Технологическое обеспечение прочности профильных неподвижных соединений упругопластическим деформированием элементов соединения
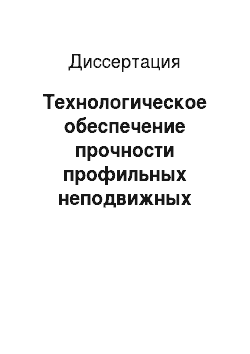
Вторая глава посвящена разработке методики аналитического определения прочности ПНС, имеющего заданный профиль, дано обоснование вида предлагаемого профиля, предложена технология его формообразования. Приведена методика расчета геометрических параметров и режимов формообразования профиля на основе теоретических расчетов и оценок. Приведена методика определения минимальной толщины сечения профиля… Читать ещё >
Содержание
- ВВЕДЕНИЕ. .. .. .. ... .'
- 1. АНАЛИТИЧЕСКИЙ ОБЗОР И ПОСТАНОВКА ЗАДАЧИ КОНСТРУКЦИОННО-ТЕХНОЛОГИЧЕСКОГО ОБЕСПЕЧЕНИЯ ПРОЧНОСТИ ПРОФИЛЬНЫХ СОЕДИНЕНИЙ
- 1. 1. Конструктивные особенности и существующие методы обеспечения требуемой прочности неподвижных соединений с натягом в изделиях машиностроения
- 1. 2. Методы обеспечения прочности неподвижных соединений применением эффективных способов сборки
- 1. 3. Обоснование прочности соединений с натягом
- 1. 4. Физико-механические свойства поверхностного слоя металла
- 1. 5. Виды и основные параметры рельефа поверхности. .38 1. б Выбор полного натяга при деформирующем протягивании
Технологическое обеспечение прочности профильных неподвижных соединений упругопластическим деформированием элементов соединения (реферат, курсовая, диплом, контрольная)
Ускорение научно-технического прогресса непрерывно связано с разработкой и внедрением новых прогрессивных технологий для производства высокоэффективной техники нового поколения. Использование высокоскоростных и супермощных машин ведет к необходимости обеспечить высокую надежность работы как отдельных узлов, так и машины в целом. Работоспособность и надежность неподвижных соединений определяется в первую очередь их прочностью, то есть способностью элементов сопротивляться их относительному смещению в процессе эксплуатации и несущей способностью самих элементов.
Повышение прочности неподвижных соединений часто связано с увеличением материалоемкости конструкции. В то же время, для повышения своей конкурентоспособности современные предприятия вынуждены внедрять ресурсосберегающие технологии, которые наряду с повышением прочности и работоспособности деталей машин и конструкций обеспечивают снижение материалоемкости изделий.
В связи с этим большое значение приобретает решение проблемы обеспечения прочности деталей машин и их соединений технологичным способом при одновременном снижении материалоемкости изделия.
Успешное решение названной проблемы открывает возможности повышения технического уровня и эффективности использования различных неподвижных соединений, в том числе и подшипников скольжения, ставшими неотъемлемой частью многих современных машин и приборов.
Опыт эксплуатации и исследования многих отечественных и зарубежных ученых в области повышения несущей способности неподвижных соединений, выполненные в последние десятилетия, показывают, что на прочность неподвижных соединений большое влияние оказывают геометрические параметры сопрягаемых поверхностей, их физико-механические свойства, а также метод сборки соединения. К настоящему времени опубликовано большое количество зарубежных и отечественных работ [7, 12, 13, 17 19, 24, 35, 50, 70, 75, 82, 91, 96, 97 и др.], посвященных прочности профильных неподвижных соединений и методам формирования профиля, а также связанному с этим изменению структуры и физико-механических свойств поверхностного слоя. Предлагаемые на сегодняшний день решения, как правило, относятся к частным случаям, поэтому дальнейшее накопление экспериментальных данных, изучение особенностей влияния различных факторов на прочность неподвижных соединений имеет важное научное значение.
Ужесточение требований к материалоемкости изделий стимулировало развитие новых методов обеспечения прочности ПНС. Одним из перспективных путей решения проблемы прочности является метод повышения прочности за счет образования профиля в неподвижных соединениях уп-ругопластическим деформированием одного из сопрягаемых элементов при заданном макрорельефе поверхности другого элемента. При этом непосредственное прикладное значение имеет разработка режимов формообразования профиля, их оптимизация для изделий конкретного назначения.
