса удаления водотоплиеных фракций
- 4. 2. 1. Результаты лабораторных исследований процесса удаления смеси углеводородов и воды
- 4. 2. 2. Результаты лабораторных исследований процесса удаления смеси дизельного топлива и вод
- 4. 2. 3. Результаты лабораторных исследований процесса удаления водотопливных фракций из отработанных смазочных масел
- 4. 3. Результаты экспериментальных исследований удаления водотопливных фракций на роторно-плёночной установке
- 4. 4. Параметры оптимизации процессов тепломассообмена
- 4. 5. Технология удаления водотопливных фракций из отработанных смазочных масел на роторно-плёночной установке
- 4. 7. Оценка эффективности научных разработок
Усовершенствование технологии удаления водотопливных фракций из отработанного смазочного масла путём оптимизации процессов тепломассообмена (реферат, курсовая, диплом, контрольная)
Повышение надёжности, долговечности и экономичности двигателей внутреннего сгорания является одной из главных задач машинно-тракторного парка (МТП). Мировая практика эксплуатации МТП свидетельствует о том, что наряду с повсеместным совершенствованием конструкции и технологии изготовления двигателей, качество используемых масел и топлив является важнейшим фактором, определяющим их технический моторесурс.
В условиях эксплуатации качество используемого смазочного маслаодно из немногих средств, позволяющих без существенных затрат достигнуть ощутимого повышения долговечности и экономичности двигателя.
Для правильного и обоснованного выбора и последующего использования смазочных масел специалисту недостаточно располагать данными о существующей номенклатуре масел и присадок, о конструктивных особенностях систем смазки того или иного двигателя.
Общие закономерности трения, износа и смазки деталей двигателя, влияние на интенсивость их изнашивания свойств используемых масел, изменение этих свойств по мере старения масел, взаимосвязь процесса старения с условиями, в которых находится работающее масло, методы оценки качества применяемого масла вообще и как объекта очистки, в частности, и, наконец, процессы очистки циркуляционных масел — таков краткий перечень вопросов, на основе изучения которых могут быть вскрыты резервы повышения моторесурса и экономичности двигателей внутреннего сгорания.
В процессе эксплуатации масла подвергаются более или менее значительным трансформациям, характер и глубина которых зависят от условий работы и свойств масел. В большинстве случаев эти трансформации таковы, что не исключают возможности повторного использования масел после надлежащей очистки и удаления продуктов старения.
Регенерация отработанных нефтепродуктов является одним из лучших способов их утилизации, так как обеспечивает возможность многократного использования сырья, приводит к увеличению ресурсов производства масел, предохраняет окружающую среду от загрязнения.
8,16,24,27,28,35,65,70,75,76].
Сбор и регенерацию отработанных масел ведут практически во всех промышленно развитых странах и в большинстве развивающихся стран. Доля смазочных материалов, подвергаемых регенерации, от общего сырья составляет: в США — 4.7%, Англии — 10.12%, Франции и Италии — 20.30% [21,43,80,83,84]. В нашей стране сбор отработанных масел составляет 10% от потребления свежих масел, а восстанавливается примерно 30% от собранных [43,55,59].
Целью диссертационной работы является усовершенствование технологии удаления водотопливных фракций из отработанных смазочных масел путём оптимизации процессов.
Научную новизну работы представляют следующие положения, выносимые на защиту:
1. Модель процессов тепломассообмена, обеспечивающая сокращение энергетических затрат на удаление водотопливных фракций из смазочных масел.
2. Технология реализации математической модели, учитывающая много-компонентность смазочных масел.
3. Многокомпонентная смесь, включающая основные соединения, содержащиеся в топливах и маслах.
4. Количественные характеристики и закономерности изменения параметров тепломассообмена.
Практическую значимость работы имеют:
1. Программа расчёта процессов газодинамики.
2. Методики расчёта теплового баланса роторно-плёночной установки и подготовки многокомпонентных смесей.
3. Параметры оптимизации процессов тепломассообмена. 8.
4. Технология удаления водотопливных фракций из отработанных смазочных масел.
