Другие работы

Рекомендовано при контроле блока цилиндров, при отсутствии высокоточных средств измерений, рекомендуется применять индикаторный нутромер с измерительными головками МИГ-1, МИГ-2 с использованием методики многократных измерений, но наиболее целесообразным является применение имеющей высокую стоимость, но наименьшую погрешность измерений электронной пробки ЦДЗМ, при этом достаточно проведение…
Диссертация 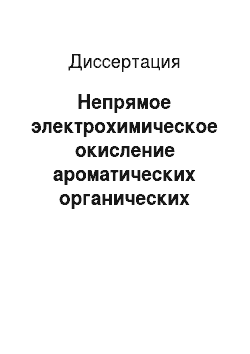
Продемонстрирован эффект снижения концентрации органических веществ класса фенолов и красителей антрахинонового ряда в имитатах сточных вод, содержащих 1,3-дигидроксибензол и натриевую соль 3,4-дигидрокси-9,10-диоксо антрацен сульфоновую-2 кислоту до уровня 4−10% от первоначальных значений за счет непрямого окисления метастабильными продуктами электролиза. Теоретически обоснована эффективность…
Диссертация 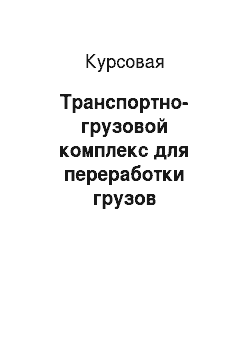
Именно поэтому в целях оптимизации погрузочно-разгрузочных работ был осуществлен последовательный переход от создания и внедрения отдельных машин, оборудования, приборов и технологических процессов к разработке, производству и массовому использованию высокоэффективных транспортно-грузовых систем, а также к современным методам организации труда и управления. транспортный грузовой подъемный машина…
Курсовая 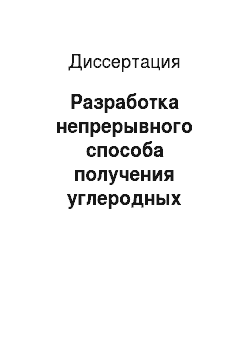
Длительное время наиболее ценными считались ОНТ. Это весьма трудно получаемый материал, имеющий наиболее высокие по сравнению с другими видами углеродных НТ себестоимость и цену и поэтому находящий ограниченное применение. Однако многослойные НТ с числом слоев от 2 до 5 (т-МНТ) не уступают однослойным по механическим, электрическим и электрофизическим характеристикам и значительно превосходят…
Диссертация 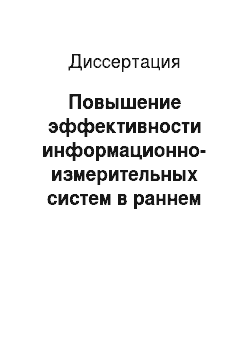
Одним из наиболее перспективных направлений в решении задач раннего распознавания осложнений является использование станций геолого-технологического контроля, обеспечивающее контроль и диагностирование изменения текущей ситуации в скважине. Серьезной задачей является привлечение современных средств обработки текущей информации и компьютерных технологий для оперативного контроля ситуаций…
Диссертация 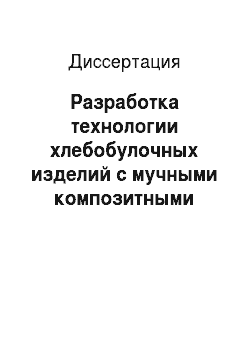
Однако использование нетрадиционных видов сырья ухудшает органо-лептические и физико-химические показатели теста и изделия. Для нейтрализации их отрицательного влияния возможно модернизировать технологию приготовления: предварительной подготовкой обогатителей, выбором рационального способа приготовления теста, режимов замеса, температуры, оптимизацией реологических свойств полуфабриката…
Диссертация 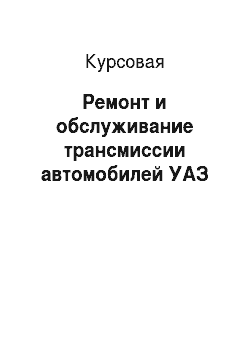
Все усовершенствованные машины имели колесную формулу 4×4, заднеприводные модификации сняли с производства. После развала СССР спрос на грузовые УАЗы по-прежнему оставался высоким. В начале 1990;х гг. лучше продавались бортовые грузовички и фургоны, покупаемые мелкими предпринимателями. Но после появления «Газели» спрос на них упал. В середине 1990;х гг. хорошо пошла «санитарка» УАЗ-3962. Дело…
Курсовая 
