Закономерности формирования структуры при ионно-вакуумном азотировании титановых сплавов
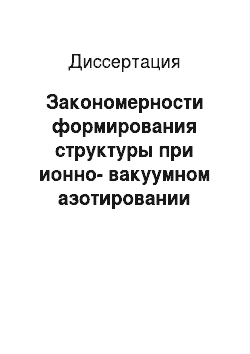
Титановые сплавы занимают важное место среди современных конструкционных материалов, благодаря удачному сочетанию физических, механических и технологических свойств. Низкая плотность, высокая коррозионная стойкость, высокая удельная прочность и жаропрочность делают эти сплавы незаменимыми для авиационной и космической техники. В последнее время наметилась тенденция расширения области применения… Читать ещё >
Содержание
- Глава I. Состояние вопроса
- 1. 1. Методы поверхностного упрочнения титановых сплавов
- 1. 2. Технология ионного азотирования и структура азотированного слоя
- 1. 2. 1. Общая характеристика ХТО и особенности ионного 22 азотирования
- 1. 2. 2. Структура азотированного слоя
- 1. 2. 3. Влияние параметров ионного азотирования на формирование модифицированной поверхности титановых сплавов
- 1. 3. Анализ влияния химического состава и структуры титановых сплавов на формирование модифицированной поверхности при 37 азотировании
- 1. 4. Анализ влияния поверхностного упрочнения на механические ф свойства титановых сплавов
Закономерности формирования структуры при ионно-вакуумном азотировании титановых сплавов (реферат, курсовая, диплом, контрольная)
Титановые сплавы занимают важное место среди современных конструкционных материалов, благодаря удачному сочетанию физических, механических и технологических свойств. Низкая плотность, высокая коррозионная стойкость, высокая удельная прочность и жаропрочность делают эти сплавы незаменимыми для авиационной и космической техники. В последнее время наметилась тенденция расширения области применения титановых сплавов, в частности, в медицине для изготовления имплантатов и в автомобилестроении. Однако, более широкое их использование сдерживается из-за неудовлетворительных триботехнических характеристик.
Одним из наиболее эффективных способов улучшения фрикционных свойств титановых сплавов является создание модифицированных поверхностных слоев (диффузионных слоев) в материале подложки, образующихся за счет диффузии ионов газов. Для этих целей, в частности, применяют термодиффузионное азотирование (ТДА), ионное азотирование и ионную имплантацию. Термодиффузионное азотирование осуществляется при температурах выше 850 °C и требует длительных выдержек, что является существенным недостатком этого метода. Применение же ионной имплантации приводит к образованию модифицированного слоя протяженностью не более 1 мкм, что часто недостаточно для обеспечения эрозионной стойкости поверхности.
Одним из существенных преимуществ ионного азотирования является возможность получения контролируемого распределения твердости и модулей упругости в поверхностных слоях материала за счет управления параметрами техпроцесса, такими как температура, давление газа и состав газовой смеси. Однако до настоящего времени для получения протяженных модифицированных слоев в основном используют сравнительно высокие температуры (750−800°С), которые могут менять микрогеометрию поверхности и приводить к существенным изменениям структуры и свойств сердцевины изделия.
В МАТИ-РГТУ им. К. Э. Циолковского совместно с ОАО «НИАТ» был разработан метод вакуумной ионно-плазменной обработки поверхности, позволяющий в едином цикле проводить ионно-вакуумное азотирование и нанесение нитридных покрытий в модифицированной установке «Булат». Данный метод позволяет снизить температуру процесса до 500−600°С, а продолжительность поверхностной обработки до 1 часа. Однако для полной реализации преимуществ ионно-вакуумного азотирования необходимо проведение комплексного исследования влияния технологических параметров процесса и исходной структуры подложки на формирование структуры поверхностных слоев.
Известно, что химический состав и структура титановых сплавов оказывает существенное влияние на формирование диффузионных слоев при азотировании. Однако систематических исследований в этом направлении до настоящего времени не проводилось. Поэтому задача исследования закономерностей формирования структуры азотированного слоя в процессе ионно-вакуумного азотирования в зависимости от химического состава и исходной структуры титановых сплавов является актуальной.
Научная новизна:
1. Показано, что размер структурных составляющих в двухфазных титановых сплавах оказывает влияние на процесс азотирования: с повышением дисперсности а-фазы увеличивается протяженность диффузионной зоны с образованием а-твердого раствора, и уменьшается количество нитридных фаз на поверхности.