Тема диссертационной работы утверждена Советом инженерного факультета Санкт-Петербургского государственного аграрного университета и соответствует Республиканской целевой научно-технической программе «Механизация, энергетика, автоматизация и ресурсосбережение» .
Общие выводы.
В результате выполненных исследований разработана усовершенствованная технология удаления водотопливных фракций из отработанного смазочного масла путём оптимизации процессов тепломассообмена, реализация которой обеспечивает сокращение энергетических затрат и времени, затрачиваемого на регенерацию ОСМ, а также применение комбинированных, экологически безопасных методов по удалению ВТФ.
Усовершенствованная технология базируется на следующих результатах исследований:
1. Разработанная модель процесса тепломассообмена и технология её реализации обеспечивает сокращение энергетических затрат на удаление ВТФ из ОСМ на 25% за счёт введения в ОСМ добавок воды от 15% до 40% и понижения температуры теплоносителя от 130 140 С до ЮО С. При увеличении процентного содержания воды более 40% в смеси с ОСМ исчезает экономическая эффективность добавки воды, так как энергетические затраты на передачу теплоты от теплоносителя, нагретого до 100 °C, к ОСМ превысят затраты на нагрев одного ОСМ до 200 С без добавок воды. Выигрыш во времени, затрачиваемом на удаление ВТФ из ОСМ в УПРТ, возрастает от 23% до 44% при введении добавок воды от 15% до 40%. При увеличении добавок воды свыше 40% временные затраты будут по прежнему уменьшаться.
2.Обоснованная многокомпонентная смесь, включающая основные соединения компонентов, содержащихся в топливах и маслах, и методика её подготовки позволяют обосновать методики лабораторных и экспериментальных исследований удаления ВТФ из ОСМ и провести лабораторные исследования. При этом состав модельных смесей отвечает процентному содержанию углеводородных соединений, топлива и воды в ОСМ.
3. Лабораторными исследованиями установлено влияние добавок воды на испарение модельных смесей. При добавке в дизельное топливо каждые 5% воды увеличивают количество удалённой смеси на 68%. Уменьшение абсолютного давления на 0,005МПа приводит к увеличению количества удалённой смеси на 5%. При добавке воды в модельную смесь, состоящую из масляной основы МС-20 и дизельного топлива, каждые 5% воды способствуют повышению эффективности испарения лёгких (на 5%) и средних фракций (на 10%) топлива. Температура вспышки возрастает в 1,1 раза при содержании в смеси не более 10% воды. При содержании воды более 10% рост увеличивается до 1,3 раз на каждые добавленные 5%. Темперао о тура греющей поверхности снижается с 200 С до 130−150 С.
4. Разработанная программа расчёта процессов газодинамики и методика расчёта теплового баланса УПРТ позволяют получить количественные характеристики, среди которых следует выделить следующие. При увеличении частоты вращения ротора (160−200об/мин) в 1,33 раза скорость в поперечном сечении канала увеличивается в 1,15 раза. При увеличении давления, создаваемого внутри УПРТ, в 3 раза (с 0,01МПа до 0,03МПа) скорость паров ВТФ вблизи ОСМ, стекающего по стенке испарителя, увеличивается в 2,3 раза. При одинаковой длине канала, по которому движутся пары ВТФ, осевая скорость возрастает 1,1 раза при уменьшении температурного перепада ОСМ на входе и выходе в испаритель УПРТ с 50 °C до 10 °C.