Все это предопределило направление настоящего исследования, основной целью которого является исследование зависимости влияния геометрических параметров на прочность ПНС, разработка рекомендаций по оптимальному их применению и выбору режимов обработки, расчет минимальной толщины стенки охватываемого элемента .
В диссертации представлены результаты исследования влияния параметров профиля соединения, а также толщины сечения охватываемого элемента на прочность соединения, приведен алгоритм выбора оптимального соотношения конструктивных параметров соединения при заданных эксплуатационных нагрузках, выявлена взаимосвязь параметров профиля и режимов его формирования, даны рекомендации по выбору вида рельефа и назначению режимов обработки.
В качестве объекта исследования выбрано цилиндрическое профильное неподвижное соединение, где пластичность одного элемента значительно превышает пластичность другого — подшипник скольжения, один из элементов которого выполнен в виде толстостенной втулки или корпуса сложной формы из конструкционной стали, другой в виде тонкостенной втулки из сплава на основе меди. Научная новизна работы заключается в следующем:
1. Выявлена закономерность влияния основных конструктивных и технологических факторов ПНС на его прочность;
2. Предложена методика расчета параметров профиля ПНС с минимальной толщиной сечения охватываемого элемента, а также их оптимизация с целью увеличения производительности и уменьшения материалоемкости изделия;
3. Предложена методика расчета режимов упругопластиче-ского деформирования при формировании профиля на поверхности одного из элементов и сборке ПНС. Практическая ценность работы заключается в разработке ПНС с различными конструктивными особенностями, позволяющими снизить материалоемкость соединенияв разработке высокопроизводительной ресурсосберегающей технологии обеспечения прочности ПНС, позволяющей исключить дорогостоящие финишные операции, совместить механическую обработку и сборку деталейв разработанных и доведенных до удобной и наглядной формы программах, позволяющих рассчитать параметры профиляв использовании разработанных технологических процессов и программ в учебном процессев разработке технологической оснастки для реализации технологического процесса образования рельефа на поверхности охватывающего элемента ПНС.
Результаты выполненной работы изложены в настоящей диссертации, состоящей из введения, четырех глав, общих выводов и списка литературы.
В первой главе представлен аналитический обзор исследований, посвященных прочности неподвижных соединений, выявлены факторы, влияющие на прочность НС, и характер их влияния, сформулированы и обоснованы направление исследования, научные и практические задачи.
Вторая глава посвящена разработке методики аналитического определения прочности ПНС, имеющего заданный профиль, дано обоснование вида предлагаемого профиля, предложена технология его формообразования. Приведена методика расчета геометрических параметров и режимов формообразования профиля на основе теоретических расчетов и оценок. Приведена методика определения минимальной толщины сечения профиля охватываемого элемента соединения .
В третьей главе приведены результаты теоретических расчетов и экспериментальных данных зависимости несущей способности элементов соединения от геометрических параметров профиля. Изложена методика экспериментального исследования. Проведен анализ сходимости теоретических и экспериментальных данных и оценка достоверности полученных результатов.
Четвертая глава содержит результаты разработки технологии обеспечения прочности профильных неподвижных соединений, практические рекомендации по выбору параметров профиля, алгоритм расчета конструктивных параметров охватывающего элемента соединения. Предложена методика назначения режимов формирования рельефа на сопрягаемой поверхности охватываемого элемента ПНС.
В настоящей работе автор защищает:
1. Экспериментальные зависимости прочности профильных неподвижных соединений от геометрических параметров профиля.
2. Новую технологию обеспечения прочности профильных неподвижных соединений с уменьшением материалоемкости изделия, позволяющую увеличить коэффициент использования материала дорогостоящей тонкостенной втулки до 80 -100%.
3. Методику выбора оптимальных геометрических параметров профиля и методику определения минимальной толщины сечения профиля охватываемого элемента соединения.