2. Показано, что глубина диффузионного слоя а-твердого раствора азота при ионно-вакуумном азотировании в интервале температур 550−650°С для атитановых сплавов определяется системой и степенью легирования, а для а+р-щ титановых сплавов — соотношением количества аи Р-фаз в структуре при этих температурах.
3. Установлено, что в отожженном состоянии глубина диффузионного слоя с увеличением в структуре количества Р-фазы до 30% увеличивается в 1,4 раза по сравнению с титаном за счет более высокой скорости протекания процессов диффузии азота в Р-фазе. Увеличение в структуре объемной доли Р-фазы от 30 до 100% вызывает уменьшение протяженности диффузионной зоны, вследствие меньшей растворимости азота в Р-фазе.
4. Показано, что образование в поверхностном слое а-твердого раствора внедрения практически не оказывает влияния на значения предела прочности и относительного удлинения при кратковременных испытаниях, но, вследствие существования в нем растягивающих напряжений, уменьшает на 30% предел выносливости при циклических нагрузках.
Практическая значимость;
1. Разработаны рекомендации по технологии ионно-вакуумного азотирования изделий из титановых сплавов, не испытывающих знакопеременных нагрузок в процессе работы в условиях трения по сверхвысокомолекулярному полиэтилену, включающие азотирование при температуре 550 °C в течение 60 минут, что позволяет получить на поверхности изделий прочную беспористую пленку, стойкую к истиранию.
2. Разработаны режимы упрочняющей термической и поверхностной обработок для изделий из высокопрочного титанового сплава ВТ22, способных выдерживать контактные напряжения в условиях ограниченной подвижности до 2,5ГПа. Проведение закалки с температур Р-области с последующим старением при 550 °C в течение 6 часов и ионно-вакуумного азотирования при 530 °C в течение 60 минут обеспечивают получение твердости в объеме материала 49−50 ед. HRC, а на.
0 поверхности — износостойкого слоя с твердостью 56−57 ед. HRC.
Разработанные технологии были использованы ЗАО «Имплантат МТ» при производстве элементов эндопротезов тазобедренного сустава, что подтверждено соответствующим актом.
Апробация работы. Материалы работы доложены на 8 научно-технических конференциях и семинарах, в том числе: на Молодежных научно-технических конференциях «МАТИ"-РГТУ им. К. Э. Циолковского «Гагаринские чтения» (2002г., 2004 г., Россия), на Научно-технической конференции «Новые материалы и технологии» (2002г., Россия), на II НПК молодых ученых и специалистов «Исследования и перспективные разработки в авиационной промышленности» (2004г., Россия), на III Международной конференции «Ti-2005 в СНГ» (2005г., Украина), на конференции «Структура и свойства материалов с особыми свойствами» (2005г., Россия), на II Франко-российском семинаре «Новые достижения в материаловедении» (2005г., Россия).
Основные выводы.
1. Исследованы закономерности формирования структуры в титановых сплавах различных классов при ионно-вакуумном азотировании. Показано, что послойное формирование фазового состава модифицированного слоя происходит в соответствии с диаграммой состояния Ti-N. В процессе обработки а-титановых сплавов вначале происходит образование твердого раствора внедрения азота в а-фазе, а для двухфазных сплавов инициированное азотом >а превращение с образованием в конечном итоге на поверхности слоя нитридов от состава Ti2N до состава TiN.
2. Показано, что температура и время выдержки оказывают существенное влияние на качество поверхности после ионно-вакуумного азотирования. При температурах выше 550 °C и временах выдержки, не превышающих 60 минут, образуется плотная беспористая нитридная пленка, которая не приводит к изменению шероховатости поверхности. Повышение температуры ионно-вакуумного азотирования до 600 °C приводит к появлению в нитридном слое отдельных мелких пор, размер которых при продолжительности обработки до 30 минут не превышает 0,5 мкм. Увеличение времени выдержки или дальнейшее повышение температуры азотирования до 700−800°С вызывает как увеличение количества пор и их размера, так и шероховатости поверхности.
3. Установлено, что состав газовой смеси 16%N2 и 84%Аг является оптимальным для проведения ионно-вакуумного азотирования титановых сплавов. При меньшем содержании азота происходит заметное снижение как глубины диффузионной зоны, так и поверхностного упрочнения, а увеличение содержания азота в газовой фазе приводит к быстрому формированию на поверхности нитрида TiN, затрудняющему дальнейшую диффузию азота вглубь металла.