5. Разработанная методика расчёта теплового баланса УПРТ позволяет получить закономерности изменения параметров тепломассообмена. Коэффициенты теплоотдачи от теплоносителя к поверхностям, непосредственно воспринимающим от него количество теплоты, зависят от скорости движения теплоносителя. При увеличении скорости в 2 раза они возрастают в 1,27 раза. Коэффициенты теплоотдачи от внешней стенки УПРТ в окружающую среду и от внутренней стенки цилиндра испарителя к ОСМ возрастают в 1,14 и 1,4 о о раза при увеличении температуры теплоносителя от 100 С до 140 С. Доля теплоты, передаваемая теплоносителем к ОСМ возрастает в 1,61 раза, а доля потерь в окружающую среду уменьшается в 1,46 о о раза при увеличении температуры теплоносителя со 100 С до 140 С в большей степени, чем при увеличении скорости его движения в два раза (в 1,125 и 1,09 раза соответственно). Потери теплоты конвекцией от ОСМ к воздушному потоку внутри испарителя и доля этой составляющей в тепловом балансе УПРТ возрастают в 1,3 и 2 раза (с 4% до 8%) соответственно при уменьшении давления в испарителе с 0,04МПа до 0,015МПа. Тепловые потери через стенку трубопровода, соединяющего испаритель и конденсатор, падают в 2,3 раза при уменьшении давления внутри УПРТ с 0,04МПа до 0,015МПа. Время пребывания ОСМ в испарителе зависит от температуры ОСМ и длины испарителя и не зависит от частоты вращения ротора. При проведении эксперимента в диапазоне чисел оборотов от 200 до 350 и температуре теплоносителя 130−140 С время пребывания ОСМ в УПРТ, длина испарителя которого составляла 0,6 м, равнялось 15с.
6. Проведённый анализ способов удаления водотопливных фракций из ОСМ позволил выбрать способ тонкоплёночного испарения в качестве объекта усовершенствования технологии удаления ВТФ, а также провести экспериментальные исследования. Способ тонкоплёночного испарения, который обеспечивает непрерывность удаления ВТФ из ОСМ при более низких (100−140°С), по сравнению с кубовыми устройствами (240−420°С) температурах за счёт увеличения поверхности испарения в 3−5 раз и уменьшения времени пребывания масел в регенерационной установке с 15.30мин до 5.15с.
7. Экспериментальными исследованиями установлено, что наиболее экономически эффективным способом, ускоряющим процесс удаления ВТФ в УПРТ, по сравнению с повышением температуры теплоносителя со 100 °C до 140 С является добавка воды в ОСМ, превышающая 15% от общего объёма регенерируемой смеси. Значение кислотного числа равное 0,004мгк0н/мл можно достичь при температуре теплоносителя 140 °C и добавке воды 12%, либо при температуре теплоносителя 100 С и добавке воды 25%. Добавка воды о о позволяет снизить температуру нагрева со 130−150 С до 100 Суменьшить кислотное число до уровня близкого к нулевому, предъявляемого к товарным масламуменьшить содержание присадок: при 20% добавке воды содержание присадки ПМСЯ (а, б) уменьшается в 1,13 раза, а присадки ВНИНП-354 в 1,23 раза.
8. На основании экспериментальных исследований удаления ВТФ из ОСМ и разработанной модели тепломассообмена проведена оптимизация таких параметров как: частота вращения ротора (250−400об/мин), давление внутри испарителя (0,01−0,02МПа), температура теплоносителя (100−140°С), содержание воды в ОСМ (15−40% от объёма смеси), температура ОСМ на входе в испаритель (не более 100°С). Оптимизация параметров процессов тепломассообмена позволила разработать усовершенствованную технологию удаления ВТФ из ОСМ. При аномальном, превышающем 5% содержании топлива в ОСМ необходима добавка воды, в три раза превышающая процентное содержание топлива. При регенерации смазочных масел, не относящихся к моторным добавка воды не нужна (см. табли-ДУ 1).
9. Эффективность научных разработок характеризуется экономией энергетических затрат на нагрев 1 кг ОСМ и поддержание требуемого температурного уровня (см. таблицу 1), которые составляют 25кВт. По сравнению с базовым вариантом, где суммарное снижение мощности на подготовительные операции и привод технологических систем составило 9,55кВт экономия энергетических затрат почти в 2,5 раза больше. Кроме этого, уменьшается время, затрачиваемое на удаление ВТФ в УПРТ от 1,2 до 2 раз при добавке воды от 10% до 40%.
10. Математическая модель процессов тепломассообмена при удалении водотопливных фракций из отработанных смазочных масел, методика расчёта теплового баланса роторно-плёночной установки приняты к внедрению Академией прикладных технологий (Санкт-Петербург). Основные результаты исследований, реализованные в виде усовершенствованной технологии удаления ВТФ, из ОСМ приняты к внедрению научно-исследовательской лабораторией кафедры «Тракторы, автомобили и теплоэнергетика» СПГАУ.
