Разработка высокоэффективных технологий продольно-прессового локализованного закрепления труб в трубных решетках
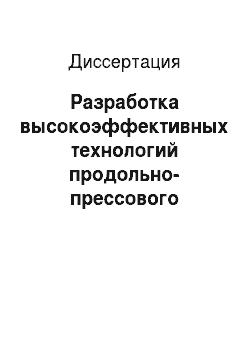
Автор настоящей работы выражают глубокую благодарность своему научному руководителю, заслуженному деятелю науки РФ, д.т.н., профессору Гречникову Ф. В. и коллективу кафедры ОМД СГАУ имени академика С. П. Королева за её активное обсуждениегенеральному директору ООО «Ремонтно-механический завод» Батраеву Г. А. и инженерно-техническим работникам данного предприятия, Ивановой И. С., Марты-новой Е… Читать ещё >
Содержание
- 1. Кожухотрубчатые теплообмеНные аппараты .г
- 1. 1. Элементы трубных пучков
- 1. 1. 1. Теплообменные трубы. г
- 1. 1. 2. Трубные решетки
- 1. 2. Механизм поперечно — прессового образования неразъ- ^ ёмных соединений
- 1. 2. 1. Стадии механизма Поперечно-прессового образований ^ неразъёмных соединений
- 1. 3. Существующие технологические процессы образованияq неразъёмных соединений
- 1. 3. 1. Механическая развальцовка
- 1. 3. 1. 1. Факторы, влияющие на качество вальцовочных соединений
- 1. 3. 2. Виды комбинированных соединений
- 1. 3. 3. Альтернативные технологии получения неразъёмных ^ соединений
- 1. 3. 3. 1. Импульсные методы образования неразъёмных со- 2g единений
- 1. 3. 3. 2. Образование неразъёмных соединений с использованием жидкости высокого давления
- 1. 3. 3. 3. Высокоскоростное деформирование клиновыми сегментами при образовании соединений
- 1. 3. 3. 4. Образование неразъёмных соединений с использо-о ванием операции дорнования
- 1. 3. 1. Механическая развальцовка
- 1. 1. Элементы трубных пучков
- 1. 4. Служебные характеристики неразъёмных соединений
- 1. 5. Мероприятия, направленные на повышение служебных 34 характеристик
- 2. 1. Анализ технологических возможностей при образовании ^ неразъёмных соединений
- 2. 2. Основные принципы продольно-прессового локализован- ^ ного образования неразъёмных соединений
- 2. 3. Конструкции трубных отверстий
- 2. 4. Разработка технологической модели
- 2. 4. 1. Стадия предварительного закрепления
- 2. 4. 1. 1. Внеконтактная деформация трубы на стадии пред- g5 варительного её закрепления в трубном отверстии
- 2. 4. 1. 2. Диаметр полости трубного отверстия
- 2. 4. 1. 3. Расчет геометрических размеров профилированной законцовки
- 2. 4. 1. 4. Расчет геометрических размеров кольцевой канавки
- 2. 4. 1. 5. Расчет длины кольцевого пояска
- 2. 4. 1. 6. Расчет длины образуемой контактной площадки при ^ осадке полотна трубы
- 2. 4. 1. 7. Заполнение кольцевой канавки
- 2. 4. 2. Окончательное закрепление
- 2. 4. 1. Стадия предварительного закрепления
- 2. 5. Оценка качества полученных неразъёмных соединений
- 3. 1. Методика изучения характера течения модельного мате- gg риала
- 3. 2. Металлографические исследования неразъёмных соеди- gg нений
- 3. 3. Качественная оценка осевых остаточных сжимающих на- qq пряжений ! — го рода
- 3. 4. Испытания неразъёмных соединений с повышенными ^ служебными характеристиками
- 3. 4. 1. Испытания на прочность неразъёмных соединений вы- ^ дергиванием трубы из трубной решетки
- 3. 4. 2. Гидравлические испытания неразъёмных соединений на плотность
- 3. 4. 3. Разработка методики ускоренных испытаний неразъёмных соединений, имитирующих действие коррозии во 101 внутренних слоях трубы
- 4. 1. Технологический процесс закрепления труб в трубных решетках № 1
- 4. 2. Технологический процесс закрепления труб в трубных решетках №
- 4. 3. Технологический процесс закрепления труб в трубных решетках №
- 4. 4. Оценка технико-экономической эффективности от внедрения в производство высококачественных технологий обра- 138 зования неразъёмных соединений
Разработка высокоэффективных технологий продольно-прессового локализованного закрепления труб в трубных решетках (реферат, курсовая, диплом, контрольная)
Развитие нефтеперерабатывающей, нефтехимической, судостроительной промышленности, атомного, энергетического машиностроения и так далее идет по пути создания мощных агрегатов и аппаратов (рис. 1), работающих в различных агрессивных средах. Надежность работы такого оборудования может быть обеспечена только при использовании для его создания самых прогрессивных технологических процессов обработки и сборки.