4. Установлено, что размер структурных составляющих в двухфазных титановых сплавах оказывает влияние на процесс азотирования. Если в результате предварительной термической обработки формируется структура с частицами а-фазы меньше 1 мкм, то глубина диффузионного слоя в 1,2 раза больше, чем после азотирования образцов с размером структурных составляющих 2−4 мкм. Дальнейшее укрупнение структуры не оказывает существенного влияния на протяженность модифицированного слоя.
5. Установлено, что чем больше глубина диффузионного слоя, тем меньше количество нитридов, образующихся на поверхности, и, следовательно, меньше упрочнение поверхностных слоев, что обусловлено интенсивным протеканием процессов абсорбции азота. Уменьшение протяженности модифицированного слоя приводит к значительному упрочнению поверхности за счет образования большего количества нитридов, вследствие того, что скорость процесса адсорбции ионов азота выше, чем их диффузия вглубь материала подложки.
6. Показано, что для однофазных а-титановых сплавов процесс ионно-вакуумного азотирования определяется системой и степенью легирования сплава. В частности, введение в а-титан 5% (по массе) алюминия существенно снижает количество абсорбированного в а-твердом растворе азота, что выражается в уменьшении почти в 2 раза интегральной микротвердости диффузионной зоны и обусловлено затруднением процессов диффузии, вследствие увеличения прочности межатомной связи а-фазы при легировании алюминием.
7. Установлено, что количественное соотношение аи Р-фаз, зависящее от химического состава титанового сплава, влияет на глубину диффузионного слоя. Увеличение в структуре отожженных сплавов количества Р-фазы до 30% приводит к увеличению в 1,4 раза глубины азотированного слоя по сравнению с титаном за счет более высокой скорости диффузии азота в р-фазе. Увеличение в структуре объемной доли Р-фазы с 30 до 100% вызывает уменьшение протяженности диффузионной зоны вследствие низкой растворимости азота в Р-фазе и необходимости реализации Р~>а превращения не только за счет роста уже существующих частиц a-фазы, но и образования новых зародышей.
8. Показано, что образование в поверхностном слое твердого раствора внедрения приводит к незначительному уменьшению кратковременных механических свойств (предел прочности и относительное удлинение уменьшаются на 5%, а относительное сужение — на 14%). Однако, из-за возникновения в а-твердом растворе растягивающих напряжений величиной до 240МПа, происходит уменьшение предела выносливости с 575 МПа в исходном состоянии до 400 МПа после азотирования.
9. Проведенные триботехнические испытания показали, что формирующаяся в процессе ионно-вакуумного азотирования структура модифицированных поверхностных слоев образцов из сплава ВТ20 позволяет исключить износ и снизить коэффициент трения по сверхвысокомолекулярному полиэтилену с 0,13 до 0,03, а на образцах из сплава ВТ22 — выдерживать контактные напряжения до 2,5 ГПа без износа при испытаниях в условиях трения качения по диску из стали ЮОСгб.
10. Разработаны рекомендации по совершенствованию технологии ионно-вакуумного азотирования изделий из титановых сплавов, не испытывающих знакопеременных нагрузок в процессе работы в условиях трения по сверхвысокомолекулярному полиэтилену, включающие азотирование при температуре 550 °C в течение 60 минут, что позволяет получить на поверхности изделия прочную беспористую пленку, стойкую к истиранию при нагрузках 2250Н.
11. Разработаны режимы упрочняющей термической и поверхностной обработок для изделий из высокопрочного титанового сплава ВТ22, способных выдерживать контактные напряжения в условиях ограниченной подвижности до 2,5ГПа, что обеспечивается получением твердости в объеме материала 49−50 ед. HRC, а на поверхности износостойкого слоя с твердостью 56−57 ед. HRC, состоящий из закалки с температур р-области с последующим старением при 550 °C в течение 6 часов и ионно-вакуумного азотирования при 530 °C в течение 60 минут.
12. Разработанные технологии были использованы ЗАО «Имплантат МТ» при производстве элементов эндопротезов тазобедренного сустава.
Список литературы
- Иголкин А.И. «Титан в медицине» УДК 669.295,61
- Кузьменко В.В., Фокин В. А. Ортопедия, травматология и протезирование 1991, № 10, с. 74−78.