Список литературы
- Авдонин Ю.А., Олевский В. М., Попов Д. М. Исследование гидродинамики плёночного течения жидкости при противотоке газа. -Химическое и нефтяное машиностроение, 1965, № 12. -с. 16.20.
- Авдонькин А.Ф. Исследование гидродинамики и теплообмена в вертикальном плёночном роторном аппарате с жёстко закреплёнными лопастями. -Автореф. дисс. на соиск. уч. ст. канд. тех. наук, Л.: 1971, -17с.
- Аверин Е.К., Кружилин Г. Н. Влияние поверхностного натяжения и вязкости на условия теплообмена при кипении воды. -Известия АНСССР, ОТН, 1955, № 10, -С.131.137.
- Арсенин В.Я. Математическая физика. Основные уравнения и специальные функции. -М.: Наука, 1966, -368с.
- Бажан П.И., Каневец Г. Е., Селиверстов В. М. Справочник по тепло-обменным аппаратам. -М.: Машиностроение, 1988, -365с.
- Бегачёв В.И. Исследование теплообмена в аппарате с механическим перемешивающим устройством. -Автореф. дисс. на соиск. уч. ст. к.т.н., Л.: 1967,-18с.
- Бенуа Г. Ф., Точильников Д. Г., Ронинский H.A., Селиванов Ф. Ю. Методика ускоренных натурных исытаний моторных масел для судовых дизелей. -Двигателестроение, 1979, № 9, -С.56.58.
- Бенуа Г. Ф., Данилова Е. В., Точильников Д. Г. Сравнение процессов старения товарного и регенерированного моторных масел при работе в судовом дизеле. Двигателестроение, 1979, № 11, -с.46.,.48.
- Бенуа Г. Ф., Данилова Е. В., Точильников Д. Г. Радиоиндикаторные исследования противоизносных свойств товарного и регенерированного масел. Двигателестроение, 1979, № 12, -С.37.39.
- Бутов Н.П. Система восстановления и использования отработанных автотракторных масел в АПК. -Автореф. дис. на соиск. уч. ст. д.т.н., Зерно-град, 1996, -40с.
- Бухтер А.И., Холин И. Н., Непогодьев A.B. Ужесточение требований к качеству отработанных масел сырья регенерации. -Химия и технология топлив и масел, 1987, № 9, -с.30.,.31.
- Бэтчелор Д. Введение в механику жидкостей. -М.: Мир, 1973, -758с.
- Венцель C.B. Смазка двигателей внутреннего сгорания. -М.: Маш-гиз, 1963,-180с.
- Гончаренко В.Г. Регенерация автотракторных масел. -Саратов: Облгосиздат, 1988, -104с.
- Григорьев М.А., Бунаков Б. М., Долецкий В. А. Качество моторного масла и надёжность двигателей. -М.: Изд-во стандартов, 1981, -232с.
- Громашев C.B. Совершенствование технологии удаления водотоп-ливных фракций из моторных масел путём разработки малогабаритной реге-нерационной установки и обоснование режимов её работы. -Автореф. дисс. на соиск. уч. ст. к.т.н., СПб, 1997, -17с.
- Гуреев A.A., Азев B.C., Камфер Г. М. Топливо для дизелей. Свойства и применение. -М.: Химия, 1993, -336с.
- Демченко B.C., Иванов JI.B., Горенков А. Ф. Химия и технология горючего и смазочного материалов. -JL: 1971, -270с.
- Доманский И.В. Гидродинамика и теплообмен в газожидкостных аппаратах химической технологии. -Автореф. дисс. на соиск. ст. д.т.н., JI.-, 1976,-42с.
- Доманский И.В., Исаков В. П., Островский Г. М., и др. Машины и аппараты химических производств. Л.: Машиностроение. Ленинградское отделение, 1982, -384с.
- Евдокимов А.Ю., Фалькович М. И. Вторичная переработка отработанных масел за рубежом. -Химия и технология топлив и масел, 1988, № 10, -С.42.45.