Рис. 1 — Нефтеперерабатывающая установка ЭЛОУ -11 (Новокуйбышевский НПЗ).
Кожухотрубчатые теплообменные аппараты, выпускаемые заводами химического машиностроения, являются самым распространенным видом (до 40% /1/ от общего веса) технологического оборудования (рис. 2).
При проектировании новой, изготовлении и ремонте существующей аппаратуры в условиях наращивания мощностей технологических установок (примерно в 4 раза за каждые 10 лет 121), основное внимание направлено на повышение эксплуатационного срока службы теплообмен-ных аппаратов и увеличения сроков межремонтных пробегов технологических линий в целом.
По данным нефтеперерабатывающей и нефтехимической промыш-ленностям убытки, связанные с простоем технологических линий в результате низкого качества закрепления труб в трубных решетках в 10−15 раз 131 превышают стоимость самих дорогостоящих (100 тыс. рублей/тонну и более) теплообменных аппаратов.
Рис. 2 — Блок теплообменных аппаратов нефтеперерабатывающей установки ЭЛОУ -11 (Новокуйбышевский НПЗ).
Усовершенствованию многие годы подлежат как конструкции сборок труб в трубных решетках, а также технологические процессы оборудования неразъемных соединений, так как, например, около 80% простоев теплообменной аппаратуры, изготовленной механической вальцовкой, вызвано разгерметизацией и коррозией труб в пределах вальцовочного пояска /4/.
Недостатки существующей большой разновидности технологических процессов закрепления труб в трубных решетках (механическая вальцовка, виброразвальцовка, гидропротягивание, запрессовка высоким гидравлическим давлением, запрессовка взрывчатыми веществами, электрогидравлическая запрессовка и так далее), даже при использовании доработанных конструкций сборок труб с трубными решетками, предопределяются неэффективностью положенного в их основу поперечно-прессового механизма образования соединений, когда:
1. требуемые характеристики прочности и плотности достигаются только на стадии совместной деформации трубы и трубной решетки, причем на достаточно большой площади контакта соединяемых элементов;
2. наличие микронеровностей на контактируемых поверхностях соединяемых элементов обусловливают необходимость использования высоких по уровню радиальных давлений, которые, в конечном итоге, вызывают коробление трубной решетки;
3. предусмотренные в трубном отверстии кольцевые канавки не заполняются материалом трубы;
4. коррозионная стойкость соединений труб с трубными решетками, как важнейшая служебная характеристика, не регламентирована техническими документами.
Рис. 3 — Трубные пучки перед их ремонтом (ООО «Ремонтно-механический завод» ЗАО НК ЮКОС — РМ).
Применение той или иной технологии закрепления труб в трубных решетках оправдано для определенных конструкций теплообменной аппаратуры, условий и требований её эксплуатации. Недостаточно обоснованный её выбор приводит к урону (аварии на Чернобыльской АЭС, АЭС «Хенфорд», «Тарапур» «Сан-онофр», «Милма», «Шипинг-лорт», на атомных подводных лодках «Морской волк» (США), «Комсомолец», на Самарском НПЗ в ноябре 1997 года), который невозможно оценить только в денежном выражении.
Вибрационные, ударные и другие знакопеременные нагрузки при одновременном воздействии высоких давлений, температур и высоких агрессивных сред обусловливают необходимость применения новых конструктивных решений в соединений труб с трубными решетками, повышающими качество теплообменников, что, в свою очередь, ставит новые технологические задачи, связанные с закреплением труб в трубных решетках при изготовлении и ремонте трубных пучков.
Эффективная технологическая управляемость служебными характеристиками соединений, в том числе и их коррозионной стойкостью, достигается разработанным автором настоящей работы механизмом продольно — прессового локализованного закрепления и на его основе целым рядом рациональных технологий образования неразъемных соединений. При этом используются универсальные конструкции тепло-обменных труб с профилированными законцовками и соответствующие им новые конструкции сборок соединяемых элементов.
Настоящая работа представляет собой законченный этап исследований, проводимый сотрудниками СГАУ имени академика С. П. Королева совместно с сотрудниками ООО «Ремонтно-механический завод» ЗАО НК ЮКОС — РМ.
Исследования выполнялись согласно программам хоздоговоров.
Результаты исследований позволили разработать научно-обоснованные рекомендации и технические требования на проектирование технологических процессов производства теплообменных труб с профилированными законцовками условия ТУ 1212−001−43 950 522−02 «Крепление труб с профилированными законцовками в трубных решетках теплообменных аппаратов» со сроком введения 01.06.2002 года, изготовлению оснастки и выбору оборудования, а также на выполнение операций закрепления труб в трубных решетках.