- Scinemann S.G., Perren S.M., Titanium alloys as metallic biomaterials Proc. Of the fifth world conf. on titanium 1984, v.2, p. 1327-' 1334.
- Tateishi Tekuya, Kinzoki 1989,№ 1, v. 59, p.33−37.
- Титан: совместное издание. Прогр. ООН по окружающей среде (Пер. с англ.) М.: Медицина 1986.
- Kononen М. and Kivilanti J. An application of the titanium-alumina system for prosthetic dentistry-Proc. Of the sixth world conf. on titanium 1988, v.l. p. 541−544.
- Minoru Okada, Hisushi Mitsuya, Isamu Katod, Superplastik forming of Ti6A14V denture base-Seventh world conf. on titanium. Abstr. Prog. San-Diego, TDA. 1992, p. 184.
- Рогожников Г. И., Немировский М. Б., Шаров T.B., Белховский М. А., Сплавы титана в ортопедической стоматологии. Пермь. Книжное изд-во 1991.
- Firoze Е. Katak, Servi I.S., Agarwal J.C. JOM, 1991, v.43. № 7,p.30.
- Matsushita Т., Nishimura T. Titanium alloy wire for reattachment of bones- Seventh world conf. on titanium., Abstr. Prog. San-Diego, TDA. 1992, p. 184.
- Трение изнашивание и смазка // Справочник, Москва: Машиностроение 1978, т.1,с.399.
- Crowninshield R., Price Н., Parr J., Gilbertson L., Lower J., Shetty R.: Hardness abrasion resistance and particulate release from metallic implant surfaces. Trans of 37th Ann. Meet of Orthop. Soc. Abaheim 1991. P. 91.
- Гаркунов Д.Н. Триботехника. M.: Машиностроение, 1989, с. 242.
- Д.У. Дини «Лазерная модификация поверхности покрытий, нанесенных электроосаждением, физическим осаждением из паровой фазы и плазменным распылением.», Калифорния, стр. 41.
- Модифицирование и легирование поверхности лазерными, ионными и электронными пучками. (Под редакцией Дж. М. Поута)., М. Машиностроение, 1987, 424.
- Григорянц А.Г., Сафонов А. Н., «Лазерная техника и технология» Кн. 3 Методы лазерной обработки., М., Высшая школа., 1987, ст. 191.
- Григорянц А.Г., Сафонов А. Н., «Лазерная техника и технология» Кн. 6. Основы лазерного термоупрочнения сплавов. М., Высшая школа, 1988, 156.
- Колачев Б.А., Габидуллин P.M., Питузов Ю. В. «Технология термической обработки цветных металлов и сплавов», М., Металлургия, 1992, ст. 272.
- N.E.W. Hartley, Wear, 34, 1975, 427.
- G. Dearnaley and N.E.W. Hartley, Thin Solid Films, 54, 1978, 215.
- G. Dearnaley, Radiat. Eff., 63, 1982, 1.
- H.Herman, Nucl. Instrum. Methods, 182−183, 1981, 887.
- J.K. Hirvonen, J. Vac. Sci. Technol., 15, 1978, 1662.
- L. Singer, R.N. Bolster and C.A. Carosella, Thin Solid Films, 73, 1980,283.
- S. Lo Russo, P. Mazzoldi, I. Scotoni, C. Tosello and S. Tosto, Appl. Phys. Lett., 34(10), 1979, 627.
- F. -Z. Cui, H.-D. Li and X.-Z. Zhang, Nucl. Instrum. Metods, 209−210, 1983, 881.
- J.B. Pethica, in V. Ashworth (ed.), Ion Implontation into Vetals, Pergamon, Oxford, 1982, p. 147.
- C.A. Dos Santos, B.A.S. de Barros, Jr., J.P. de Souza and I.J.R. Baumvol, Appl. Phys. Lett., 41(3), 1982, 237.
- K.Hohmuth, B. Rauschenbach, A. Kolitseh and E. Richter, Nucl. Instrum. Metods, 209−210, 1983,249.- 16 030. Т. Barnavon, J. Tousset, S. Fayeulle, P. Guiraidenq, D. Treheux and M. Robelet,
- Radiat. Eff., 77, 1983, 249.
- Buchanan R.A., Rigney E.D., Williams J.M.: Ion implantation of surgical Ti6A14V for improved resistance to wear-accelerated corrosion. J. Biomed. Mater. Res.2I: 355, 1987.