Ключом" к созданию высокоинтенсивных электромембранных процессов является построение теории «запредельного» состояния мембранных систем и поиск новых механизмов доставки ионов к межфазной поверхности мембрана/раствор. Первым фундаментальным исследованием, направленным на раскрытие феномена «запредельного» состояния мембранных систем, явилась работа Сонина А. А. и Пробстена Р. Ф., опубликованная…
Диссертация 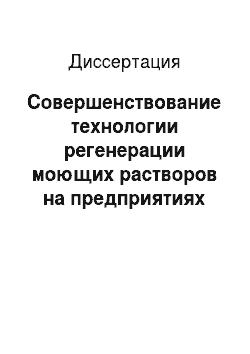
Решение этой задачи необходимо осуществлять, внедряя современные экологически чистые процессы и технологии. В настоящее время наиболее эффективными и прогрессивными в технологии очистки отработанных моющих растворов являются методы электрообработки. Применение данных методов позволяет непосредственно воздействовать на систему «раствор-загрязнение» и выделять из объема раствора загрязнения любой…
Диссертация 
Показано, что обработка поверхности стали фенолои карбами-доформальдегидными модификаторами приводит к увеличению адгезионной прочности покрытий из порошковых эпоксидных красок. Наиболее высокие значения адгезии достигаются при кислотной обработке поверхности перед ее модификацией (адгезионная прочность увеличивается приблизительно в 1,7 раза). Одновременно происходит стабилизация адгезии…
Диссертация 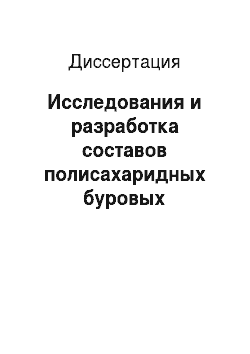
Выполнение планов добычи углеводородного сырья в России напрямую связано с повышением технико-экономической эффективности буровых работ. В структуре буровых работ отмечается тенденция роста наклонно направленного бурения скважин с горизонтальным окончанием ствола, в последние годы доля таких скважин выросла до 15% от общего числа. Также увеличиваются объемы бурения скважин со сложными…
Диссертация 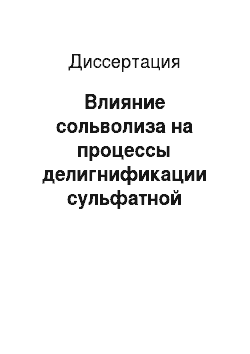
Научная новизна. Впервые систематически исследована кинетика процесса делигнификации лиственной сульфатной целлюлозы в водных растворах диоксана и этанолаизучена кинетика деструкции целлюлозы и избирательность ее делигнификациивпервые определены параметры полихронной кинетики для процесса делигнификации сульфатной целлюлозы в среде водного диоксана, определены константы скоростей реакций kmin…
Диссертация 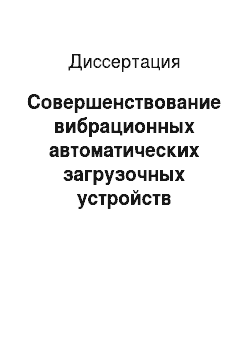
В 50-е годы в России интенсивно внедряются автоматические роторные линии (APJI) и затем в 60-е годы роторно-конвейерные линии (APKJI) конструкции JI.H. Кошкина с производительностью соответственно до 200 и 1200 шт/мин. Объединение в одной APJI до шести технологических операции позволило значительно снизить число типоразмеров АЗУ и увеличить производительность линий в 2−3 раза по сравнению…
Диссертация 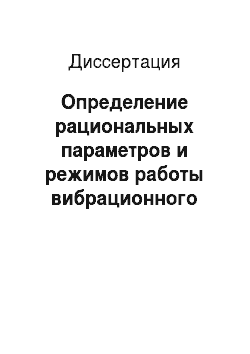
Основные положения диссертационной работы докладывались и обсуждались на международной конференции РАН «Проблемы механики современных машин», г. Улан-Удэ, 2000 г.- на международном симпозиуме «Механизмы и машины ударного, периодического и вибрационного действия», г. Орел, 2000 г.- на международной научно-технической конференции «Интерстроймех-2001», г. Санкт-Петербург, 2001 г.- на международной…
Диссертация 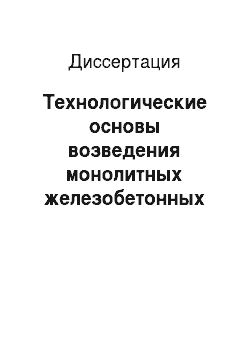
Впервые исследованы качественные изменения состояний технологической системы монолитного каркасного высотного жилищного строительства при различных внешних условиях. Показана необходимость комплексного и однонаправленного изменения составляющих системы для повышения адаптивности и эффективности ее функционирования при изменении внешних условий. Сформулирована конечная цель таких изменений…
Диссертация