Практическим итогом работы явилось проектирование и изготовление специальных производственных комплексов для производства труб с профилированными законцовками, получения отверстия трубных решеток, а также изготовления трубных пучков для Новокуйбышевского и Самарского НПЗ, ООО «Этанол», ООО «Завод масел и присадок».
Материал настоящей работы докладывался на научно-технических конференциях г. г. Москвы, Самары и Орла, а также на НТС родственных предприятий городов Тольятти, Бугульмы, обсуждался со специалистами из Азербайджана, Казахстана и Германии.
На международной выставке «Нефть и Газ — 97» и «Нефть и Газ -2001» представленные результаты работы вызвали положительные отзывы отечественных и зарубежных специалистов: «Индреско» (США), «Китайнефтегаз» и др.
На состоявшейся в августе 2001 года презентации продукции ООО «Ремонтно-механический завод» новые технологические процессы закрепления труб в трубных решетках при изготовлении и ремонте тепло-обменных аппаратов получили одобрение со стороны специалистов заинтересованных предприятий (см. в приложении «Заключение о новых технологиях»).
Автор настоящей работы выражают глубокую благодарность своему научному руководителю, заслуженному деятелю науки РФ, д.т.н., профессору Гречникову Ф. В. и коллективу кафедры ОМД СГАУ имени академика С. П. Королева за её активное обсуждениегенеральному директору ООО «Ремонтно-механический завод» Батраеву Г. А. и инженерно-техническим работникам данного предприятия, Ивановой И. С., Марты-новой Е. В., Тамаровой О. Т., Христову В. Р., Иванникову Ю. Д., Глухову В. С., Землякову П. В., Дегтяреву Е. П., за помощь по освоению и внедрению новых разработок в производствосотрудникам ЦЗЛ, Анискиной В. И., Куликовой Н. А., Осипову Н. М., АО «Авиакор» за помощь в проведении испытаний, сотрудникам, отдела механизации и автоматизации АО «Авиакор» Иванову А. И., Копелевичу А. М., Долгушину С. И. за консультации, состоявшиеся в процессе выполнения настоящей работы.
Результаты работы послужили основанием для следующих выводов:
1. В результате низкого качества выполняемых соединений труб с трубными решетками, убытки, связанные с простоем нефтеперерабатывающих установок, превышают в 10. 15 раз стоимость самих дорогостоящих (100 тысяч руб./тонну и более) теплообменных аппаратов.
2. Впервые в практике закрепления труб в трубных решетках разработана методология и на её основе — блок технологических процессов продольно-прессового локализованного образования неразъемных соединений с повышенными и долговременными их служебными характеристиками (прочностные характеристики соединений превышают аналогичные характеристики трубы в исходном сечениидавление разгерметизации более 16 МПасрок межремонтного пробега трубных пучков при их бездефектной работе не менее 7,5 лет). Создана обобщенная технологическая модель, включающая перечень следующих операций: раздача трубы в сочетании с внеконтактной изгибной деформацией её полотнаосадка полотна трубы на поверхности трубного отверстия, прилегающей к торцу трубной решетки с образованием площадки контактадорнование отверстия трубы с поперечными сдвигами в её полотнеосадка торца трубы на лицевой поверхности трубной решетки.
3. Расчетными параметрами технологической модели закрепления труб в трубных решетках являются конструкции трубных отверстий (глубина и форма поперечного сечения кольцевой канавки, их количество, длина кольцевого пояска или поясков), профилированных законцовок (длина опорного участка и его консольной частидлина конического переходного участкадлина и форма поперечного сечения нагружаемого участка), длина выступания торца законцовки над лицевой поверхностью трубной решетки, силовые характеристики стадий закрепления, а также конечный диаметр трубы после её закрепления.
4. Разработаны технологические процессы получения профилированных законцовок для изготовления новых и трубных пучков ремонтного варианта. При этом достигается их единый типоразмер, что снижает потребность в инструменте по номенклатуре и его количеству.
5. Разработан и эксплуатируется на ООО «Ремонтно-механический завод» ЗАО НК ЮКОС-РМ универсальный производственный комплекс (с максимально развиваемым усилием в 400 кН) для выполнения операций закрепления трубы в трубном отверстии, выпрессовывания трубы из трубного отверстия при ремонте теплообменного аппарата, а также операции дорнования при получении отверстия в трубной решетке. Время выполнения одной операции 13−15 с.
6. Разработаны способы ускоренных испытаний, имитирующих влияние коррозии на внутренние слои трубы при параметрах эксплуатации трубных пучков, что позволяет прогнозировать их срок бездефектной работы.
7. Выпущены технические условия ТУ 1212−001−43 950 522−02 «Крепление труб с профилированными законцовками в трубных решетках те-плообменных аппаратов» со сроком введения 01.06.2002 года.