Основные результаты исследований докладывались на региональной научной конференции студентов, аспирантов и молодых ученых (г. Новосибирск, 2001 г.), конференции «Транссибвуз 2000» (г. Омск, 2000 г.), а также на семинарах кафедр «Технология машиностроения», «Металлорежущие станки и инструменты» и «Сопротивление материалов». Работа выполнена на кафедре «Технология машиностроения» Омского государственного технического университета.
ОБЩИЕ ВЫВОДЫ И РЕЗУЛЬТАТЫ.
1. Разработан технологический метод обеспечения требуемой прочности путем создания заданных отклонений формы с дальнейшим заполнением их в процессе пластического деформирования.
2. Способность соединения сопротивляться относительному смещению в значительной мере зависит от геометрических параметров профиля и созданного натяга на цилиндрических участках профиля.
3. Конструктивными факторами, оказывающими наибольшее влияние на прочность ПНС, являются диаметр индентора, высота профиля, шаг винтовых впадин.
4. На основе закономерностей формирования профиля ПНС и результатов экспериментальных исследований разработана методика обеспечения прочности ПНС с уменьшением материалоемкости изделия.
5. Установлен характер изменения прочности ПНС в зависимости от параметров профиля.
6. Уравнение регрессии, полученное по результатам многофакторного эксперимента, как функция отклика, позволяет определить область оптимального сочетания глубины накатывания и шага винтовых впадин, обеспечивающих требуемое значение параметра оптимизации — прочности ПНС.
7. Сравнительными испытаниями образцов подшипников скольжения изготовленными по серийной технологии и с использованием предлагаемой технологии, показано, что последняя обеспечивает повышение прочности ПНС в 2 -2,5 раза и (или) снижение материалоемкости в 1,3 — 2 раза.
Список литературы
- A. с. 12 98 032, СССР. Способ изготовления неразъемных соединений деталей/ Кравченко Ю. Г., Ворохов A.A. //Открытия. Изобретения. 1987. -№ 11.
- А.с. 1 488 176 СССР, МКИ4 В 23 Р 11/02. Способ соединения охватываемой и охватывающей деталей/Беляев В.А., Комаров С. С., Голубев В. Н. и др. //Открытия. Изобретения. 1989. -№ 23.
- Акименко Ю.А. Исследование процесса дорнования отверстий тонкостенных деталей в обойме. Автореферат диссертация на соискание учёной степени КТН. Брянский политехнический институт, 1975.
- Андреев Г. Я. Тепловая сборка колесных пар. Харьков: Харьковского университета, 1965. 227 с.
- Андреев Г. Я., Шатько И. И. Распределение контактных давлений в- напряженных посадках // Вестник машиностроения, 1967. -№ 5. С. 36−38.
- Андреев Ю. В. Миндрул О. Б. Технология повышения качества прессовых соединений дорнованием // Новые технологические процессы и оборудование для поверхностной пластической обработки материалов. Тезисы докладов. Брянск, 1986, С. 63.
- Аскинази Б.М. Упрочнение и восстановление деталей машин. Чистовая обработка поверхности металла с подогревом. М.: Машиностроение, 1989. 200 с.
- Аскинази Б.М. Упрочнение и восстановление деталей машин электромеханическим методом. М. Л., Машгиз, 1961.
- Безъязычный В.Ф., Кожина Т. Д. К вопросу технологического обеспечения прочности прессовых соединений // Оптимизация операций механической обработки. Ярославль, 1986. -С. 51−55.
- Беляев Н.С., Ильяшенко A.A. О взаимозаменяемости конических соединений с натягом. — Технология и организация производства, 1974, № 5, с. 33—35.
- Беляев Н.С., Ильяшенко A.A., Михайленко Л. Ф. Перспективы применения абразивных материалов для повышения статической прочности конических соединений. Труды московского автомеханического института. М.: 1975, вып. 5, с. 133 — 137.
- Берникер Е.И. Посадки с натягом в машиностроении. 1966. ч
- Бородин A.B., Волков В. М. Повышение несущей способности соединений с натягом // Прикладные задачи механики: Сб. науч. тр./ Под ред. В.В. Ев-стифеева. -Омск: ОмГТУ, 1997. -кн. 1. -с.17−20.