- Живайкин Л.Я., Волгин Б. Н. Определение величин уноса жидкости с поверхности плёнки потоком газа. -Инженерно-физический журнал, 1961, т.4, № 8, -С.114.116.
- Житинкин A.A. Разработка и исследование роторного плёночного аппарата для непрерывной абсорбции углекислого газа поливинилхлоридной пастой. -Автореф. дисс. на соиск. уч. ст. к.т.н., Л.: 1967, -21с.
- Заявка № 94 037 575./ Способ очистки отработанных масел от воды и низкокипящих фракций и устройство для его осуществления. //C.B. Грома-шев, А. П. Картошкин, Л. А. Ашкинази, М. И. Браславский, В. Я. Фрайштадт, 1994.
- Закупра В.А., Козак В. А., Колосова Э. В., Выхрестюк Н. И. Содержание углеводородов в смазочном масле. -Химия и технология топлив и масел, 1979, № 3 -С.58.62.
- Исаченко В.П., Осипова В. А., Сукомел B.C. Теплопередача.- М.: Энергоиздат, 1981 -417с.
- Исследование процессов отгона водотопливных фракций при регенерации отработанных моторных масел. /C.B. Громашев, A.M. Хандов. //Тез. докл. научно-тех. семинара стран СНГ (СПГАУ). -Спб., 1996, -с.30.,.32.
- Исследование процесса удаления водотопливных фракций из моторных масел. /Л.А. Ашкинази, А. П. Картошкин, A.M. Хандов. // Двигателе-строение, 2000, № 3 -с. 30−32 .
- Кадер Т.Л., Олевский В. М., Дмитриев М. А. Гидродинамика газового потока в плёночной трубчатой колонне при противоточном течении фаз. -Теоретические основы химической технологии, 1971, т.5, № 2, -с.259.,.267.
- Калишевич Ю.И., Таубман Е. И., Кожелупенко Ю. Д. Экспериментальная оценка теплообмена при испарении воды в нисходящей плёнке. -Инженерно-физический журнал, 1971, т.21, № 6, -с.1039.1043.
- Касаткин А.Г. Основные процессы и аппараты химической технологии. -М.: Химия, 1971, -784с.
- Кириллов А.И., Рис В.В., Смирнов Е. И., Ходак А. Е. Расчёт трёхмерных турбулентных течений в турбомашинах на основе решения парабо-лизованных уравнений Навье-Стокса. -Теплоэнергетика, 1993, т. З, -с.28.31.
- Кламман Д. Смазки и родственные продукты. Синтез. Свойства. Применение. Международные стандарты. /Пер. с англ. /Под ред. Ю. С. Заславского. -М.: Химия, 1988, -488с.
- Коваленко В.П., Карпекина Т. П. Экономия масел и смазок при эксплуатации машин. -М.: Агропромиздат, 1988, -56с.
- Коваленко В.П., Зыков С. А., Олейник А. Н. Регенерация отработанных моторных масел. -Тракторы и с.-х. машины, 1995, № 1, -с. 13. 16.
- Коган В.Б., Харисов М. А. Оборудование для разделения смесей под вакуумом. -Л.: Машиностроение, 1976, -375с.
- Колешко С.Б. Разностная схема для решения уравнений стационарных течений вязкой жидкости. -Численные методы механики сплошной среды, Новосибирск, 1979, т. 10, № 3, -с.100.104.
- Кошляков Н.С., Глинер Э. Б., Смирнов М. М. Основные дифференциальные уравнения математической физики. -М.: Физматгиз, 1962, -767с.
- Ленивцев Г. А., Глазков В. Р., Мартьянов В. Е. Обоснование режимов регенерации моторных масел с целью повторного их использования. //Химмотология: Матер. семин./О-во «Знание» РСФСР Моск. дом научно-тех. проп. -М., 1990, -с.85.88.
- Лойцянский Л.Г. Механика жидкости и газа.-М.:Наука, 1970, -304с.
- Лошков Б.В. Физико-химические основы регенерации масел. -М,-Л.: Гостоптехиздат, 1948, -164с.