8. Изготовление 16-ти трубных пучков для ЗАО «Нефтехимическая компания» г. Новокуйбышевск обеспечило получение экономического эффекта в размере 29 600 рублей или 20,33 рубля экономии при закреплении каждой трубы в трубной решетке.
Результаты настоящих исследований вошли в состав конкурсной работы «Высокоэффективные технологии изготовления и ремШТа трубных пучков теплообменных аппаратов», удостоенной Губернской премии по Самарской области за 2001~тод. Разработанная методология продольно-прессового локализованного закрепления труб в трубных решетках позволяет расширить существующее положение о конструкциях трубных решеток с возможностью увеличения коэффициента их перфорированное&trade-. —'—.
Заключение
.
Настоящая работа выполнена с целью создания научно обоснованных высокоэффективных технологий продольно-прессового локализованного закрепления труб в трубных решетках теплообменных аппаратов.
Программа исследований, намеченная в соответствии с целью работы, выполнена полностью.
Список литературы
- Краснов В. И., Максименко М. 3. Ремонт теплообменников. М.: «Химия», 1990,104 е.-
- Юзик С. И. Развальцовка" труб в судовых теплообменных аппаратах. -Л.: Судостроение, 1978,144 е.-
- Мазуровский Б. Я. Элекгрогидроимпульсная запрессовка труб в трубных решетках теплообменных аппаратов. Киев: «Наукова думка», 1980,170 е.- — —
- Ткаченко Г. П., Бриф В. М. Изготовление и ремонт кожухотрубча-той теплообменной аппаратуры. М.: Машиностроение, 1980 т 160 е.-
- Отраслевой стандарт 26−02−1015−85. Крепление труб в трубных решетках. М.: Министерство химического и нефтяного машиностроения, 1985. 27 е.-
- Гладилин А. Н., Сторожевом. В., Попов В. А. и др. Технология металлов. М.: Машгиз, 1952. 709 е.-
- Андреев П. А., Гремилов~Д. И., Федорович Е. Д. Теплообменные аппараты ядерных энергетических установок. Л.: Судостроение, 1969.352 с.-
- Барит Г. Ю. Основы технологии судового машиностроения. Л.: Судостроение, 1972. 248 с: —
- Берлинер Ю. И., Балашов Ю. А. Технология химического и нефтяного аппаратостроения. -М: Машиностроение, 1976. 256 с: —
- Берлинер Ю. И., Бриф В. М. Анализ применимости современных методов крепления труб к трубным решеткам. Высокопроизводительные методы сварки в хим. и нефт. Машиностроении, Волгоград. 1970, вып. № 3, с. 3−12-
- Бриф В. М. Некоторые вопросы технологии развальцовки труб с ограничением крутящего момента. В кн.: Методы крепления труб в трубных решетках теплообменников. Волгоград, 1970, вып. № 3. с. 29−46-
- Деформация металлов взрывом /А. В. Крупин, В. Я. Соловьев. Н. И. Шефтель, А. Г. Кобел ев. М.: Металлургия, 1975.416 е.-
- Дорошенко П. А. Технология производства судовых парогенераторов и теплообменных аппаратов. Л.: Судостроение, 1972. 360с.-
- Зеленин В. А., Андреев В. А. Сварные соединения труб с трубными решетками в судовых теплообменных аппаратах. Л.: Судостроение, 1976. 83 е.-
- Колоколов Б. А. Исследование и разработка импульсного способа крепления труб ударом жесткого инструмента. В кн.: Высокопроизводительные методы сварки в хим. и нефт. машиностроении. Волгоград: Ниж. — Волж. ЦНТИ, 1970, вып. № 3, с. 125 130-
- Кононенко В. Г. Высокоскоростное формоизменение и разрушение металлов. Харьков: «Вища школа», 1980, 232 е.-
- Кононенко В. Г. Исследование влияния скорости деформации на коррозионную стойкость металлов. Самолетостроение и техника воздушного флота, 1965, № 4, с. 110−115-
- Кононенко В. Г., Колоколов Б. А. Внедрение импульсного способа развальцовки труб. Технология и организация производства, 1968, вып. № 5, с. 71−72-
- Кононенко В. Г., Колоколов Б. А. Исследование и внедрение импульсной развальцовки ударом жесткого тела. В кн.: Импульсная обработка металлов давлением, Харьков, 1970, вып. № 2, с. 110−122.
- Кузмак Е. М. Основы технологии аппаратостроения. М.: «Недра», 1967. 468 с.
- Луковкин А. И. Крепление труб в трубных досках паровых котлов и теплообменных аппаратов электрическими высоковольтными разрядами. Судостроение, 1959, вып. № 11. с. 40−43.