- Богоявленский К.Н., Рябинин А. Г., Кобышев А. Н. и др. Неразъемное соединение полых деталей высоким гидравлическим давлением // Кузн-штамп, пр-во. -1989. -№ 3. -С.24−26.
- Виноградов О.Г. Статическая прочность прессовых соединений с гальваническими покрытиями — Вестник машиностроения, 1966, № 3, с. 23—25.
- Воячек И.И. Расчет прочности соединений с натягом, собранных поперечным методом // Изв. вузов. Машиностроение. -1996. С. 15−15.
- Головатый А.Д., Проскуряков С. И. Технологическая обработка поверхностей и прочностьсоединений с натягом // Вестник машиностроения, 1972. № 4. С. 31−33.
- Горохов В.А. Двухуровневая регуляризация микрогеометрии технических поверхностей и ее обеспечение // Вестник машиностроения, 1994, № 5 с. 29 -32.
- Гречищев Е.С., Ильяшенко A.A. Опыт внедрения конических посадок с гарантированным натягом. — Вестник машиностроения, 1966, № 9, с. 27—30.
- Гречищев Е.С., Ильященко A.A., Соединение с натягом: расчёты, проектирование, изготовление. -М.: Машиностроение, 1981. 247с., ил.
- Дальский A.M. Технологическое обеспечение надёжности высокоточных машин. М.: Машиностроение, 1975. 223с.
- Демкин Н.Б., Рыжов Э. В., Суслов А. Г., Алексеев В. М. Оценка шероховатости и волнистости при расчете контактного взаимодействия деталей машин // Вестник машиностроения. 1975. № 8. С. 27—29.
- Демкин Н.Б., Рыжов Э. В. Качество поверхности и контакт деталей машин. М., 1981. 244 с.
- Демкин Н.Б. Контактирование шероховатых поверхностей. М.: Наука, 1970. 227 с.
- Детинко Ф.М., Фастовский В. М. Посадка короткой втулки на цилиндрическую оболочку // Вестник машиностроения, 1967.- № 7. -С. 42−45.
- Ефремов В.В., Наумов В. А., Чурсин A.A. Теория и практические вопросы работоспособности элементов машин, приборов и аппаратуры. Иркутск: Изд-во Иркут. ун-та, 1984. — 220с.
- Житницкий С. И. Андрейчиков О.С. Инструмент для накатывания резьбы в отверстиях «Станки и инструмент», M, 1965, № 10.
- Зенкин A.C., Арпентьев Б.M., Козелло H.A., Оборский И.Jl. Технологическое обеспечение точности сборки соединений с натягом осуществляемым с термовоздействием. // Вестник машиностроения. 1988 -№ 10. -С.43−45.
- Ильяшенко A.A. Расчет прочности конических посадок с учетом погрешностей изготовления. — Труды МИИТа. M Транспорт, 1967, вып. 241, с. 6071.
- Ильяшенко A.A., Ноткин B.C. Работа посадок с натягом при передаче осевых усилий. — Труды Московского автомеханического института. Вопросы транспортного машиностроения, М.: 1975, вып. 5, с. 138−143.
- Иоселевич Г. Б., Лукащук Ю. В. Распределение напряжений в соединении с гарантированным натягом // Вестник машиностроения, 1979 № 6. -С. 25−26.
- Иоселевич Г. Б. Детали машин: Учеб. для вузов. -М.: Машиностроение, 1988. 367 с.
- Кацев П.Г. Обработка протягиванием. Справочник. М.: Машиностроение. 1986. — 272., ил.
- Киричек П. А. Способ получения неподвижных соединений.// Машиностроитель. 1994, № 10.
- Клевакин B.C. Исследование прочности соединений с автофретированными охватывающими деталями и разработка метода их расчета. Автореферат дисс. На соиск. уч. степ. канд. техн. наук, Пермь, 1978.
- Ковалевский В.Ф., Наумов В. А. Применение рельефа, полученного капельно-адгезионной технологией // Проблемы машиностроения и металлообработки. Сб. трудов. /Под ред. В. А. Наумова, В.В. Евсти-феева, ОмПИ. -1992. -С. 90−92.