- Mekellop H. And Rostlunl N.: The wear behavior of ion-implanted Ti6A14V against HMWPE. J. Biomed. Mater. Res.24: 1413, 1990.
- С. Файель Трибологические характеристики материалов, имплантированных азотом, Лион, 1986, с. 12.
- Леонидова М.Н., Шварцман Л. А., Шульц Л. А. «Физико-химические основы взаимодействия металлов с контролирующими атмосферами» М. Металлургия, 1980, 264.
- Yu, H.-D. Li, X.-Z. Zhang and J.-H. Tian, Nucl. Instrum. Metods, 209−210, 1983, 1063.
- N. Bolster and I.L. Singer, ASLE Trans., 24(4), 1981, 526.
- S.illich, R.N. R. N. Bolster and I.L. Singer, in G.K. Hubter, O. W. Holland, C.R.Clayton and C.W.White (eds.), Ion Implontation and Ion Beat Processing of Materials, Elsevier, Amsterdam, 1985, p. 637.
- L.E.Pope, F.G.Yost, D.M.Follstaedt, S.T. Picraux and J.A.Knapp, in G. K. Hubler, O.W.Holland, C.R. Clayton and C.W.White (eds.), Ion Implontation and Ion Beat Processing of Materials, Elsevier, Amsterdam, 1985, p. 681.
- L.Singer, in G. K. Hubler, O.W.Holland, O.W.White, C.R. Clayton and C.W.White (eds.), Ion Implontation and Ion Beat Processing of Materials, Elsevier, Amsterdam, 1985, p. 585.
- L.Singer, Appl. Surf., Sci., 18. 1984, 28.
- L.Singer, Vacuum, 34, (10−11), 1984, 853.
- J.F. Coplin, Proc. Int. Conf. Designing with Titanium, Bristol, 1986, p. 11.
- R.I. Jaffee, Proc. Int. Conf. Designing with Titanium, Bristol, 1986, p. 28.
- J.A. Hall, Proc. 6th World Conf. Titanium, Cannes, 1988, part 1, p. 1.
- T.W. Farthing, Proc. 6th World Conf. Titanium, Cannes, 1988, part 1, p.37.
- Y. Iton, A. Iton, H. Azuma, T. Hioki «Improving the tribological properties of Ti-6A1−4V alloy by nitrogen-ion implantation», Surface and Coatings Technology 111, 1999, p. 172−176.
- P. Sioshansi, J. Met. 42 (1990), 30.
- F. Pons, J.C. Pivin, G. Farges, J. Mater. Res. 2, 1987, 580.
- J.T. Elber, R. Thamburaj, P.C. Patnaik, Int. Mater. Rev. 33, 1988, 289.
- S.Saritas, R.P.M. Procter, W.A. Grant, Mater. Sci. Eng. 90, 1987, 297.
- E.Ma, J.J. Li, H.D. Li, Surf. Coat. Technol.37, 1989, 31.
- R. Hutchings, W.C. Oliver, Wear 92, 1983, 143.
- A.Chen, X. Qiu, J.R. Conrad, R.S.Dodd, F. Worzala, J. Blanchard, J. Mater. Eng. 12,1990,299.
- Nath, D.K. Sood, R.R. Manoiy, Nucl. Instrum. Meth. B5960, 1991, 946.
- V.C. Nath, D.K. Sood, R.R. Manoiy, Surf. Coat. Technol. 49, 1991, 510.
- Cui, A.M. Vredenberg, F.W. Saris, Appl. Phys. Lett. 53, 1988, 2152.
- Виноградов Ю. M. Трение и износ модифицированных металлов. М.: Наука, 1972. 151 с.
- Титан. // МиТОМ /Тр. Ill Международной конф. по титану. М.: ВИЛС, 1978. Т. 2. с. 738.
- Горынин И. В. Чечулин Б.Б. Титан в машиностроении М.Машиностроение, 1990. с. 400.
- Гельтман И. С., Рогов И. В., Паньков В. И., //Трение и износ. 1985. Т. 6, № 1. С. 167−170.
- Кудинов В. В. Плазменные покрытия. М.: Наука, 1977. 184 с.- 16 262. Чечулин Б. Б., Ушков С. С., Разуваева И. Н., Гольдфайн В. Н. Титановыесплавы в машиностроении. JI. Машиностроение, 1977. 248 с.