- Луковкин А. И. Новые вальцовочные соединения, полученные с применением энергии взрыва. Л.: ЛДНТП, 1968. 31 с.
- Луковкин А. И., Миронов Г. П. Высокопроизводительные методы сварки в хим. и нефт. машиностроении. Волгоград, 1970, вып. № 3, с. 108−117.
- Луковкин А. И., Семенов В. А. Технология закрепления труб в теплообменных аппаратах и котлах методом взрыва. Л.: ЛНДТП, 1968. 28 с.
- Мазуровский Б. Я. О развальцовке теплообменных аппаратов с малой степенью перфорации. КШП, 1974. вып. № 2, с. 22−24.
- Носков С. И. Оценка~ качества вальцовочных соединений по степени развальцовки. Технология судостроения, 1966, вып. № 1, с. 48−50
- Степанов В. Г., Шавров И. А. Высокоэнергетические импульсные методы обработки «мьлаллов. Ленинград: «Машиностроение», 1975. 280с.
- Степанов В. Г., Шавров И. А. Импульсная металлообработка в судовом машиностроении. Ленинград: «Судостроение», 1968. 254с.
- Степанов В. Г. Основы технологии развальцовки труб в судовых теплообменных аппаратах. -Л.: Судостроение, 1972. 208 с.
- Технология судостроения. /Под ред. В. Д. Мацкевича. Л.: Судостроение, 1971. 614 с.
- Опарин В. И., Ткаченко Г. П., Лукьянов В. П. Механизация производства химической и нефтяной аппаратуры. М: Машиностроение, 1973. 222 с.
- Черняк Я. С., Дуров В. С. Ремонтные работы на нефтеперерабатывающих и нефтехимических предприятиях. М.: «Химия», 1975. 264 с.
- Заявка № 3 328 913 ФРГ, МПК F28 F9/16, F16 F41/08. Устройство для закрепления втулки в отверстии. Опубл. 28.02.85, № 9.
- Унксов Е. П. Инженерная теория пластичности. М.: Машгиз, 1959. 328 с.
- А. с. № 592 421 СССР, МПК В21 D39/06.Cnoco6 закрепления труб в решетке теплообменника. /Юзик С. И./ опубл. 15.08:75, бюл. № 15//Открытия. Изобретения. -1976, № 15. с. 80
- А. с. № 592 341 СССР, МПК В21 D39/06.Cnoco6 закрепления труб в решетке теплообменника. /Богданов А. И. и др./опубл. 10.06.75, бюл. № 10/Юткрытия. Изобретения. -1976, № 13г- с. 50
- Заявка № 3 305 615 ФРГ, МПК В21 D39/06. Устройство для закрепления металлической трубы в отверстии металлической плиты с соединением их путем направленного взрыва. Опубл. 12.02.82. № 48. —'
- Заявка № 3 015 278 Франция, МПК В21 D39/06. Способ закрепления труб в перфорированной плите методом взрыва: Опубл. 29.10.81, № 44
- А. с. № 1 257 403 СССР, МПК F28 F9/16, В21 D39/06: Способ закрепления труб в решетке теплообменника. /Овечкин В. В., Орехов А. А. и др./ опубл. 10П2.83, бюл. № 10//0ткрытия. Изобретения, -1984, № 10.-е. 12
- А. с. № 691 673 ССеРгМПК F28 F9/16, В21 D39/06. Способ закрепления трубы в отверстии трубной решетки теплообменника. /Сапелкин В. С., Соловей^гИ. и др./, опубл. 15.10.79, бюлг№ 38-
- А. с. № 66 852 СССР, МПК F28 F9/16, F28 F11/02. Узел крепления трубы в отверстииггрубной решетки теплообменного аппарата. /Сапелкин В. С., Соловей А. И. и др./, опубл. 30.07.79, бюл. № 28- ~ —- ----
- А. с. № 794 355 СССР, МПК F28 F9/16, В21 D39/06. Способ закрепления трубы в отверстии трубной решетки теплообменника. /Сапелкин В. С., Соловей А. И. и др./, опубл. 07.01.81, бюл. № 1-
- А. с. № 1 099 211 СССР, МПК F28 Р9/16гУзел креплегте&гтрубы в отверстии трубной решетки теплообменника. /Мартынов А. С., Петровых В. И.,-Мартынов А./, опубл. 23.06.84, бюл. № 23г
- А. с. № 1 042 848 СССР, МПК В21 D39/06. Способ крепления трубы в отверстии трубной решетки. /Азенко Н. В./, опубл. 23.09.83, бюл. № 35-
- А. с. № 518 257 СССР, МПК В 21 D39/06. Способ соединения труб с трубными решетками. /Шевелев Г. Н., Тюрин В. Н., Шевелев А. Н./, опубл. 25.06.76, бюл. № 23-
- А. с. № 497 461 СССР, МПК F28 F9/16. Способ закрепления труб. /Ващилин В. Г., Черненко В. И., Семенов С. А/, опубл. 30.12.75, бюл. № 48-