- Коновалов Е.Г., Лобачевский И.С. Ротационное дорнирование АН СССР, Минск, 1959
- Косилова А. Г. Отделочная обработка внутренних поверхностей пластическим деформированием // Прогрессивные методы изготовления, отделка и упрочнение металлических деталей пластическим деформированием. М.: Машгиз, 1962. -С. 154−161.
- Лукашевич Г. И. Прочность прессовых соединений с гальваническими покрытиями. Киев: Гостехиздат, 1961, 61с.
- Максак В.И., Советченко Б. Ф. Определение прочности соединений с натягом по их диссипатив-ным свойствам — Вестник машиностроения, 1975, № 12, с. 29−30.
- Масягин В. Б. Исследование прочности профильных неподвижных неразъемных соединений: Дисс. канд. техн. Наук.:01.02.Об / ОмГТУ. Омск, 1999. — 288 с.
- Марьяновский М.М., Вагман А. Я. Посадки холодом. Обмен трудовым опытом. Труды всесоюзного про-ектно-технологического института тяжелого машиностроения. М.: 1958. 55 с.
- Михайленко JI. Ф. Исследование влияния технологической подготовки сопрягаемых поверхностей на прочность соединений, осуществляемых с применением глубокого холода. Автореф. дисс. на соискание уч. степ. канд. техн. наук. Киев: КТИЛП, 1975, 26 с.
- Монченко В.П. Дорнование отверстий в длинных гильзах М., НИИ Автопром, 1967.
- Монченко В.П. Эффективная технология изготовления полых цилиндров. М.: Машиностроение, 1980. — 24 8с., ил.
- Моргунов А. П Технологическое обеспечение прочности профильных неподвижных соединений накатыванием. // Механика процессов и машин: Сб. науч. тр. Омск. 2000. С. 27−29.
- Технологическое обеспечение прочности профильных неподвижных соединений деформирующим протягиванием. // Прикладные задачи механики: Сб. науч. тр. Омск. 2003. С 16−19.
- Моргунов А.П. Разработка и обеспечение прочности профильных неподвижных неразъемных соединений. Автореферат дисс. на соиск. уч. степ, доктора техн. наук. Омск, 1998. -38 с.
- Новиков М.П. Основы технологии сборки машин и механизмов. М.: Машиностроение, 1980. -592 с.
- Некоторые вопросы усталостной прочности прессового соединения вал-втулка/Л. П. Савченко, В.
- В. Сумцов, M. Л. Туровский и др.— Проблемы прочности, 1975, № 2, с. 90−93.
- Николаев В.А., Гадецкий Ю. Л., Белецкий В. В., Пименов А. Ф., Трайно А. И. Формирование прессовых соединений повышенной сложности // Вестник машиностроения, 1997, № б, с. 38—39.
- Николаев В.Д., Штриков Б. Л. Ультразвуковая запрессовка деталей // Вестник машиностроения, 1994, № 8, с. 24−26.
- Ноткин B.C. Повышение работоспособности посадок с натягом в тепловозостроении. — Труды Московского автомеханического института. Вопросы транспортного машиностроения. М.: 1975, вып. 5, с. 144−152.
- Обработка поверхностей и прочность соединений с натягом. — Вестник машиностроения, 1972, № 4, с. 31−33.
- Объемное дорнование отверстий. / Технология упрочняюще калибрующей и формообразующей обработки металлов. Справочное пособие. М.: Машиностроение, 198 9.
- Папшев Д. Д Отделочно упрочняющая обработка поверхностным пластическим деформированием. М., 1978. 151 с.
- Пинегин C.B. Контактная прочность к сопротивлению качения. М.: Машиностроение, 1969.
- Повышение несущей способности конических соединений с натягом путем оксидирования деталей / Г. А. Бобровников, Н. С. Беляев, А. А. Ильяшенко, Л.
- Ф. Михайленко — Вестник машиностроения, 1977, № 8, с. 58−61.
- Проскуряков Ю.Г. Выбор смазки для дорнования цилиндрических отверстий. ВИНИТИ, тема № 6, № М-59−251/9, М., 1959.
- Проскуряков Ю.Г., Меньшаков В. М. Методика выбор режимов при накатке деталей шариками или роликами. «Вестник машиностроения», 1962, № 11.