- Анитов И. С., Максимова А. Г., Щербакова 3. В. //Химикотермическая обработка сталей и сплавов. Л.:Дом техники, 1961. С 3−16.
- Клабуков А. Г., Зуев А. М.//Известия ВУЗов. Сер. Машиностроение. 1974. № 3. С. 120−124.
- Рубцова 3. С., Сентюрихина JI. П., Никоноров Е. М. И др.// Вестник машиностроения. 1982. № 5. 44с.
- Шашков Д. П., Виноградов А. В., Полохов В. Н. // Изв. АН СССР: Металлы: 1981, № 6. С. 172−177.
- Брискина Н. Г., Кенина Е. М., Туманова Т. А. И др. // Защита металлов, 1983. Т. 19 № 1.С. 61−64.
- Minhell Е., Brotherton P. J. Inst Metals. 1965. V/ 93, N 11. P. 381−386.
- Titanium Science and Technology/ Proc. Of the fifth Intern: Conf. on titanium. Congress-Center/ Munich: FRG/ September 10−14. 1984. V. 1−4. Edited by G. Lutjering. U.Zwicrer. W. Bunk, v., II, p. 973, 367.
- Арзамасов Б.Н., Братухин А. Г., Елисеев Ю. С., Панайоти Т. А. Ионная химико-термическая обработка сплавов // М.: Издательство МГТУ им Н. Э. Баумана, 1999. 400с.
- Арзамасов В.Н., Громов В. И., Сосков М. Д. Влияние режимов ионного азотирования на структуру и свойства титановых сплавов // Металловедение и термическая обработка металлов. 1996. № 5. С. 26−28.
- Шашков Д.П. Влияние азотирования на механические свойства и износостойкость титановых сплавов // Металловедение и термическая обработка металлов. 2001. № 6. С. 20−26
- Бокштейн С.З. Диффузия и структура металлов. М.: Металлургия, 1973. 206с.
- Titanium Nitrogen Phase Diagram and Diffusion Phenomenal. E.Etchessahar., I.P. Bars., J. Debuigne.// Proc. 5-th., Int. Conf. on Titanium, Titanium science and teehnology. Munich, 1984, V.3., p. 1423−140.
- Кипарисов С. С., Левинский Ю. В. Азотирование тугоплавких металлов. М. Металлургия, 1972. 160 с.
- Панайоти Т.А., Соловьев Г. В. Ионное азотирование а- и а+(3-сплавов титана // Вестник МГТУ. Сер. Машиностроение. 1994. № 1. С. 15−24.
- Арзамасов Б.Н., Братухин А. Г., Елисеев Ю. С., Панайоти Т. А. Ионная химико-термическая обработка сплавов // М.: Издательство МГТУ им Н. Э. Баумана, 1999. 400с.
- Wasilewski R.J., Kehl I. Diffusion of nitrogen and oxygen in titanium // J. of the Inst. Of Metals. 1954/55. № 83. P. 94−104.
- Боровлева H.H., Велищанский A.B., Теплов B.C. Ионное насыщение титановых сплавов азотом и кислородом // Труды МВТУ /Под ред. Арзамасова М.: МВТУ, 1987. С. 54.
- Кофстад П. Высокотемпературное окисление металлов. М.: Мир, 1968. 96с.
- Metin Е., Osmal Т. Kinetics of the Layer Growth and Multiphase Diffusion in Ion-Nitrided Titanium // Met. Trans. 1989. V. 20A. P. 1819−1832.
- Панайоти Т.А. Азотирование высокопрочных сталей и сплавов в тлеющем разряде. М.: Машиностроение. 1989. 40с.
- Ильин А.А., Бецофен С. Я., Скворцова С. В. и др. Структурные аспекты ионного азотирования титановых сплавов // Металлы. 2002. № 3. С.6−15.
- Диссертация Давыдовой Г. С. Москва, 2001 г.
- Колачев Б.А., Ливанов В. А., Елагин В. И. Металловедение и термическая обработка цветных металлов и сплавов. М.: Металлургия. 1981. с. 416.- 16 486. Носова Г. И. Фазовые превращения в сплавах титана М.: Металлургия. 1968.с. 181.
- Новиков Е.Н., Лужников Л. П., Кононова В. Ф. Влияние легирования на процесс азотирования титана и его сплавов // Легирование и термическая обработка титановых сплавов под ред. Туманова А. Т., Глазунова С. Г., Хорева А. И., М., 1977, с.89−96.