- А. с. № 1 119 756 СССР, МПК В 21 D39/06. Способ крепления труб в трубных решетках теплообменных аппаратов. /Орехов А. В., Тевелев Л. Г., Юзик С. И., Овсянкин А. Н./, опубл. 23.10.84, бюл. № 39-
- Талыпов Г. Б. Исследование эффекта Баушингера. М.: Механика и машиностроение, 1964.121 е.-
- Талыпов Г. Б. Влияние микронапряжений, обусловливающих эффект Баушингера. На границы текучести и устойчивости при чистом сдвиге // Сб. «Исследования по упругости и пластичности». -Л.: ЛГУ, 1963, № 3-
- Талыпов Г. Б. Исследование эффекта Баушингера.// Изв. АН СССР «Механика и машиностроение», 1964, № 6-
- Каменцева 3. П. Эффект Баушингера при предварительных пластических деформациях разного знака. //Сб. «Исследования по упругости и пластичности». Л.: ЛГУ, 1963, № 3-
- Талыпов Г. Б. Анализ экспериментальных данных по эффекту Баушингера и их теоретическое истолкование. //Механика твердого тела, 1966, № 2-
- Васильев Д. М. О природе эффекта Баушингера. //Изв. вузов машиностроения, 1965, № 12-
- Талыпов Г. Б. К теории пластичности, учитывающей эффект Баушингера. //Механика твердого тела, 1966, № 6-
- Талыпов Г. Б. Пластичность и прочность стали при сложном нагружении. Л.: ЛГУ, 1968. 134 е.-
- Илюшин А. А. Пластичность. М.: Наука, 1948. 376 е.-
- Москвитин В. В. Циклические нагружения элементов конструкций. М.: Наука, 1981. 344 с.-
- Джонсон У., Меллор П. Теория пластичности для инженеров. Перевод с англ. М.: Машиностроение, 1979. 567 е.-
- Качанов Л. М. Основы теории пластичности. Изд. 2-е. М.: Наука, 1969.420 с.
- Смирнов Аляев Г. А. Сопротивление материалов пластическому деформированию. 3-е изд., перераб. и доп. Л.: Машиностроение, 1978. 368 с-
- Смирнов Аляев Г. А., Розенберг В. М. Метод микроструктурных изменений пластической деформации. — «Заводская лаборатория», 1951, вып. № 11, с. 1343−1352-
- Смирнов Аляев Г. А., Розенберг В. М. Теория пластической деформации металлов. М. — П.: Машгиз, 1956. 367 е.-
- Смирнов Аляев Г. А., Розенберг В. М. Технологический задачи пластичности. — Л.: Лениздат, 1951. 215 е.-
- Смирнов Аляев Г. А., Чикидовский В. П. Экспериментальные исследования в обработке металлов давлением. Л.: Машиностроение, 1972. 370 с.
- Ильюшин А. А. Об основах общей математической теории пластического течения. М.: АН СССР, 1961. 46 с.
- Рейнер М. Деформация и течение. Введение в реологию. (Пер. с англ.) М.: Изд-во иностр. лит-ры, 1963. 381 с.
- Малинин Н. Н. Прикладная теория пластичности и ползучести. Изд. 2-е. М.: Машиностроение, 1975.400 с
- Ильюшин А. А., Ленский В. С. Сопротивление материалов. М.: Физматгиз, 1959. 371 с.
- Качанов Л. М. Основы теории пластичности. М.: Гостехгео-ретиздат, 1956. 324 е.-
- Сторожев М. В., Попов Е. А. Теория обработки металлов давлением. М.: «Высшая школа», 1963. 388 е.- Сторожев М. В., Попов Е. А. Теория обработки металлов давлением. — М.: Машиностроение, 1971. 424 с.-
- Локализация деформации и её влияние на ход процессов обработки металлов давлением./ Пресняков А. А. //Проблемы прочности. 1994, № 2, с. 89−92-
- Выдрин В. И. Процесс прокатки волочения//Изв. Вузов. Черная металлургия. — 1970, № 5, с. 17−19-
- Пресняков А. А. Локализация пластической деформации. М.: Машиностроение, 1983. 56 е.-
- Дзугутов М. Я. Пластическая деформация высоколегированных сталей и сплавов. М.: Металлургия, 1977. 479 е.-
- Охрименко Я. М. Технология кузнечно-штампового производства. М.: Машиностроение, 1976. 560 е.-
- Пресняков А. А., Умурзаков Т. А., Дегтярева А. С. Шнуровая локализация деформаций.//Физ. Механика материалов. 1991, № 11, с. 155−160-
- Патент RU № 2 171 155 С 1, кл. В 21 D 39/06, 53/08, F 28 F 9/16. Способ закрепления труб в трубных решетках. /Батраев Г. А., Козий С. С. и др./ по заявке № 99 120 204, бюл. № 24 от 27.07.01.