- Лохтов В.Н., Малюсов В. А., Жаворонков Н. М. Определение фазовых сопротивлений в процессе плёночной ректификации по профилю концентраций. -Теоретические основы химических технологий, 1967, т.1, № 3, -С.319.321.
- Мисникевич А.Д. Регенерация отработанных масел в СССР и за рубежом. -Сер. «Ремонт предприятий» -М.: НИИТЭхим., 1987,-44с.
- Морозов Г. А. Применение топлив и масел в дизелях. -Л.: Недра, 1964,-330с.
- Мухортов И.В., Брагина Е. И. Зависимость свойств регенерированного моторного масла от глубины очистки сырья. //Тех. эксплуат., надёжн. и соверш. автомобилей. -Челябинск, 1996, -С.88.92.
- Олевский В.М., Ручинский В. Р. Ректификация термически нестойких продуктов. -М.: Химия, 1972, -200с.
- Олевский В.М., Ручинский В. Р. Роторно-плёночные, тепло- и мас-сообменные аппараты. -М.: Химия, 1977, -207с.
- Павлов А.Г., Резников В. Д. Новые требования к моторным маслам за рубежом. -Химия и технология топлив и масел, 1994, № 7−8, -С.33.37.49. Патент № 1 610 990 (СССР).50. Патент № 198 671 (ЧССР).
- Постановка задачи газообмена роторно-плёночного испарителя. /A.M. Хандов.// Тез. докл. Межд. научно-тех. конф. «Транском-97″. -Спб, 1997, -с.146.148.
- Проскуряков В.А., Драбкин А. Е. Химия и технология нефти и газа. -Л.: Химия, 1989, -421с.
- Разработка малогабаритного модульного регенерационного комплекса. /A.B. Николаенко, А. П. Картошкин, C.B. Громашев, В. А. Филимонов. //Тез. докл. 8-ого научно-тех. семинара (Саратовский ГАИУ). -Саратов, 1995. -с.37.
- Регенерация азеотропных смесей отработанных моторных масел. /А.П. Картошкин, А. Г. Потапков, A.M. Хандов // Тез. докл. научно-тех. семинара стран СНГ (СПГАУ), -Спб., 1998, -с.49.
- Регенерация отработанных масел и их повторное использова-ние.Обз. информ. /Госагропром СССР. АгроНИИТЭИИТО. /Сост. КБ. Рыбаков, В. П. Коваленко, В. В. Нигородов. -М., 1989. -26с.
- Резников В.Д., Шипулина Э. И. Критерии, определяющие необходимость смены судовых и тепловозных дизельных масел. //Химмотология: Матер. семин./0-во „Знание“ РСФСР Моск. дом научно-тех. проп. -М., 1990, -С.40.47.
- Рекомендации МСХ СССР по внедрению достижений науки и передового опыта в производство. / Реф. сб. ВАСХНИИЛ, ВНИИТ-ЭИСХ, Вып 6,-М., 1984, -C.74.78.
- Рид Р., Шервуд Т. Свойства газов и жидкостей. -Л.: Химия, 1971,704с.
- Сбор и очистка отработавших масел. Обзор, информ. /Госагропром СССР. АгроНИИТЭИИТО. / Сост. К. В. Рыбаков, В. П. Коваленко, В. В. Нигородов. -М., 1988, -30с.
- Тананайко Ю.М., Воронцов Е. Г. Методы расчёта и исследования плёночных процессов. -Киев: Техника, 1975, -312с.
- Технология очистки отработанных машинных масел. // Матер. 1-ой Гор. научн.-практ. конф.-ярмарки „Наукоёмкие природоохр. технол.“, Тольятти, 27−30 июня 1994, Тольятти, 1994, -60с.
- Толубинский В.И., Островский Ю. Н. Механизм парообразования и интенсивности теплообмена при кипении бинарных смесей. -Теплоотдача при изменении агрегатного состояния вещества. -Киев: Наукова думка, -С.7.16.
- Трейманн A.A., Микалл В .Я., Смирде Э. К. Захлёбывание при условии умеренного вакуума. -Труды Таллинского политех, и-та, 1969, № 283, -С.47.54.