- Панайоти Т.А., Соловьев Г. В. Особенности диффузионных слоев при ионном азотировании а- и (а+р)-титановых сплавов в интервале температур от 500 до 1000 °C // Металловедение и термическая обработка металлов. 1994. № 5. С. 34−37.
- Дьякова М.А., Богачев И. Н. ФММ, 1960, т. 10, вып. 6, с. 896.
- Сидорин И.И. и др. Научные доклады высшей школы, серия «Машиностроение», 1959, № 2, с. 120.
- Смирнов А.В., Начинков А. Д. Азотирование титана при пониженном парциальном давлении азота // МиТОМ. 1960. № 7. с.42−47.
- Лахтин Ю.М., Коган Я. Д., Шпис Г. И., Бемер З. М. Теория и технология азотирования, М., Металлургия, 1991, с. 319.
- Панайоти И.А., Соловьев Г. В. Ионное азотирование стареющих (а+Р)-сплавов титана // МиТОМ. 1996. № 5. С.28−31.
- Hempel М. Draht. 1965. Bd 16, N 4. S. 209−218.
- Борискина Н. Г., Гуревич С. Е., Единович Л. Д. // МиТОМ. 1980. № 10. С. 45.
- Mitchell Е. and Brotherton P.J. //Journal of Institute of Metals 93, 1964−65, p. 381.
- Bell Т., Bergmann H.W., Lanagan J., Morton P.H. and Staines A.M. // Surface Engeneering 2, 1986, p. 133/
- Lanagan J., Morton P.H. and Bell T. // Des Titan, 1986, p. 136.
- Morita Т., Shimizu M., Kawasaki K. // Proceedings of KSME/JSME Joint Conference on Fracture and Strength'90, 1990, p. 67.
- Morita Т., Fuchikawa S., Komotori J., Shimizu M., Minakawa K., Kawasaki K. // Fatigue strength of nitrided high-strength titanium alloys / Proc. 10-th Int. Conf. On Titanium, Titanium Science and technology. Hamburg, 2003. P. 941−948.
- Ливанов B.A., Буханова A.A., Колачев Б. А. Водород в титане. М.: Металлургиздат. 1962. 245с.
- Коростелев П.П. Лабораторные приборы технического анализа. Справочник. М., Металлургия. 1987. с. 115−117.
- Назимов О.П., Буханова А. А. Спектральное определение водорода в металлах. Журнал прикладной спектроскопии. 1977. т.27. с.963−973.
- Методическая рекомендация. Качественный и количественный рентгеновский анализ фазового состава титановых сплавов. ВИЛС, MP 18−36/СМИ-75. 1975. с. 39.
- Методическая рекомендация. Измерение параметров решетки титановых сплавов. ВИЛС. МП 30−26−70. 1970. 19.
- Методы испытания, контроля и исследования машиностроительных материалов / под ред. Туманова А. Т. Том 2. Методы исследования механических свойств металлов. М.: Машиностроение, 1974, 320 с.
- Гаврюшенко Н.С. Методика исследования качества узлов трения эндопротезов тазобедренного сустава человека. VI съезд травм, и ортоп., 9−12 сент.1997, Н. Новгород, тезисы докл., с. 537.
- Джонсон Н., Лион Ф./ Статистика и планирование эксперимента в технике и науке, т.1. Методы обработки данных. М. Мир. 1980. С. 512.
- Авиационные материалы. Справочник под ред. Туманова А. Т. ОНТИ-1973.585с.
- Ш. Борисова Е. А., Бочвар Г. А., Брун М. Я. и др. Титановые сплавы. Металлография титановых сплавов. М: Металлургия. 1980 г. 464с
- Ильин А.А. Механизм и кинетика фазовых и структурных превращений в титановых сплавах. М. Наука. 1994. 304с.
- Rosenblum М.Е., Smith P.R., Froes F.N. Microstructural of superplastic forming of titanium alloys // Proc. Fifth Inter. Conf. on Titanium. Titanium'80, Science and Technology. Kyoto, Japan, 1980. pp. 1001−1014.
- Ильин A.A., Скворцова C.B., Лукина E.A., Карпов В. Н., Поляков О. А. Низкотемпературное ионное азотирование имплантатов из титанового сплава ВТ20 в различных структурных состояниях // Металлы. № 2. 2005, с. 38−44.