- Патент RU № 2 173 231 С 2, кл. В 21 D 39/06, 53/08, F 28 F 9/16. Способ закрепления труб в трубных решетках. /Батраев Г. А., Козий С. С. и др./ по заявке № 99 121 593, бюл. № 25 от 10.09.01.
- Патент RU № 2 173 232 С 2, кл. В 21 D 39/06, 53/08, F 28 F 9/16. Способ закрепления труб в трубных решетках. /Батраев Г. А., Козий С. С. и др./ по заявке № 99 125 540, бюл. № 25 от 10.09.01.
- Патент RU № 2 174 886 С 2, кл. В 21 D 39/06, 53/08, F 28 F 9/16. Способ закрепления труб в трубных решетках. /Батраев Г. А., Козий С. С. и др./ по заявке № 99 122 430, бюл. № 29 от 20.10.01.
- Патент RU № 2 174 887 С 2, кл. В 21 D 39/06, 53/08, F 28 F 9/16. Способ закрепления труб в трубных решетках. /Батраев Г. А., Козий С. С и др./ по заявке № 99 123 133, бюл. № 29 от 20.10.01.
- Патент RU № 2 174 889 С 2, кл. В 21 D 39/06, 53/08, F 28 F 9/16. Способ закрепления труб в трубных решетках. / Козий С. С., Батраев Г. А. и др./ по заявке № 99 127 564, бюл. № 29 от 20.10.01.
- Патент RU № 2 163 851 С 1, кл. В 21 D 39/06. Способ получения теплообменных труб. /Батраев Г. А., Козий С. С. и др./ по заявке № 99 113 055, бюл. № 7 от 10.03.01.
- Патент RU № 2 177 854 С 2, кл. В 21 D 39/06. Способ закрепления труб в трубных решетках. /Козий С. С., Батраев Г. А. и др./ по заявке № 99 123 982, бюл. № 1 от 10.01.02.
- Патент RU № 2 170 153 С 2, кл. В 21 D 39/06, 53/08, F 28 F 9/16. Способ закрепления труб в трубных решетках. /Батраев Г. А., Козий С. С. и др./ по заявке № 99 114 359, бюл. № 19 от 10.07.01.
- Патент RU № 2 170 635 С 2, кл. В 21 D 39/06, 53/08, F 28 F 9/16. Способ закрепления труб в трубных решетках. / Батраев Г. А., Козий С. С. и др./ по заявке № 99 119 623, бюл. № 6 от 27.02.02.
- Патент RU № 2 179 903 С 1, кл. В 21 D 39/06. Способ закрепления труб в трубных решетках. /Козий С. С, Батраев Г. А., и др./ по заявке № 2 000 113 151, бюл. № 2 от 20.01.01.
- Патент RU № 2 177 852 С 2, кл. В 21 D 39/06. Способ закрепления труб в трубных решетках. /Козий С. С., Батраев Г. А. и др./ по заявке 2 000 102 498, бюл. № 1 от 10.01.02.
- Патент RU № 2 174 889 С 2, кл. В 21 D 39/06, 53/08, F 28 F 9/16. Способ закрепления труб в трубных решетках. /Козий С. С., Батраев Г. А. и др./ по заявке № 991 277 564, бюл. № 29 от 20.10.01.
- Патент RU № 2 174 888 С 2, кл. В 21 D 39/06, 53/08, F 28 F 9/16. Способ закрепления труб в трубных решетках. / Батраев Г. А., Козий С. С. и др./ по заявке № 99 123 235, бюл. № 29 от 20.10.01.
- Патент RU № 2 177 853 С 2, кл. В 21 D 39/06. Способ закрепления труб в трубных решетках. /Козий С. С., Батраев Г. А. и др./ по заявке № 2 000 110 552, бюл. № 1 от 10.01.02.
- Патент RU № 2 182 055 С 2, кп. В 21 D 39/06. Способ закрепления труб в трубных решетках. /Козий С. С., Батраев Г. А. и др./ по заявке № 2 000 113 992, бюл. № 13 от 10.05.02.
- Патент RU 3 2 182 056 С 1, кл. В 21 D 39/06. Способ закрепления труб в трубных решетках. /Батраев Г. А., Козий С. С. и др./ по заявке № 2 000 115 159, бюл. № 13 от 10.05.02.
- Патент № 2 177 851 С 2, кл. В 21 D 39/06, 53/08, F 28 F 9/16. Способ закрепления труб в трубных решетках. / Батраев Г. А., Козий С. С. и др./ по заявке № 2 000 102 497, бюл. № 1 от 10.01.02.