- Уоллис Г. Одномерные двухфазные течения. -М.: Мир, 1972, -440с.
- Устройство для определения маслянистости смазочных материалов. Патент РФ № 2 125 256 МКИ 6 G 01 N 13/02. //Филимонов В.А., Картошкин А. П., Беляев Ю. Н., Ашкинази JI.A.- С-Петербургский государственний агротехнический университет.
- Устройство для регенерации отработанных жидких масел: а.с. 1 783 225 СССР, МКИ 5F16N39/06. НЕМ. Пирожниченко, И. Я. Чернышенко, М. Д. Коневцев, И.Я. Чумаченко- Азово-Черноморский ин-т механ. с.х.
- Учёт компонентности топлив при моделировании системы регенерации масел. /А.П. Картошкин, А. Г. Потапков, A.M. Хандов //Сб. научн. тр."Судостроение и судоремонт"(СПГУВК), Спб, 1998, -с. 106.109.
- Федотов В.В., Плановский А. Н., Фокин А. П., Лебедев К. И. Обезвоживание химических реактивов в плёночных роторных аппаратах. -Хим. промышленность, 1971, № 3, -С.237.238.
- Филимонов В.А., Ашкинази Л. А., Картошкин А. П., Николаенко A.B., Беляев Ю. Н. Результаты исследований углеводородного состава смазочных масел в процессе эксплуатации и регенерации. -Журнал прикладной химии, 1999, № 5, -с.685−689.
- Фукс И.Г., Евдокимов А. Ю., Лашхи В. Л., Саидахмедов Ш. М. Экологические проблемы рационального использования смазочных материалов. -М.: Изд."Нефть и газ», 1993, -164с.
- Шашкин Л. И" Брай И. В. Регенерация отработанных нефтяных масел. -М.: Химия, 1970, -304с.
- Шишкин В.В. Исследование гидродинамики и теплообмена в вертикальном плёночном роторном аппарате с жёстко закреплёнными лопастями. -Автореф. дисс. на соиск. уч. ст. к.т.н., Л., 1972, -19с.
- Щагин В.В., Двойрис Л. И. Старение и очистка дизельных масел. -Калининград, кн. изд., 1971, -200с.
- Щур С. Г. Исследование гидродинамики и расчёт гидродинамических усилий, действующих на лопасти мешалки в аппарате с механическим перемешиванием. -Автореф. дисс. на соиск. уч. ст. к.т.н., Л., 1983, -16с.
- Экологически чистые технологии регенерации отработанных смазочных масел. /Николаенко А.В., Картошкин А. П. // Экология и развитие Северо-Запада России: Тез. докл. второй межд. Конференции. -Спб., 1997, -с.43., 44.
- Эколого-экономический антагонизм при вторичной переработке отработанных смазочных масел. /Картошкин А.П. // Улучшение эксплуатационных показателей двигателей, тракторов и автомобилей: Тез. докл. науч-но-тех. семинара стран СНГ, -СПб., 1997, -с.119.120.
- Ярошенко В В. Гидродинамика и теплообмен в аппаратах с мешалками и неподвижным внутренним устройством. -Автореф. дисс. на соиск. уч. ст. к.т.н., Л., 1988,-17с.
- Bhan O.K., Wei-Ping Tai, Brinkman D.W. -Fuel Science and technology Intern., 1986, v.4, № 3. -p.303.325.
- Booth G., Bachetti J.A. -Chemical Proc., 1983, v.46, № 1. -p. 34.35.
- Brinkman D.W. -CEP, 1986, № 3. -p.67.70.
- Condition monitoring of engine oils. /Sorab Jagadish, Van Arsdate W.E. /SAE Techn. Pap. Ser., 1990, № 902 066. -p.l.7.
- Ind. Lubric. and Tribology, 1985, v.27, № 1. -p.4.5.
- Maies E. -Lubricat. Eng., 1987, v.43, № 3. -р.162.166.
- Tribologie und Schmierungstechnik, 1986, Jh. 33, № 2. -s. 131.134.