- Проскуряков Ю.Г., Поздякова И. В. Повышение износостойкости поверхностей дорнованием. «Вестник машиностроения», 1963, № 9
- Проскуряков Ю.Г., Романов В. Н., Исаев А. Н. Объемное дорнование отверстий. М.: Машиностроение, 1984. -224 с.
- Проскуряков Ю.Г. Зависимость точности обработанных дорнованием отверстий от некоторых технологических факторов. «Вестник машине строения», 1961, № 4.
- Проскуряков Ю.Г. Технология упрочняюще-калибрующей и формирующей обработки металлов. М.: Машиностроение, 1971. 208 с.
- Проскуряков Ю.Г., Меньшаков В. М. Микрогеометрия поверхности при обработке деталей упрочняющекалибрующими методами «Вестник машиностроения», М, 1961, № 8.
- Розенберг A.M., Розенберг O.A. Механика пластического деформирования в процессе резания и деформирования протягиванием. М.: Машиностроение, 1979.
- Розенберг A.M. Обработка отверстий твердосплавными выглаживающими протяжками. М.: Машиностроение, 1976.
- Рыжов Э.В. Технологическое управление геометрическими параметрами контактирующих поверхностей // Расчетные методы оценки трения и износа. Брянск: 1975, с. 98−133.
- Саверин М.М. Соединение деталей с гарантированным натягом.// Детали машин т.1.
- Сервисен C.B., Когаев В. П., Шнейдерович P.M. Несущая способность и расчеты деталей машин на прочность. М.: Машиностроение, 1975.
- Соколовский А.П. Научные основы технологии машиностроения. M-J1., 1955. 515 с.
- Спиридонов A.A. Планирование эксперимента при исследовании технологических процессов. М.: Машиностроение, 1981.
- Суслов А. Г. Определение параметров опорной кривой и параметров функции распределения выступов по высоте // Вероятностно-статистические основы процессов шлифования и доводки JI., 1974, с. 85 -88.
- Суслов А.Г. Технологическое обеспечение контактной жесткости соединений. М., 1977. 100 с.
- Суслов А. Г. Выбор, назначение и технологическое обеспечение параметров шероховатости поверхностей деталей машин. М., 1979.
- Тимченко А.И. Профильные соединения валов втулок в машиностроении // Вестник машиностроения, 1981. № 1.-С. 33−37.
- Федоров Б.Ф. Гидропрессование с пластмассовыми компенсаторами при сборке — Технология и организация производства. 1974, № 5, с. 29—32.
- Феодосьев В.И. Избранные задачи и вопросы по сопротивлению материалов. М.: Наука, 1973, 400 с.
- Фролов Н.В., Цфайс Б. С. Теория цилиндрического соединения с натягом, нагруженного крутящим моментом — Изв. вузов. Машиностроение, 1973, № 9, с. 16−20.
- Цфас Б. С., Фролов Н. В. Распределение нагрузок по длине соединения, нагруженного крутящим моментом. — Изв. вузов. Машиностроение, 1974, № 10, с. 36−40.
- Хрущёв М. М., Беркович Е. С. Приборы ПМТ-2 и ПМТ-3 для испытания на микротвёрдость. М.: Академия наук СССР, 1950. 62 с.
- Школьник JI.M., Шахов В. И. Технология и приспособления упрочнения и отделки валов накатыванием. М., 1964.
- Шнейдер Ю. Г. Холодная бесштамповая обработка металлов давлением. М., изд-во «Машиностроение», 1967 .
- Шнейдер Ю. Г. Технология финишной обработки давлением: Справ. СПб.: Политехника, 1998. -413 с.
- Шнейдер Ю. Г. Эксплуатационные свойства деталей с регулярным микрорельефом J1.: Машиностроение, 1982. -248 с.
- Expandierwerkzend wurde verbessert // Maschinenmarkt. -1994. -100, № 51−52. С. 91.
- Kuhne Timm. Dnickfugetechnik- Alternative auch bei hohen Bean spru chunder // Blech Rohre Profile. -1995. -42, № 2 -C. 92−99.
- Verbindenger//Masch.-Anlag.+Verfanz. -1995, № 10. C.