- Патент № 2 168 385 С 2, кл. В 21 D 39/06, 53/08, F 28 F 9/16. Способ закрепления труб в трубных решетках. / Батраев Г. А., Козий С. С. и др./ по заявке № 99 112 252, бюл. № 16 от 10.05.01.
- Патент RU № 2 169 630 С 1, кл. В 21 D 39/06, 53/08, F 28 F 9/16. Способ закрепления труб в трубных решетках. / Батраев Г. А., Козий С. С. и др./ по заявке № 99 118 810, бюл. № 18 от 27.06.01.
- Патент RU № 2 169 631 С 1, кл. В 21 D 39/06, 53/08, F 28 F 9/16. Способ закрепления труб в трубных решетках. / Батраев Г. А., Козий С. С./ по заявке № 99 118 812, бюл. № 18 от 27.06.01.
- Патент RU № 2 171 154 С 2, кл. В 21 D 39/06, 53/08, F 28 F 9/16. Способ закрепления труб в трубных решетках. / Батраев Г. А., Козий С. С. и др./ по заявке № 99 118 811, бюл. № 21 от 27.07.01.
- Патент RU № 2 165 325 С 2, кл. В 21 D 39/06. Способ закрепления труб в трубных решетках. /Батраев Г. А., Козий С. С. и др./ по заявке № 99 108 941, бюл. № 11 от 20.04.01.
- Остаточные напряжения//Сб. статей под ред. Осгуда. М.: ИЛ, 1957. 50 е.-
- Биргер И. А. Остаточные напряжения. М.: Машиностроение, 1963.120 с.-
- Годерзиан К. К. Внутренние напряжения в металлах и сплавах. Методы их измерения и устранения. М.: ВНИИЦВЕТМЕТ, 1962. с. 15−20-
- Витман Ф. Ф. Остаточные напряжения. ГТТИ, 1933-
- Гликман Л. А. Остаточные напряжения в металлах. Докторская диссертация.-Ленинград, 1947-
- Вавичев М. А. Методы определения внутренних напряжений. -М.: АН СССР, 1955-
- Абрамов В. В. Остаточные напряжения и деформации в металлах. М.: Машгиз, 1963.120 е.-
- Кобрин М. М., Дехгярь Л. И. определение внутренних напряжений в цилиндрических деталях. М.: Машиностроение, 1965. 157 е.- Кудрявцев И. В. Внутренние напряжения как резерв прочности в машиностроении. — М.: Машгиз, 1951.67 е.-
- Кравченко В. А. Силы, остаточные напряжения и трение при резании. Куйбышев, 1962. 35с.
- Новый механизм закрепления труб в трубных решетках. /Батраев Г. А., Гречников Ф. В., Козий С. С. и др.//Химическое и нефтегазовое машиностроение. № 9−10,1998, с. 64−66.
- Особенности изготовления теплообменных труб с профилированными законцовками. /Батраев Г. А., Козий С. И., Гречников Ф. В., Козий С. С.//Химическое и нефтегазовое машиностроение. № 5, 1999, с. 41−43.148
- Колмогоров В. Л. Механика обработки металлов давлением. М.: Металлургия, 1986. 688 с.
- Способы гидравлических испытаний на плотность вальцовочных соединений защищены заявками на изобретение, имеющими положительное решение ВНИИГПЭ № 2 001 104 053.
- Способы гидравлических испытаний на плотность вальцовочных соединений защищены заявками на изобретение, имеющими положительное решение ВНИИГПЭ № 2 001 104 059.
- Способы гидравлических испытаний на плотность вальцовочных соединений защищены заявками на изобретение, имеющими положительное решение ВНИИГПЭ № 2 001 104 797.
- Шмыков А. А. Справочник термиста. М.: Машгиз, 1961, 392 с.
- ОСТ 26−17−01−83. Аппараты теплообменные и аппараты воздушного охлаждения. Стандартные технические требования к развальцовке труб с ограничением крутящего момента. М.: Издательство стандартов, 1984, 36 с.
- Аверкиев Ю. А., Аверкиев А. Ю. Технология холодной штамповки. М.: Машиностроение, 1989. — 604 е.-
- Любвин В. И. Обработка металлов радиальным обжатием. -М.: Машиностроение, 1975. -238 е.-
- Радюченко Ю. С. Ротационная ковка. М.: Машиностроение, 1962.-250 е.-
- Радюченко Ю. С. Ротационное обжатие. М.: Машиностроение, 1972.-176 с.
- Попов Е. А. Основы теории листовой штамповки. М.: Машиностроение, 1968. — 420 с.
- Паспорт СВ М1А -ООО — НС. 1980. 32 с.149